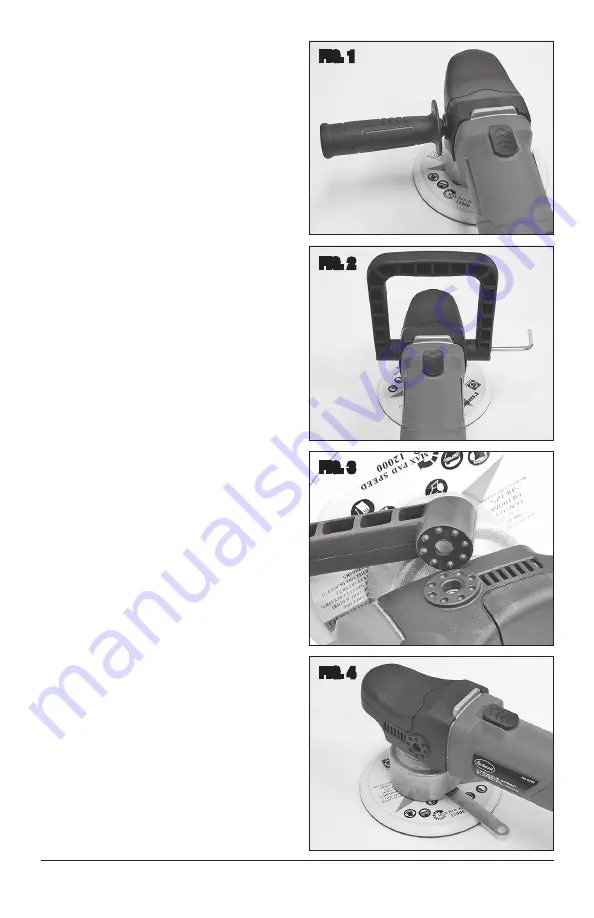
To order parts and supplies: 800.343.9353 >> eastwood.com
7
SET-UP
• Note that The Eastwood 6” Buffer/
Polisher is supplied with a choice of
2 handle mounting options:
- 1st Option; Side Handle:
Thread the
Side Handle into one of the threaded
holes at the side of the Buffer Head
(FIG 1)
. Hand Tighten securely.
NOTE:
Attach to the left side for right-
handed users and to the right side for
left-handed users .
- 2nd Option; “D” Handle:
Place
mounting holes over the threaded
holes at the side of the Buffer Head
and fasten with the supplied M8 Socket
Head Cap Screws
(FIG 2)
.
NOTE:
The Handle of the Buffer/Polisher
has an array of round, raised features
at the Mounting Flange area while the
Buffer Head has an array of correspond-
ing depressions
(FIG 3
). This allows for
positive indexing of the Handle when the
screws are tightened.
• Slide the Spindle Flat Wrench over the Hex
of the Spindle
(FIG 4)
.
• Thread the Backing Pad post into the Arbor
and hold the Arbor Flat Wrench until it is
securely tightened.
• Withdraw the Arbor Flat Wrench.
• Apply the appropriate work pad (Buffing
Pad, Sanding Disc etc.) for the job.
• Plug into a minimum 15-amp circuit.
If using an extension cord, it must be
AWG 14 or greater, no longer than 25’.
FIG. 1
FIG. 2
FIG. 3
FIG. 4