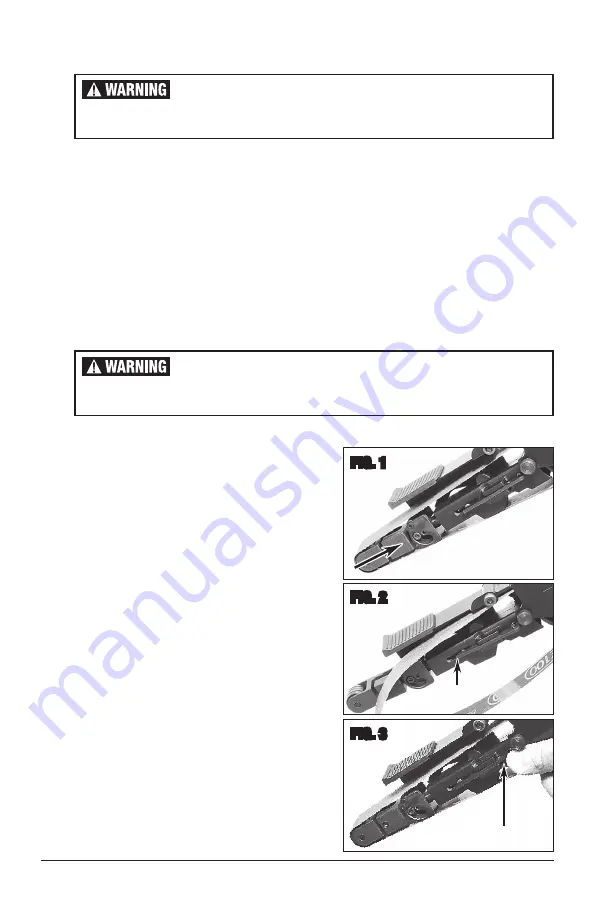
To order parts and supplies: 800.345.1178 >> eastwood.com
5
OPERATION
• Depress Throttle Paddle inward with fingers to operate tool.
• Keep the broad work surface of the Abrasive Belt parallel to the work surface whenever
possible to minimize uneven wear and maximize usable life.
• Always maintain a firm grip while operating tool, do not force but allow the rotational speed
of the Abrasive Belt to do the work.
• Be sure that the workpiece is clamped down or held securely to minimize the danger of
injury while operating tool.
INJURY HAZARD!
Disconnect air supply from the tool to prevent accidental starting and potential
injury while installing or removing Abrasive Belts.
ABRASIVE BELT REPLACEMENT
The Abrasive Belts are quickly and easily changed. No tools are required.
The following steps describe how to do this:
• The end of the Abrasive Belt Arm is spring loaded
to keep the proper tension on the Abrasive Belts.
While holding the tool firmly, push inward on the
end of the Abrasive Belt Arm while depressing the
Thumb-Lever Latch
(FIG 1)
.
NOTE:
The Guide Pin will move inward until it lo-
cates under the Latch portion of the Thumb-Lever
Latch holding it in the retracted position while the
Abrasive Belt is changed
(FIG 2)
.
• Pull the worn Abrasive Belt free of the Drive Drum
and discard.
• Slide the replacement Abrasive Belt over the Drive
Drum and Idle Roller at the end of the Abrasive
Belt Arm
(FIG 2
).
NOTE:
Be sure the Abrasive Belt is slid fully over
the Guide Bar located on the upper surface of the
Abrasive Belt Arm.
• Depress the Thumb-Lever Latch to release the
Guide Pin restoring full spring pressure
(FIG 3)
.
FIG. 1
FIG. 2
INJURY HAZARD!
Disconnect air supply from the tool to prevent accidental starting and potential
injury while installing or removing Abrasive Belts.
FIG. 3
✓
Push in to latch
Latched
✓
Push to unlatch
✓