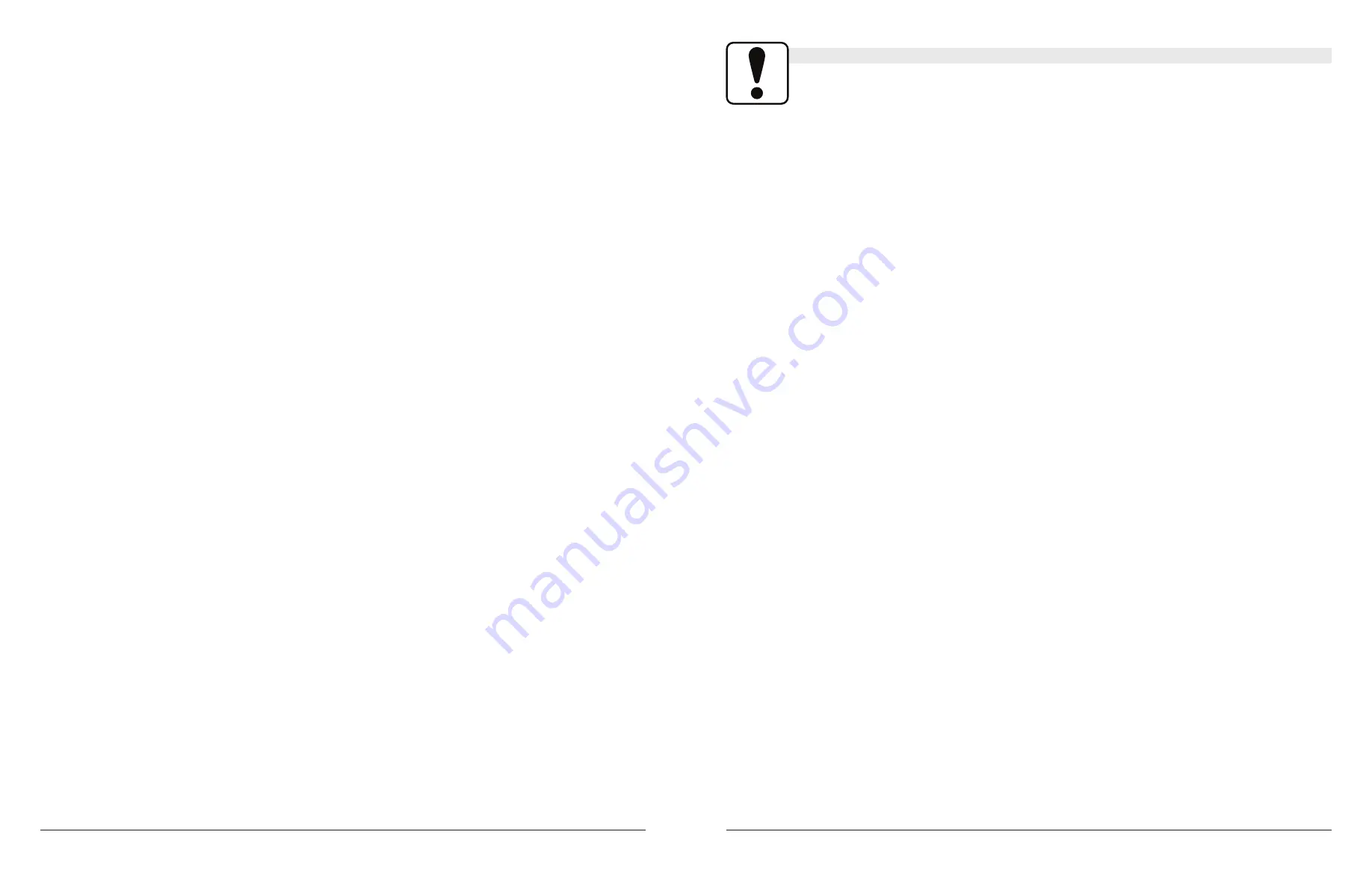
14
Eastwood Technical Assistance: 800.544.5118 >> techelp@eastwood.com
To order parts and supplies: 800.345.1178 >> eastwood.com
3
OPERATIONAL HAZARDS!
• Use clamps or other practical means to secure and support the work piece to a stable location. Holding the
work by hand or against your body may lead to a loss of control and result in severe injury.
•
NEVER
clamp the Safety Trigger (dead man valve) in the open position or attempt to defeat it’s purpose in any way.
Severe bodily injury and or property damage can quickly occur.
•
ALWAYS
check to make sure that the Safety Trigger is not open before connecting blaster to air supply.
Blaster may cause damage to property or person if connected to air while the safety trigger valve is open.
• Store the blaster out of the reach of children and untrained persons. High-pressure pneumatic equipment is
dangerous in the hands of untrained users.
• Never allow abrasive blaster to sit pressurized while unattended or not in use.
•
ALWAYS RELEASE THE AIR PRESSURE IN THE TANK BEFORE OPENING.
See “Releasing Pressure from the
Tank” section. Make sure pressure gauge reads “0” before opening the tank. Do not attempt any maintenance
on the abrasive blaster until the pressure gauge reads “0”, and it has been disconnected from air supply.
• Check for damage regularly. If any part of the blaster is damaged or, if in doubt, the part should be replaced. Only
qualified persons familiar with high-pressure pneumatic equipment should perform repairs. Consult Eastwood for
advice.
• Periodically check the abrasive media delivery components. Valves, hoses and nozzles that are exposed to the
abrasive media after it leaves the pressure tank are subjected to abrasive blasting action and will wear out more
quickly than other components.
•
ALWAYS
disconnect the air supply and release pressure from the tank before refilling media, storing, servicing,
or changing accessories. Such preventative safety measures reduce the risk of releasing pressure accidentally.
• Make sure all air supply equipment is rated to the appropriate capacity. For best results, set regulator and
operate at 80 to 90 psi. DO NOT exceed 125 psi.
• The safety valve is set to release at 125 psi. If the safety valve releases, stop all work immediately and release
pressure from the tank (see “Releasing Pressure from the Tank” section).
3.
The third most common cause of unsatisfactory Abrasive Blaster performance is insufficient CFM flow. CFM = Cubic Feet per
Minute. This is based on compressor output and is listed on all compressor data plates. The greater the CFM output of a
compressor, the better an Abrasive Blaster will perform. Also, a smaller Nozzle I.D. will require less CFM. Generally, a 2mm
Nozzle will require 10 CFM @ 90 psi while a 3.5mm Nozzle will require 20 CFM.
In addition, excessive hose length and an increased number of fittings will reduce available CFM to the Abrasive Blaster.
A larger hose I.D. and shorter length will serve to increase CFM delivery to the Abrasive Blaster.
Generally, if a compressor runs constantly while blasting, it is an indication that it is undersized and a larger capacity unit may be
required. Continuing to run a compressor at that rate can cause overheating and permanent damage.
WARRANTY
This product has a one year warranty covering any manufacturing defects. Despite our strict quality control standards implemented
during our manufacturing process, sometimes a product gets shipped that does not meet our specifications. If you have a product
that does not work correctly within 30 days of your purchase, it can be returned to The Eastwood Company for credit or replacement.
Before returning any product, you must contact the Eastwood Company at 800-345-1178 to acquire a Return Authorization Number.
When sending your product you must include:
1.
A copy of the dated receipt showing the original purchase,
2.
Your full name, street address and telephone number.
Please ship to:
The Eastwood Company
263 Shoemaker Rd.
Pottstown, PA 19464
ATTN: Warranty Return
We will examine the product. If the problem is due to a manufacturing defect, we will repair or replace the product at no charge and
return to you postage or UPS paid. If the problem is due to misuse, abuse, user modification or it is out of warranty, we will contact
you with a repair estimate and ask for a credit card number for payment. After the product has been repaired, it will be returned via
postage or UPS paid.