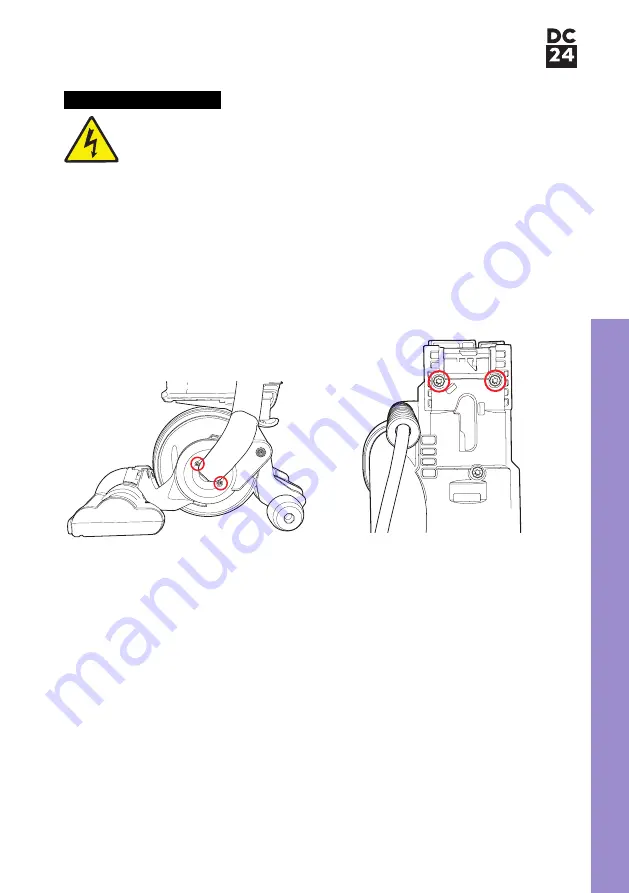
Technical info.
Service manual
02
Electrical safety testing
Ensure that at all times during the repair and testing of products
that customers, pets, children and you are not exposed to any
Live electrical supply.
Insulation test
The following tests
must
be performed
prior to and upon completion of all
repairs to Dyson floorcare products and
before
any functional checks.
You must
ensure that a full visual inspection
of the product is completed prior to
repair.
Test results
An insulation test reading of >2 M
Ω
is acceptable.
A reading of below 2 M
Ω
is not considered
safe and further investigation, rectification
and testing must be completed before the
product is used. The following components
must be visually inspected:
The wiring behind the upright switch
•
cover.
All wiring behind the switch housing.
•
If you cannot repair a product with an
insulation test reading of below 2M
Ω
you must inform the customer that the
product is unsafe to use.
Please inform the customer of the
required actions to repair the product
(including the charge structure).
If the product is left un-repaired please
indicate on your paperwork/hand held
device that the product is electrically
unsafe and attach a ‘WARNING:
product electrically unsafe’ sticker in
a visable location on the product.
The Seaward Primetest 200 (or equivalent)
should be used to test the electrical
insulation of a Class 11 appliance; it
indicates any electrical leakage.
Test the two screws highlighted in the
upright switch cover.
Test the two screws highlighted in the
rear of the duct assembly.
Insulation test points:
These tests are vital to avoid any
possibility of personal injury to the
end user.