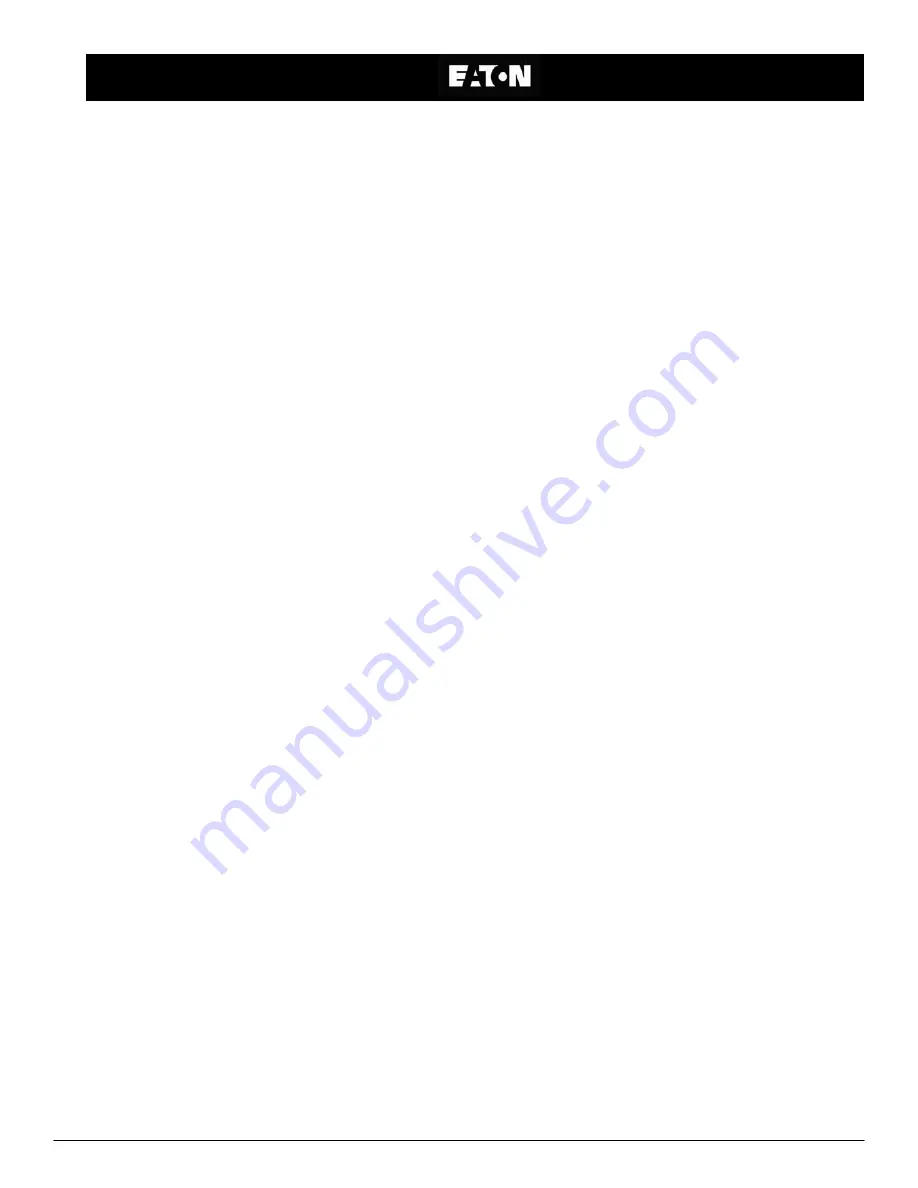
9
Trouble Shooting
High Differential Pressure due to high solids
loading in process fluid:
Increase length of backwash cycle or backwash
continuously
.
Backwash Arm not rotating, Motor overloads
tripped:
Obstruction between straining element and back-
wash arm.
Misalignment of backwash arm.
Bearing failure.
High Differential Pressure due to piping:
Shorten backwash piping by eliminating elbows,
vertical pipe runs and restrictions due to valves,
fittings, etc. By removing pipe friction loses, system
pressure losses are reduced.
Trouble Shooting, Continued
Backwash Arm not rotating, Motor and/or reducer
failure:
Incorrect voltage applied to strainer motor.
Overload heaters in motor starter improperly sized.
Lubricant level in reducer too low, reducer vent
plugged, or no lubricant.
Control Problems:
Blown fuses.
Incorrect voltage applied to control panel and/or
valves, switches, etc.
Incorrect wiring between control panel and valves,
switches, alarms, etc.
Differential pressure switch improperly adjusted.
Insufficient air pressure applied to pneumatically oper-
ated backwash valves