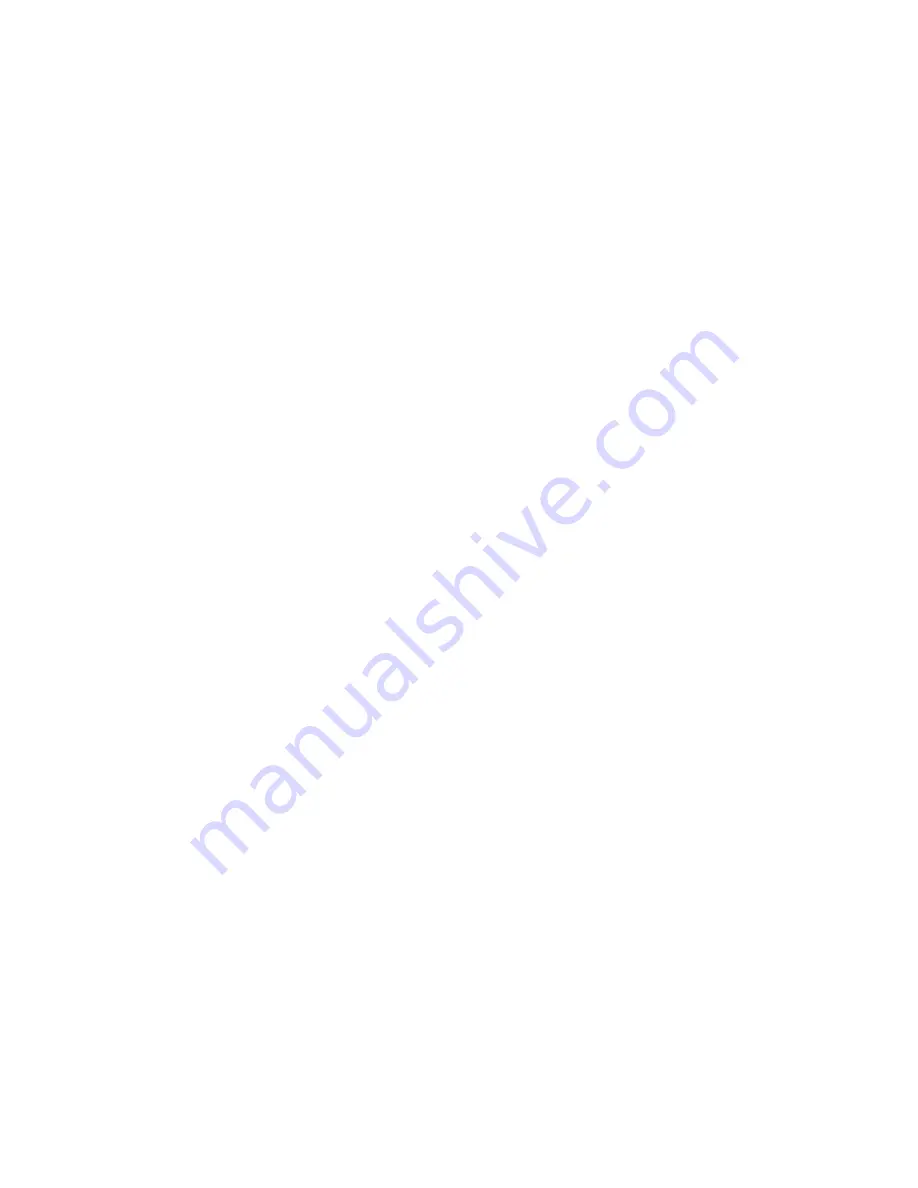
Loctite
®
is a registered trademark of Loctite Corp.
Motor Assembly/Disassembly Instructions – 3" Dynabuffer (cont.)
8.
Refer to the exploded view of the
55170
Flow Control Assembly to identify the parts and their proper order of assembly. Care should be taken when installing the
55169
Stem and
01024
O-Rings into the
55168
Inlet Adapter to prevent the lead O-Ring from shearing as it passes over the cross hole in the
55168
Inlet Adapter.
Apply a small amount of Vaseline to the O-Rings insert a 5/32" (4mm) hex wrench into the
55169
Stem and then slowly twist the stem as you gently push the Stem
into position. Secure the Stem with
95558
Retaining Ring.
9.
After threaded surfaces have been properly cleaned and primed, apply a small amount of Loctite #567 (or equivalent) to the external threads of the
55168
Inlet
Adapter. Install the
55170
Flow Control Assembly onto to the
45252
Throttle Body Housing. (Torque to 28 N•m/250 in. lbs.)
10.
Install the
95492
Screws into the two handle bosses in the
55160
Housing.
11.
With the throttle body mounting thread pointing up, position
95492
Screws between the vise jaws and secure the
55160
Housing in the vise.
NOTICE: Do not over tighten the vise.
12.
Install the
45267
Insert (smaller diameter end first) into the
45252
Throttle Body Housing.
13.
Apply a small amount of Vaseline to the
95523
O-Ring and install it onto the
45267
Insert.
14.
After threaded surfaces have been properly cleaned and primed, apply a small amount of the Loctite #567 (or equivalent) to the threads of the
55160
Housing. Install
the Throttle Body Housing assembly onto the
55160
Housing. Position the throttle lever assembly to the desired location and use a “Wide-Open” smooth jaw
adjustable, or a 34 mm open-end wrench to tighten the throttle body. NOTICE: LEFT HAND THREAD, Turn counterclockwise. (Torque to 45 N•m/400 in. lbs.)
15.
Slide the
01547
Collar back onto the throttle body lock nut.
Throttle Body Assembly Complete.
Shroud Assembly:
1.
Install the two
55161
O-Rings into the inner and outer shrouds.
2.
Install the
55158
Muffler Insert into the outer shroud.
3.
Fit and install the inner shroud into the outer shroud. Rotate the inner shroud to interlock with the outer shroud.
4.
Apply a small amount of Vaseline to the
55161
O-Rings.
5.
Push the shroud assembly onto the
55160
Housing. Rotate the shroud assembly to line-up the four mounting holes in the shroud with the four threaded holes in the
55160
Housing.
6.
NOTICE: Install the air motor before continuing with the shroud assembly. SEE: Motor Assembly (Steps 13 – 18) for air motor installation instructions.
7.
After threaded surfaces have been properly cleaned and primed, apply a small amount of the Loctite #567 (or equivalent) to the threads of the four
97101
Screws.
Use the
95050
Hex Key (5/64") to install.
8.
Install the
97166
Hang Plate. NOTICE: Insert the throttle body through the large opening in the
97166
Hang Plate and pull it into position around the
55160
Housing
and above the shroud.
Shroud Assembly Complete.
Motor Assembly:
1.
Install the
95630
Snap Ring onto the
57069
Balancer Shaft.
2.
Install the
59084
V-Seal onto the balancer shaft so that it fits down past the step on the balancer shaft.
NOTICE: The flat side of the v-seal must face the
56052
Bearing.
3.
After threaded surfaces have been properly cleaned and primed, apply a small amount of the Loctite #271 (or equivalent) to the bearing surface of the balancer shaft.
4.
Face the seal side of the
56052
Bearing toward the flat side of the
59084
V-Seal. Use the
57091
Bearing Press Tool and the
96232
Arbor Press (#2) to push the
bearing down to the step on the
57069
Balancer Shaft.
5.
After threaded surfaces have been properly cleaned and primed, apply a small amount of Loctite #271 (or equivalent) to the outside diameter of the
56052
Bearing,
and install the balancer shaft/bearing assembly into the
55153
Shaft Balancer.
6.
CAUTION: To avoid injury during the final installation of the
95630
Snap Ring, it is best to secure the counterbalance in a vise. Use a small thin screw driver to install
the snap ring. Install the
95630
Snap Ring between the hex end of the balancer shaft and the flat side of the
59084
V-Seal. The snap ring must fit into the groove on
the inside diameter of the
55153
Shaft Balancer.
7.
Install the
55154
Lock Ring, and the
55155
Lock Ring Spacer onto the
55153
Shaft Balancer. Use the smaller diameter end of the
57091
Bearing Press Tool and the
arbor press to push the
02695
Bearing down to the top of the counterbalance on the shaft balancer. Install the
55152
Front Bearing Plate in the same manner.
8.
Install the
54673
Key into the
55153
Shaft Balancer.
9.
Apply the
95842
Dynabrade Air Lube 10W/NR (or equivalent) to the vanes. Install the
54671
Rotor and
54674
Vanes (5/pkg.).
10.
Position the
55151
Cylinder Assembly so that the short line-up pin side fits against the
55152
Front Bearing Plate.
11.
Install the
54679
Rear Bearing Plate and the
01206
Bearing onto the
55153
Shaft Balancer. NOTICE: The
01206
Bearing is a slip fit into the
54679
Rear Bearing
Plate. Use the smaller diameter end of the
57091
Bearing Press Tool and the arbor press to push the bearing and plate down until the rear bearing plate just touches
the
55151
Cylinder Assembly. This should create a snug fit between the bearing plates and the cylinder.
12.
Use the
96343
Retaining Ring Pliers to install the
95626
Retaining Ring with the curve of the ring arched up. Push the sides of the retaining ring down into the groove
at the top of the shaft balancer.
13.
After threaded surfaces have been properly cleaned and primed, apply a small amount of the Loctite #567 (or equivalent) to the threads of the
55154
Lock Ring.
14.
Grasp the counterbalance of the motor assembly. Sight the end of the
95865
Pin with the line-up hole on the inside of the
55160
Housing. Carefully install the motor
assembly into the
55160
Housing so that the
95865
Pin fits into the line-up hole. By hand, use the
56058
Lock Ring Tool to turn the lock ring clockwise into the
housing. If resistance is felt, stop and realign the motor assembly. If the motor assembly is aligned correctly, the lock ring and the motor should advance into
the housing easily.
15.
Install the
95492
Screws into the two handle bosses in the
55160
Housing.
16.
With the shaft balancer (counterbalance) facing up, position
95492
Screws between the vise jaws and secure the
55126
3" Dynabuffer in the vise.
NOTICE: Do not over tighten the vise.
17.
Use the
56058
Lock Ring Tool to secure the
55154
Lock Ring and motor assembly into the
55160
Housing. (Torque to 28 N•m/250 in. lbs.)
18.
Use the
95050
Hex Key (5/64") to install the four
97101
Screws to secure the shroud assembly.
19.
Use the
59293
Offset Wrench (26 mm) to install the back-up pad.
Motor Assembly Complete. Tool Assembly Complete.
Throttle Lever Positioning Procedure:
1.
Use the
59293
Offset Wrench (26 mm) to remove the back-up pad.
2.
Install the
95492
Screws into the two handle bosses in the
55160
Housing.
3.
With the air inlet pointing up, position
95492
Screws between the vise jaws and secure the
55126
3" Dynabuffer in the vise.
NOTICE: Do not over tighten the vise.
4.
Slide back the
01547
Collar onto the
45206
Housing Sleeve. NOTICE: Do not to entirely separate the
45252
Throttle Body Housing from the
55160
Housing. Use a
“Wide-Open” smooth jaw adjustable, or a 34 mm open-end wrench to loosen the throttle body lock nut. LEFT HAND THREAD, Turn clockwise.
5.
By hand, with a firm grasp on the throttle Body, rotate the throttle body and position the throttle lever assembly to the desired location.
6.
Maintain a firm grasp of the throttle body to prevent rotation, and tighten the lock nut.
NOTICE: LEFT HAND THREAD, Turn counterclockwise. (Torque to 45 N•m/400 in. lbs.)
Throttle Lever Positioning Procedure Complete.
Additional Information: It is important to determine that the tool is working properly and safely before applying the tool to the work.
Place 2-3 drops of the 95842 Dynabrade Air Lube 10W/NR (or equivalent) directly into the air inlet with throttle lever depressed. Follow tool speed check procedure outlined
in Routine Preventative Maintenance section on page 3.
6