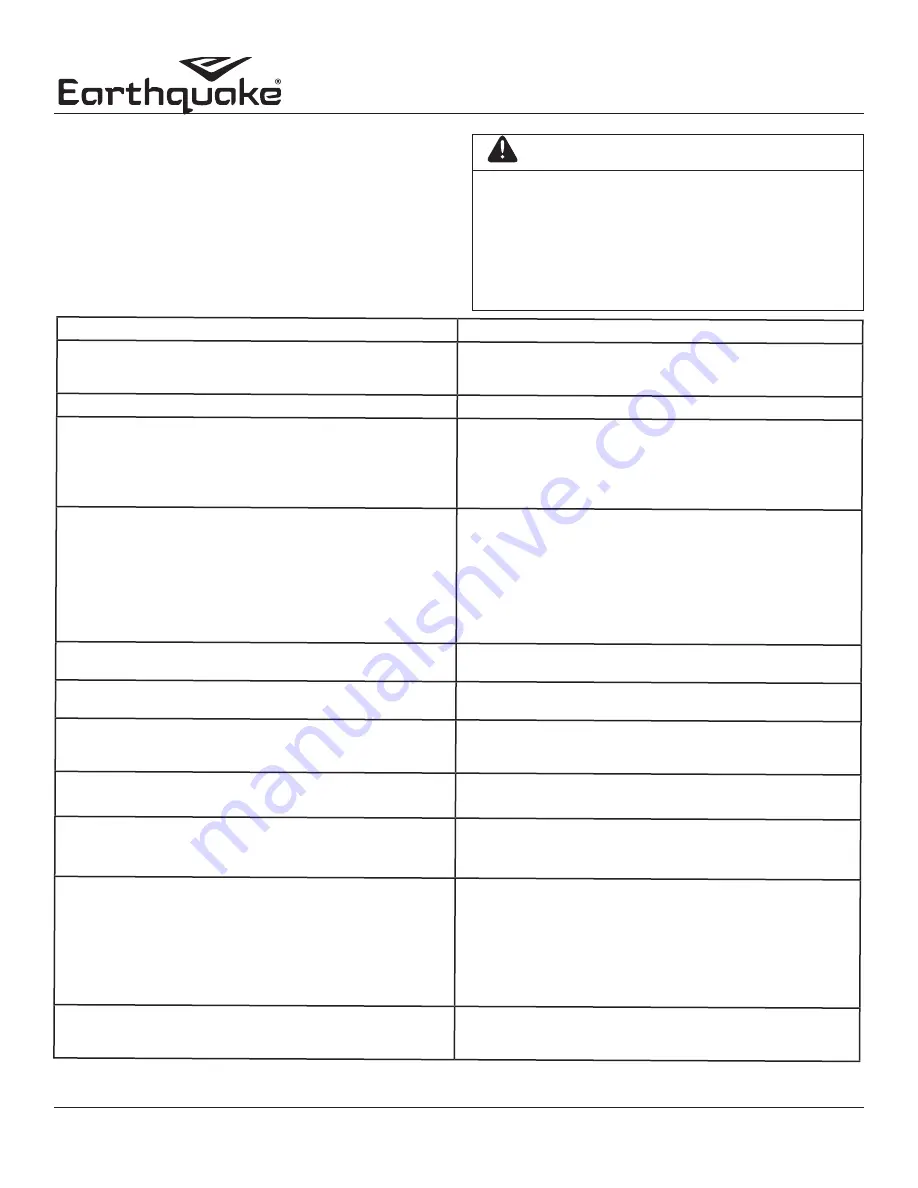
Operator’s Manual
CRT Rototiller
20
For additional information email
info@ardisam.com
or call 800-345-6007 M-F 8-5
TROUBLESHOOTING
Troubleshooting Guide
While normal care and routine maintenance will extend
the life of your rototiller, prolonged or constant use may
eventually require that service be performed to allow
it to continue operating properly. The troubleshooting
guide below lists the most common problems, causes and
remedies.
PROBLEM
REMEDY/ACTION
Engine will not start
Add gas to gas tank.
Connect spark plug wire to spark plug
Throttle must be positioned at choke for a cold start
Engine runs rough, floods during operation
Clean or replace air cleaner
Engine is hard to start
Drain old fuel and replace with fresh. Use gas stabilizer at end
of season
Make sure spark plug wire is securely attached to spark plug
Drive safety control levers must be released to neutral position
to start the engine
Engine misses or lacks power
Raise the tines for shallow tilling by lowering the depth
regulator lever
Remove and clean fuel tank
Clean or replace air cleaner
Improper carburetor adjustment, take to authorized engine
service center
Replace spark plug and adjust gap
Drain and refill gas tank and carburetor
Engine will not stop when throttle control is positioned at
stop
See engine manual to check and adjust throttle linkage
Tiller moves forward during starting
Drive safety control levers must be released to neutral position
to start the engine
Tiller is difficult to control when tilling (machine jumps or
lurches forward)
Lock wheels in tilling position
Raise tines for shallower tilling by lowering the depth regulator
lever
Tines turn, wheels do not turn
Lock wheels in tilling position
Internal transmission failure, see your dealer
Tines turn, wheels turn, tiller does not move
Raise the tines for shallower tilling by lowering the depth
regulator lever
Lift slightly on handlebars to allow wheels to gain traction
Belts squeal in neutral
Adjust forward belt guide:
- turn engine off and allow muffler to cool,
- disconnect spark plug wire and secure from spark plug,
- remove belt guard,
- pull down on drive safety control lever,
- manually bend forward belt guide so there is 1/16 inch or
less clearance between belt guide and belt,
- replace belt guard and spark plug wire.
Excessive heat build up in transmission/tine area during tilling Remove vegetation by following instructions in Clean Tine
Axle Shaft of Normal Care section. Check transmission fluid
and fill if needed
PRACTICE SAFETY AT ALL TIMES. ENGINE MUST
BE TURNED OFF AND ALLOWED TO COOL, AND
SPARK PLUG WIRE MUST BE DISCONNECTED AND
SECURED BEFORE ATTEMPTING ANY MAINTENANCE
OR REPAIR. FAILURE TO COMPLY WITH THIS SAFETY
REQUIREMENT CAN RESULT IN SERIOUS PERSONAL
INJURY TO YOU OR BYSTANDERS.
WARNING