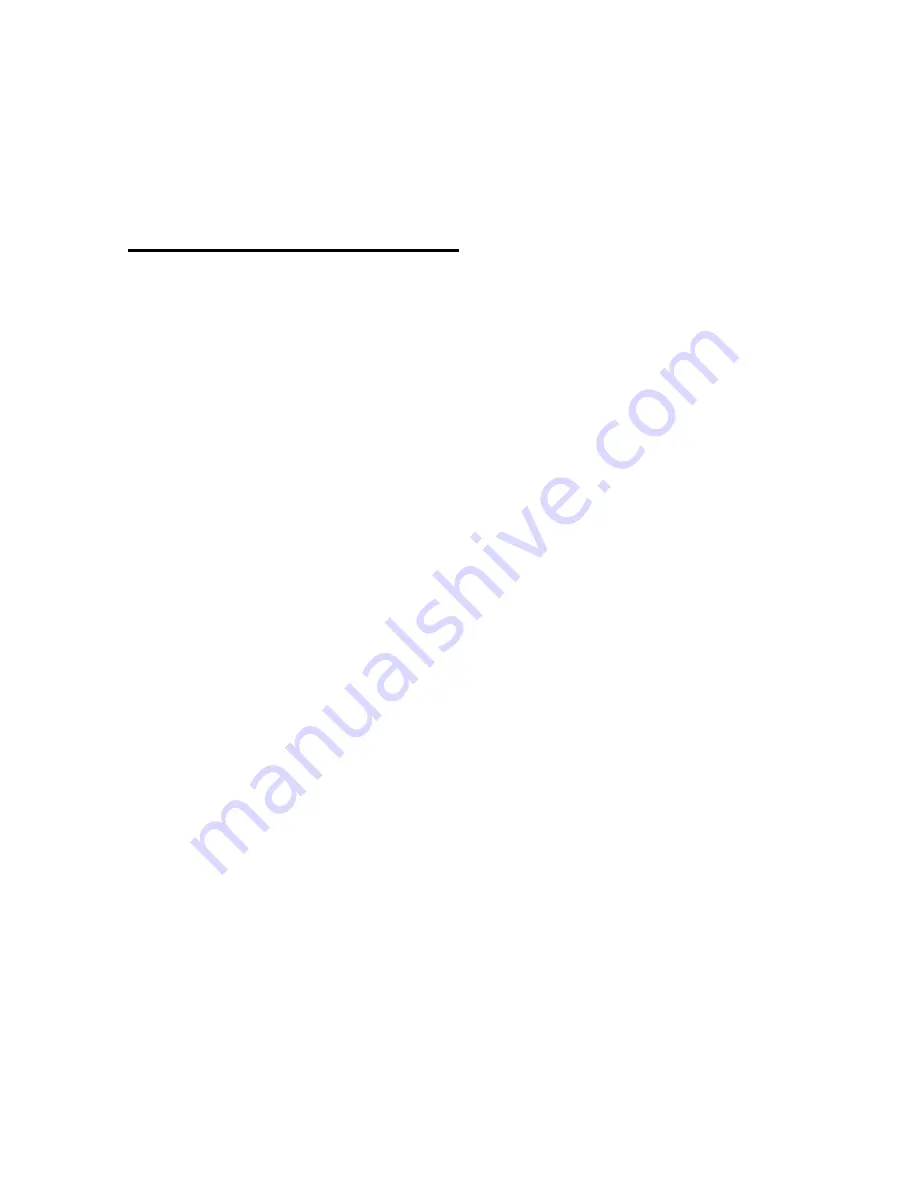
Section VIII
Proof Testing Procedures
EATON
Aerospace Group
TF100-63B October 2018
Section VIII
Proof Testing Procedures
1. Equipment
The following equipment is recommended for proof
test of hose assemblies covered by this manual.
Eaton Part No.
Name
F2197
Hydraulic Proof Test Stand
For information covering pneumatic proof test equipment,
contact Eaton.
2.
Recommended Hydrostatic and Pneumatic Proof Test
Pressures
A.
The recommended hydrostatic proof test
pressure is 6,000 psi (413.68 bar) for all sizes.
B.
The recommended pneumatic proof test
pressure is 3,000 psi (206.84 bar) for all sizes.
3.
Hydraulic Proof Test
Proof test medium shall be hydraulic oil, Specification
MIL-H-5606 or water. All hose assemblies shall be proof
tested after assembly for a period of not less than 30
seconds and not more than 5 minutes.
Note
: Proof test stands and special adapters are avail-
able from Eaton to facilitate testing large quantities of
hose assemblies. See Assembly Equipment, Special
Tools, Fixtures, and Services, Section XV.
4.
Pneumatic test
Pressure test air-under-water for not less than 30 sec-
onds nor more than 5 minutes and observe for bubbles
indicating leakage.
Warning:
Pneumatic leakage testing shall only be
performed under a protective cover for the safety of
the operator.
Caution:
Never proof test sleeved hose lines under
water.
5.
Disposition If Fitting Leakage Is Noted
A.
Remove hose assembly and check for proper
gap (Section VI – Assembly Procedure.)
B.
If proper gap was obtained, disassemble
hose assembly according to Section III –
Disassembly. Inspect fittings as described in
Section XI.
6.
After Proof Test Operation
A.
Cleaning — Clean and drain assembly after
proof test. See Cleaning, Section IV.
Note
: Application of an identifying mark such
as a paint dot, etc., indicating satisfactory proof
test is recommended.
B.
Capping — Cap or plug all hose assemblies to
ensure cleanliness.