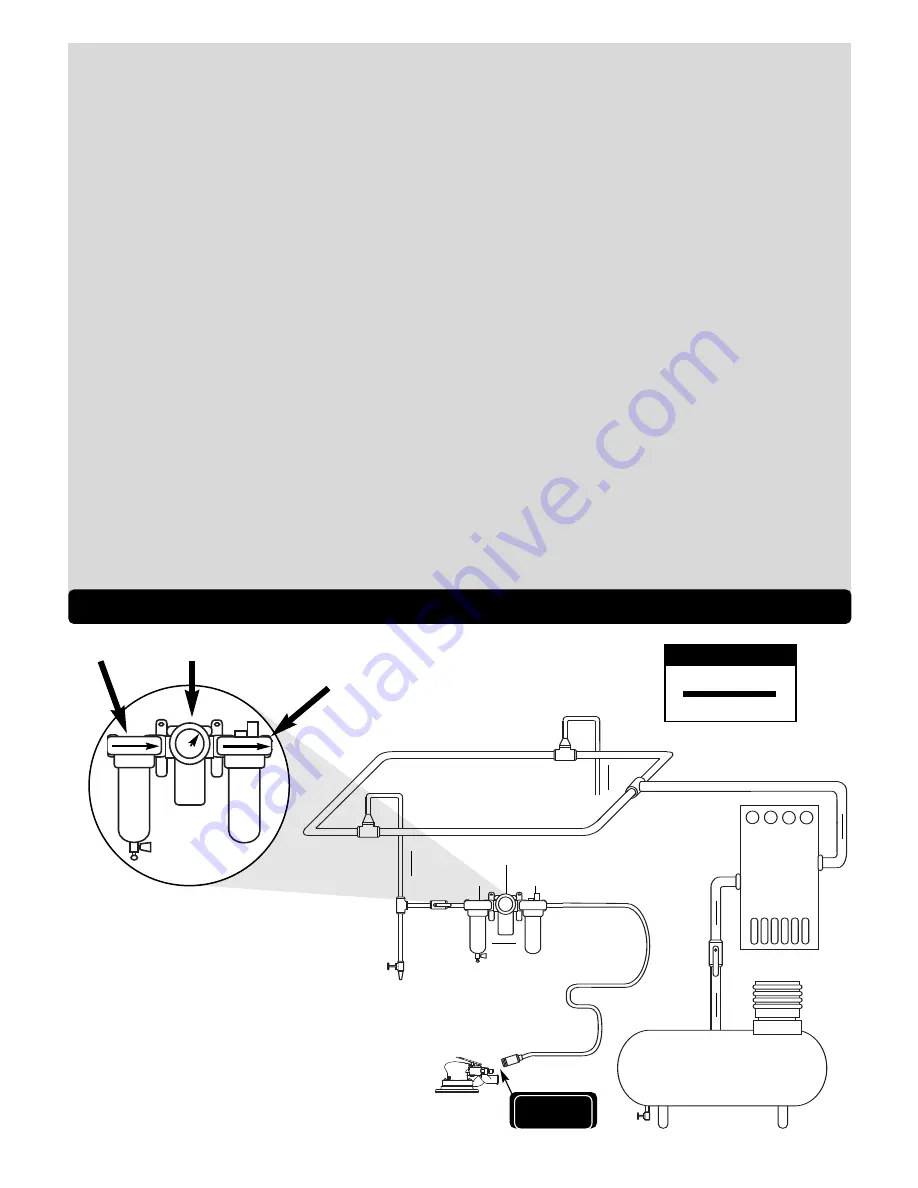
2
To Tool Station
Closed Loop Pipe System
(Sloped in the direction of air flow)
Ball
Valve
Ball
Valve
Filter
Regulator
Lubricator
Air Flow
Drain
Valve
Drain
Valve
Air Tool
Air Compressor
and Receiver
Drain
Valve
Air Hose
Air Flow
Refrigerated
Air Dryer
Filter
Regulator
Lubricator
90 PSIG
(6.2 Bar)
SAFETY INSTRUCTIONS (Cont.)
• Use only recommended accessories. See back page of manual and Dynabrade Literature.
• Before mounting an accessory, visually inspect for defects. Do not use defective accessories.
• Follow tool specifications before choosing size and type of accessory.
• Only use recommended fittings and air line sizes. Air supply hoses and air hose assemblies must have a minimum working pressure rating of 150 PSIG (10 bars, g) or 150
percent of the maximum pressure produced in the system, whichever is higher. (See Tool Machine Specifications Table.)
OPERATING INSTRUCTIONS
Warning:
Always wear eye protection. Operator of tool is responsible for following: accepted eye, face, respiratory, hearing and body protection.
Caution:
Hand, wrist and arm injury may result from repetitive work, motion and overexposure to vibration.
Caution:
Be sure that any loose clothing, hair and all jewelry is properly restrained.
• Install air fitting into inlet bushing of tool. Important: Secure inlet bushing of tool with a wrench before attempting to install the air fitting to avoid damaging
valve body housing.
• BEFORE MOUNTING AN ACCESSORY, after all tool repairs and whenever a tool is issued for use, check tool OPM (speed) with tachometer with air pressure set at 90
PSIG while the tool is running. This tool is an orbital tool, checking the OPM requires either a strobe or magnetic tachometer. If tool is operating at a higher speed than the
RPM marked on the tool housing, or operating improperly, the tool must be serviced and corrected before use.
Caution:
Tool RPM / OPM must never exceed abrasive/accessory RPM / OPM rating. Check accessory manufacturer for details on maximum operating speed or
special mounting instructions.
• With power source connected at the air tool relieve hose of air pressure and disconnect tool from air supply when changing recommended accessories.
• Connect air tool to power source. Be careful NOT to depress throttle lever in the process.
Do not expose air tool to inlet pressure above 90 PSIG or (6.2 Bars).
Caution:
After installing the accessory, before testing or use and/or after reassembling tool, the tool must be started at a reduced speed to check for good balance. Gradually
increase tool speed. DO NOT USE if tool vibration is excessive. Correct cause, and retest to insure safe operation.
• Use only appropriately sized abrasive sanding sheets properly secured and aligned to the backing pad provided with the air sander.
• When applying the sander to a work surface
start-on
and
stop-off
when completed.
• Make sure that work area is uncluttered, and visitors are at a safe range from the tools and debris.
• Potentially explosive atmospheres can be caused by dust and fumes resulting from sanding or grinding. Always use dust extraction or suppression systems which are
suitable for the material being processed.
• Proceed with caution in unfamiliar surroundings. Hidden hazards may exist, such as electricity or other utility lines.
• Use only Dynabrade weight-mated pads to maintain low vibration levels.
• Use a vise or clamping device to hold work piece firmly in place.
• Work may generate hazardous dust.
• Do not apply excessive force on tool or apply “rough” treatment to it.
• Always work with a firm footing, posture and proper lighting.
• Ensure that sparks and debris resulting from work do not create a hazard.
• This tool is rear exhaust. Exhaust may contain lubricants, vane material, bearing grease, and other materials flushed through the tool.
Report to your supervisor any condition of the tool, accessories, or operation you consider unsafe.
Air System
1
DROP/MIN.
20
SCFM
LUBRICATOR SETTING
•
Dynabrade Air Power Tools are designed to
operate at 90 PSIG (6.2 Bar/620 kPa) maximum
air pressure at the tool inlet, when the tool is
running. Use recommended regulator to control
air pressure.
•
Ideally the air supply should be free of moisture.
To facilitate removing moisture from air supply, the
installation of a refrigerated air dryer after the
compressor and the use of drain valves at each
tool station is recommended.
➤
➤
➤
➤
➤
➤
90 PSIG MAX
(6.2 Bar)