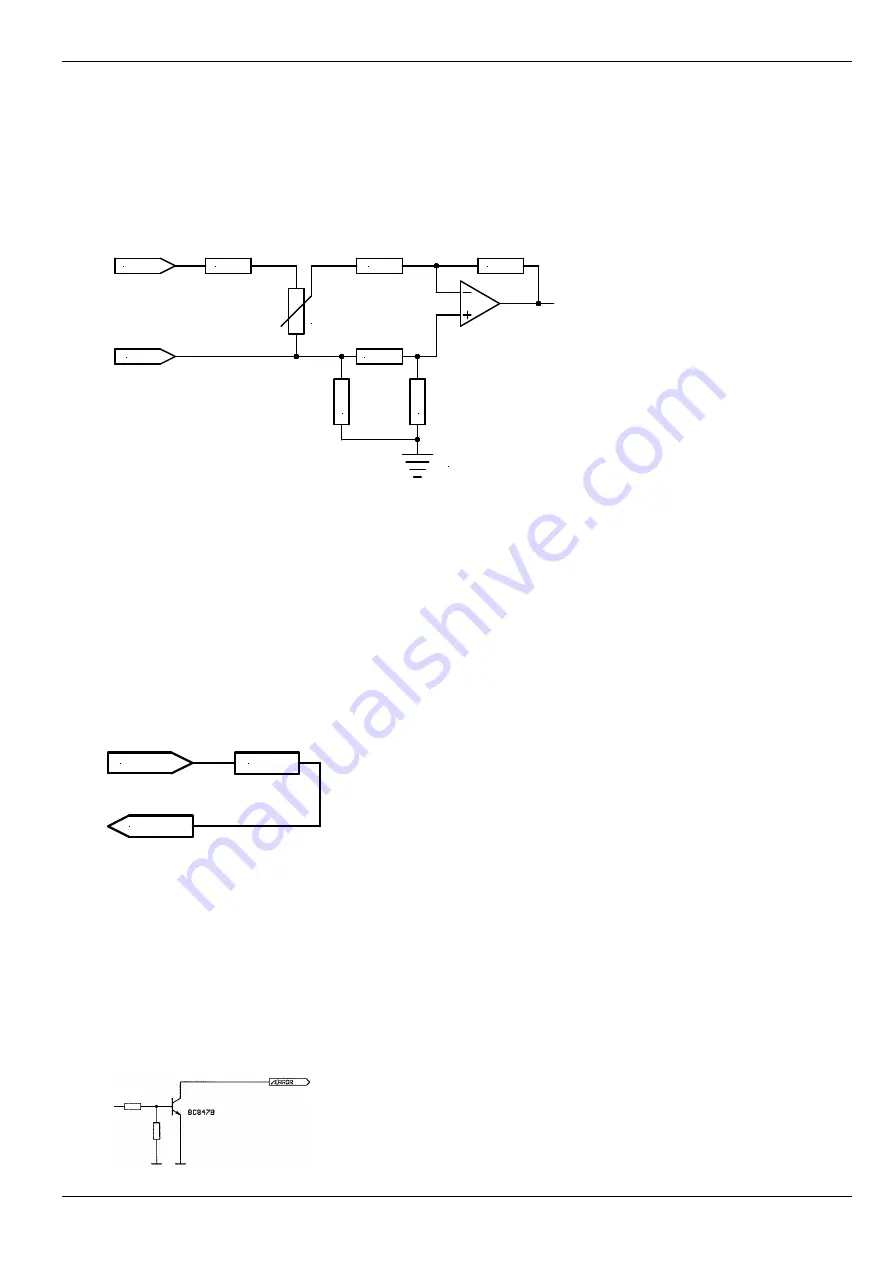
Manual SCA-SE-30-06
V 0.9
10/02 page 5
e-motion Gesellschaft für Antriebstechnik mbH, Zettachring 2, D-70567 Stuttgart, Germany
Tel.: +49-(0)711-7221535, Fax.: +49-(0)711-7221548 E-mail: mgmt@e-motion-controls.com
4.1.3. + Tacho (5)
4.1.4. – Tacho (6)
Due to the operating mode encoder feedback, the outputs of the encoder to tacho conversion stage
have to be connected to these inputs.
Input impedance:
50 kOhm
Maximum input voltage:
50 V
Input connection tacho:
+Tacho
-Tacho
1k
33k
100k
33k
50k
100k
4k7
GNDA
4.1.5. + Vcc (3)
4.1.6. Power GND (4)
Power supply connector.
Caution: DO NOT c Vcc and Power GND to the o Motor or - Motor.
4.2. Outputs
4.2.1. Auxiliary voltage output V (13)
The auxiliary voltage output V provides a low-resistant connection to pin + Vcc (3).
+Vcc
V
1k
4.2.2. Supervising report Error Out (11)
The error-signal is to show the status of the drive and can be used to provide a feedback signal to
other devices and controls. The open-collector is normally turned off which means the output is
pulled to a positive level by the means of an external resistor. In case of a fault or if the drive is
disabled (input
Enable In (14)
not connected to an external positive voltage > 11 V) the output is
pulled to GND.
Input voltage range: max. 30 V DC
Load current:
< 20 mA
Output connection Error: