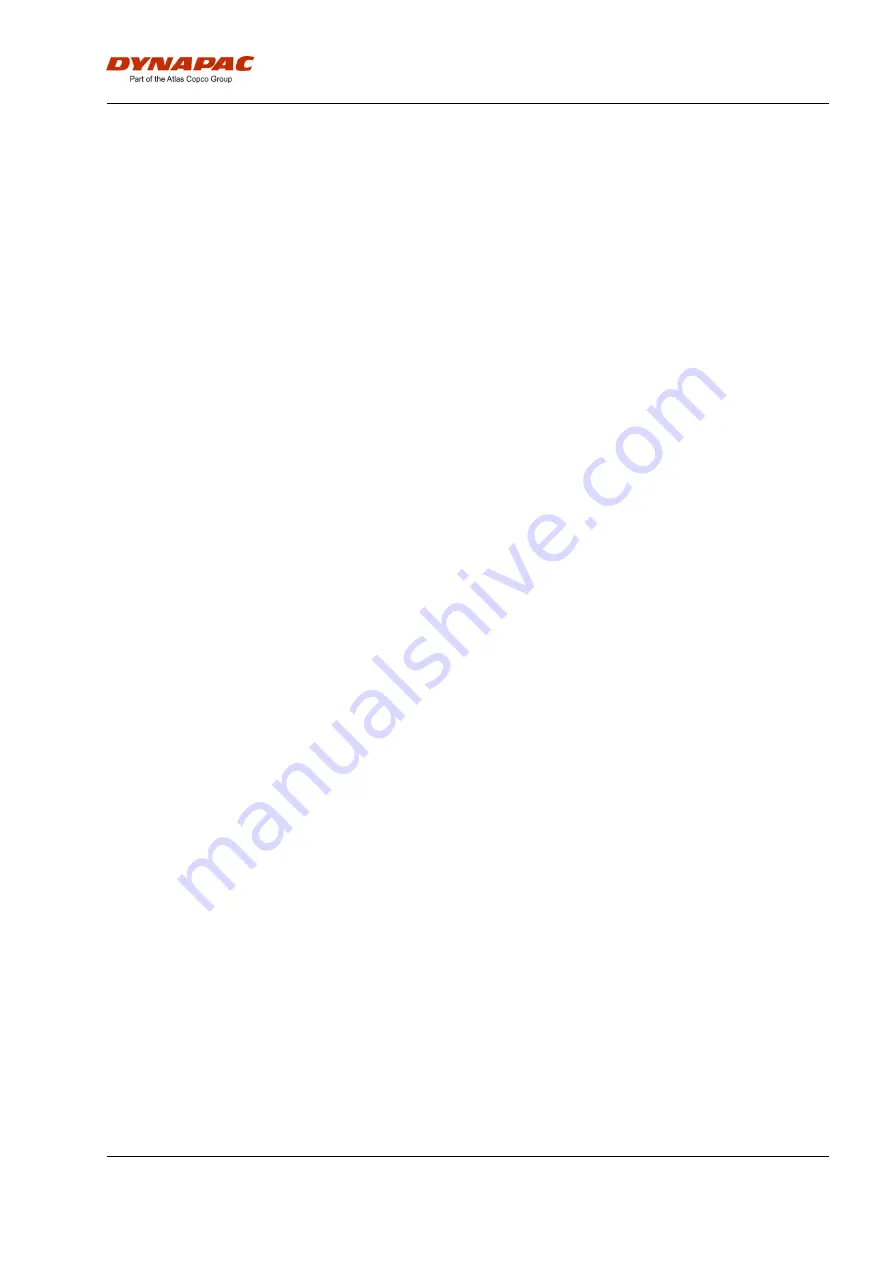
Preventive maintenance
IPL350TD-1EN2.pdf
2012-06-18
Preventive maintenance
Complete maintenance is necessary for the machine
to function satisfactorily and at the lowest possible
cost.
The Maintenance section includes the periodic
maintenance that must be carried out on the machine.
The recommended maintenance intervals assume that
the machine is used in a normal environment and
working conditions.
Acceptance and delivery inspection
The machine is tested and adjusted before it leaves
the factory.
On arrival, before delivery to the customer, delivery
inspection must be conducted as per the check list in
the warranty document.
Any transport damage must be immediately reported
to the transport company.
Warranty
The warranty is only valid if the stiplulated delivery
inspection and the separate service inspection have
been completed as per the warranty document, and
when the machine has been registered for starting
under the warranty.
The warranty is not valid if damage has been caused
by inadequate service, incorrect use of the machine,
the use of lubricants and hydraulic fluids other than
those specified in the manual, or if any other
adjustments have been made without the requisite
authorisation.
63
Summary of Contents for PL350 TD
Page 2: ......
Page 16: ...Safety Optional IPL350TD 1EN2 pdf 2012 06 18 8 ...
Page 20: ...Special instructions IPL350TD 1EN2 pdf 2012 06 18 12 ...
Page 66: ...Long term parking IPL350TD 1EN2 pdf 2012 06 18 58 ...
Page 72: ...Preventive maintenance IPL350TD 1EN2 pdf 2012 06 18 64 ...
Page 96: ...Maintenance 250h IPL350TD 1EN2 pdf 2012 06 18 88 ...
Page 106: ...Dynapac Compaction Equipment AB Box 504 SE 371 23 Karlskrona Sweden ...
Page 107: ...Dynapac Compaction Equipment AB Box 504 SE 371 23 Karlskrona Sweden ...