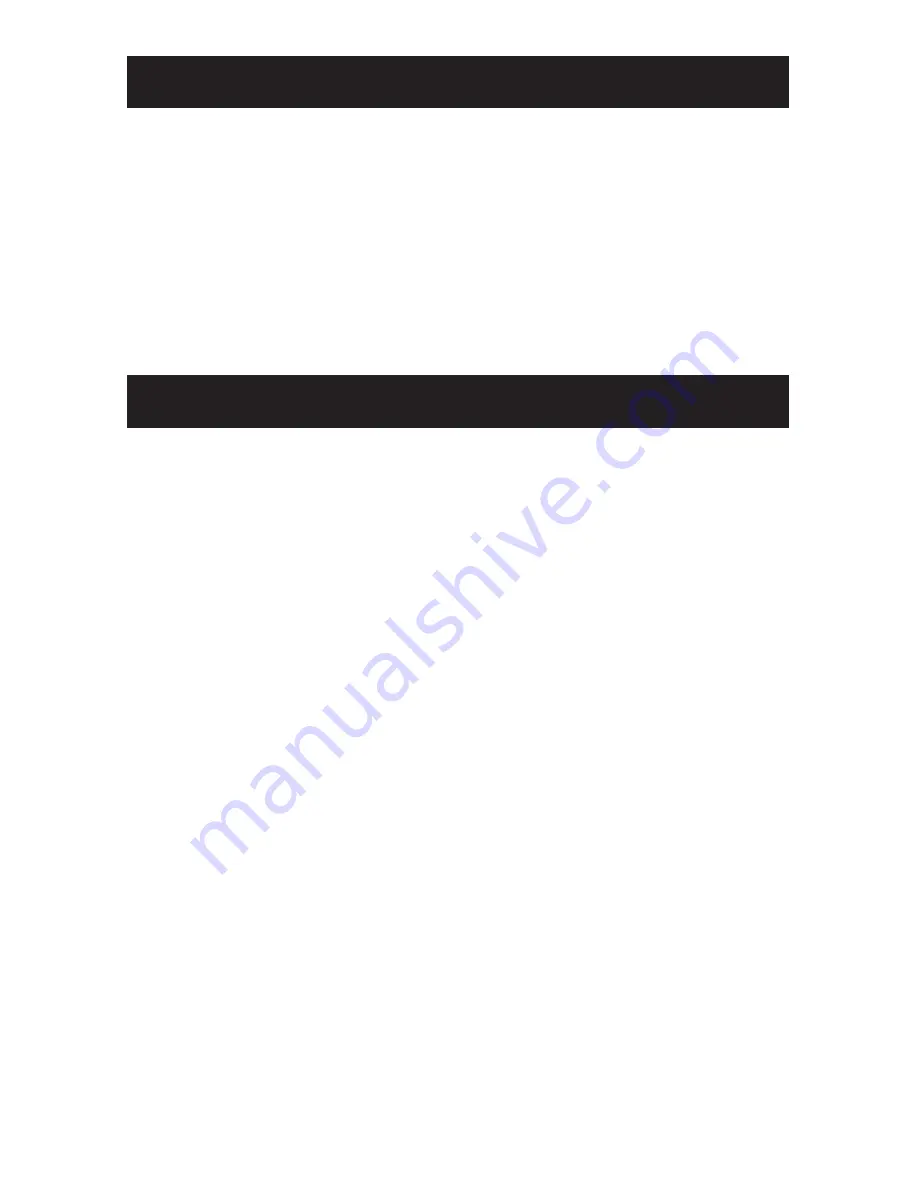
Eagle Solutions, ©2008, Tracker Operator Manual Page #8
Eagle Solutions, ©2008, Tracker Operator Manual Page #9
• Operator must have completed certification
training before using machine.
• Proper maintenance is the responsibility of the
operator before use of machine. This includes:
checking the oil level, checking and cleaning
air and dust filters, keeping machine clean and
lubricated, inspect for damaged, worn or loose
parts, clean carburetor air filters (and as needed
during operation), clean entire machine after
each use.
• Sweep floor and check for items protruding out
of the floor surface before operating machine.
• Do not start engine with the transport wheel
attached, if applicable.
• Do not allow the machine to run unattended or
be tilted back while it is running.
• Exhaust parts are extremely HOT. Be careful
not to allow them to come into contact with
anything or anyone.
• Do not attempt to change pads or abrasives
while the engine is running.
• Exercise extreme caution when installing
or changing pads or abrasive material. The
machine is very heavy!
• Maintain proper room ventilation.
• Do not stand on the machine.
• Stop the engine by closing the service valve on
the fuel cylinder.
• Remove the key from the switch, if applicable,
to prevent unauthorized use.
• Remove the fuel cylinder from the machine and
store it outside in a secure approved cabinet.
• Servicing or adjusting the propane fuel system
should only be done by a trained service
technician. Never attempt to adjust the fuel
system of a propane engine! If equipped with
an emission monitoring or controlling system
never attempt to disconnect it or circumvent it!
• Never attempt to bypass or disconnect the kill
switch or any other safety devices.
• Liquefied propane will expand 270 times to
flammable vapor - avoid needless release
of liquefied propane and using overfilled
cylinders.
• Propane is heavier than air – if it leaks it will
spread in low places like under doors where it
may be ignited and cause damage.
• Only use 4E240 cylinders that are approved
by the DOT - never use cylinders designed for
other services like barbecues.
• The low boiling point of propane can cause
serious frostbite – always wear frost proof
gloves and a face shield before attempting to
check for fuel cylinder overfill.
• In case of a fire, keep the fuel cylinder cold with
an extinguisher or water hose.
• Store fuel cylinders vertically in an outside
lockable, ventilated storage locker.
• Be aware of the symptoms of carbon monoxide
poisoning and take appropriate actions if
necessary.
• Always maintain engine and machine as
specified for superior performance, long life
and safety.
Reminders
Operational Safety
To Order Parts Call 1-888-702-5326 - https://monsterfloorequipmentparts.com