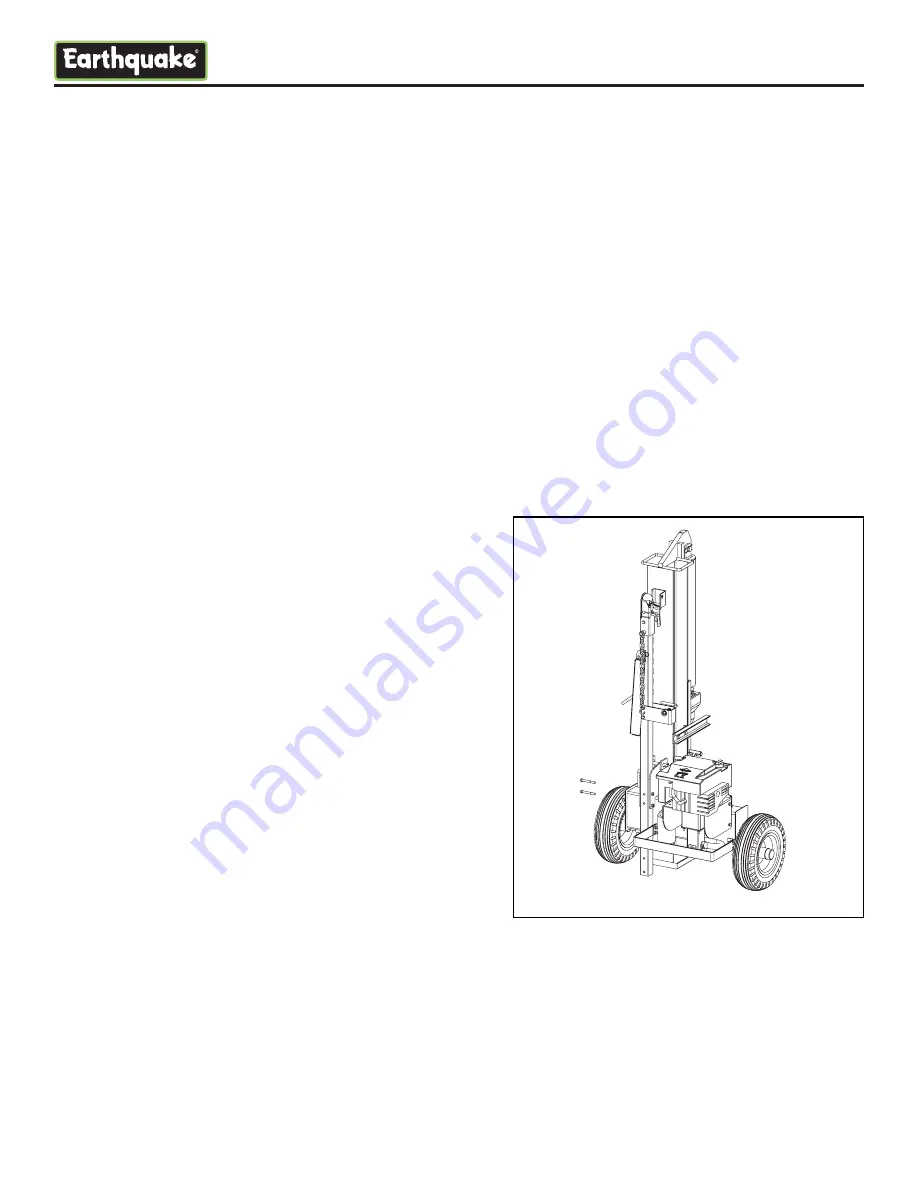
Page 12
LOG SPLITTER OPERATING INSTRUCTIONS
MAINTENANCE
1. Consult the operating and maintenance instructions of the Engine Operator’s Manual for engine care and
maintenance.
2. Always check the oil level of the hydraulic reservoir before operation. Operating the log splitter without an
adequate oil supply will cause severe damage to the hydraulic pump.
3. Change the oil filter after the first 25 hours of operation. Thereafter, change the oil filter every 100 hours or
seasonally, whichever comes first.
4. If the wedge becomes dull or nicked, it can be removed and sharpened. While the log splitter is in the
horizontal position, remove the 1/2” x 3-1/2” bolt (4362) that connects the wedge to the hydraulic cylinder.
Carefully rotate the hydraulic cylinder, take special care not to damage the control valve. The wedge can
now be removed and sharpened.
5. Refer to the Repair and Maintenance Safety section of this manual.
6. All replacement parts must meet manufacturer’s specifications.
7. Check air pressure of tires before each use. Maintain pressure between 20 psi and 30 psi.
8. Grease wheel bearings annually.
STORAGE
1. Rotate the beam to the vertical position after the log splitter
has been moved to its storage location. Ensure that the
locking pin for the vertical position has been fully engaged.
2. While a second person balances the beam vertically, unbolt
the tongue from the reservoir. Save the nuts and bolts.
Rotate the tongue 90 degrees and stand it on the end that
was previously bolted the reservoir. Re-install the two nuts
and bolts that were removed in Step 1.
Refer to Figure 9.
3. To return the unit to its functional state, follow the Steps in
reverse order.
Figure 9