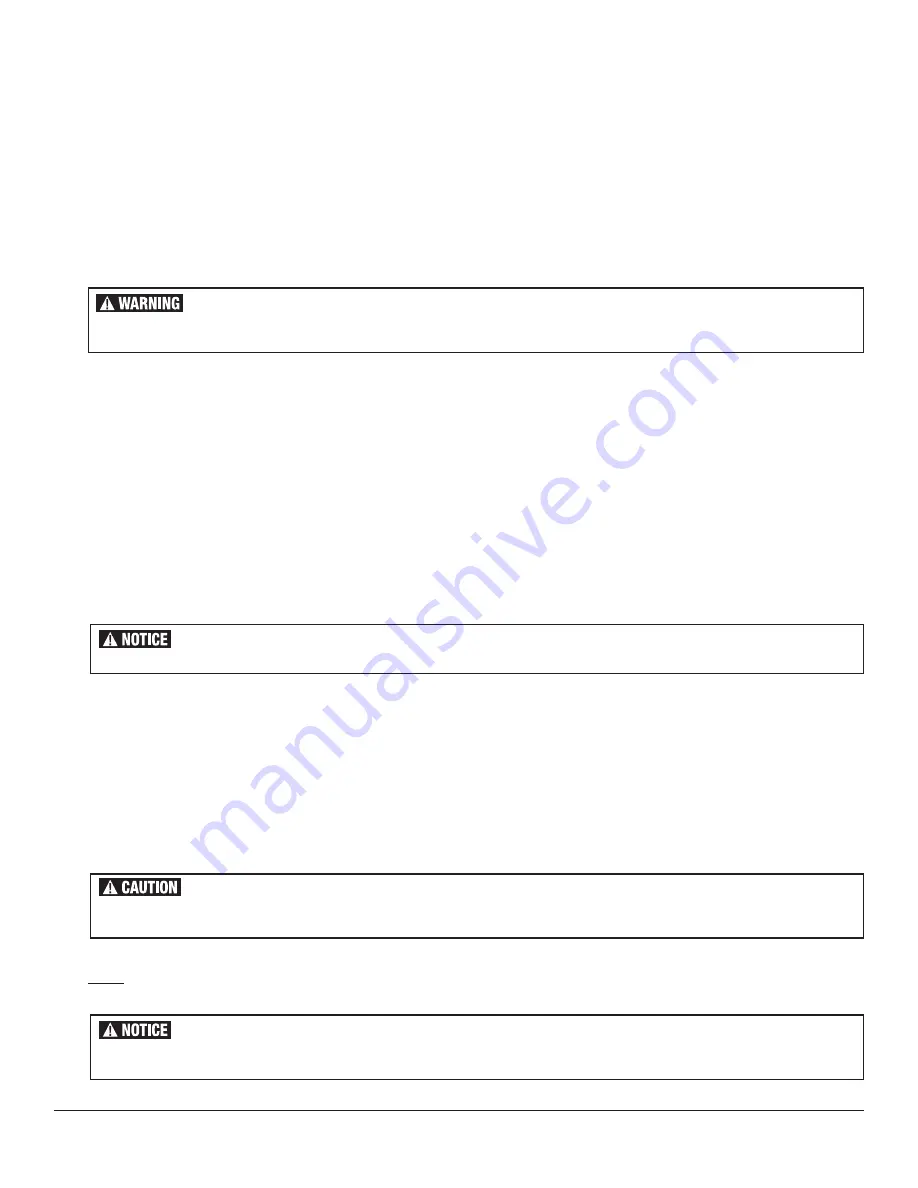
To order parts and supplies: 800.343.9353 >> eastwood.com
9
AIR TANK CONDENSATION DRAIN
In normal use, particularly in humid environments, moisture will condense and collect in the tank. It must be drained daily to prevent internal tank corrosion
and ultimate failure.
Tank moisture draining procedure:
• Move the Power Switch to the “OFF” position.
• Release pressure from the Tank until the Tank Pressure Gauge indicates 0 PSI.
• Place a suitable container under the Drain Valve.
• Slowly
open the Drain Valve located on the underside of the Tank
(FIG 12)
.
• Close Drain Valve securely when finished.
Condensate is a polluting material and should be disposed of in compliance with local regulations.
If drain valve becomes clogged, release all air pressure, remove and clean valve, then reinstall.
Opening the Drain Valve before releasing pressure from the Tank will cause contaminated water to be blown out at high velocity.
Release pressure from the Tank until Tank Pressure Gauge indicates 0 PSI. Always wear appropriate eye protection.
OIL TANK CONDENSATION DRAIN
Operation
• The Moisture Drain System is designed to provide a means to easily drain excess moisture (water) which builds up in the oil tank. Check for moisture
monthly using the following procedure.
NOTE:
For heavy use in high humidity conditions, it is recommended to drain the oil tank condensation weekly.
• Move Power Switch to the “OFF” position.
• Release pressure from Tank until Tank Pressure Gauge indicates 0 PSI.
• Disconnect Compressor from power supply.
• Allow the unit to sit at least 8 hours without operating. This allows the water sufficient time to settle to the bottom of the oil tank for easy removal.
• Verify the Oil Drain Hose is connected to the Moisture Drain Bottle.
• Slowly open the Oil Drain Valve and allow any clear liquid (water) to drain.
• As soon as you observe the honey-colored oil coming out, close the drain valve.
• Verify the oil level is still acceptable. Remove the Oil Fill Plug/Dipstick from the upper front area of the Oil Reservoir
(FIG 2)
.
• Check oil level by observing the level on the Dipstick. The oil level is acceptable when it is
BETWEEN
the top mark and bottom mark
(FIG 3)
.
• If necessary, carefully add or remove oil until the level is
BETWEEN
the marks.
• Inspect the Oil Fill Plug/Dipstick Seal and replace the Oil Fill Plug/Dipstick and tighten securely.
• Check for full closure of the Drain Valve located on the Oil Reservoir
(FIG 4)
.
• The compressor may be started and operated as normal.
Maintenance
• Remove and drain the Bottle when the moisture level approaches 1/2 full.
• Wash Bottle completely with soap and hot water. Dry thoroughly.
Fluids drained from the Moisture Drain Bottle are hazardous materials and should be disposed of in compliance with local regulations.
INJURY HAZARD!
Before performing any service, turn Power Switch to the “OFF” position (FIG 1). Shut off breaker or disconnect power supply. Release
pressure from Tank until Gauge indicates 0 PSI.