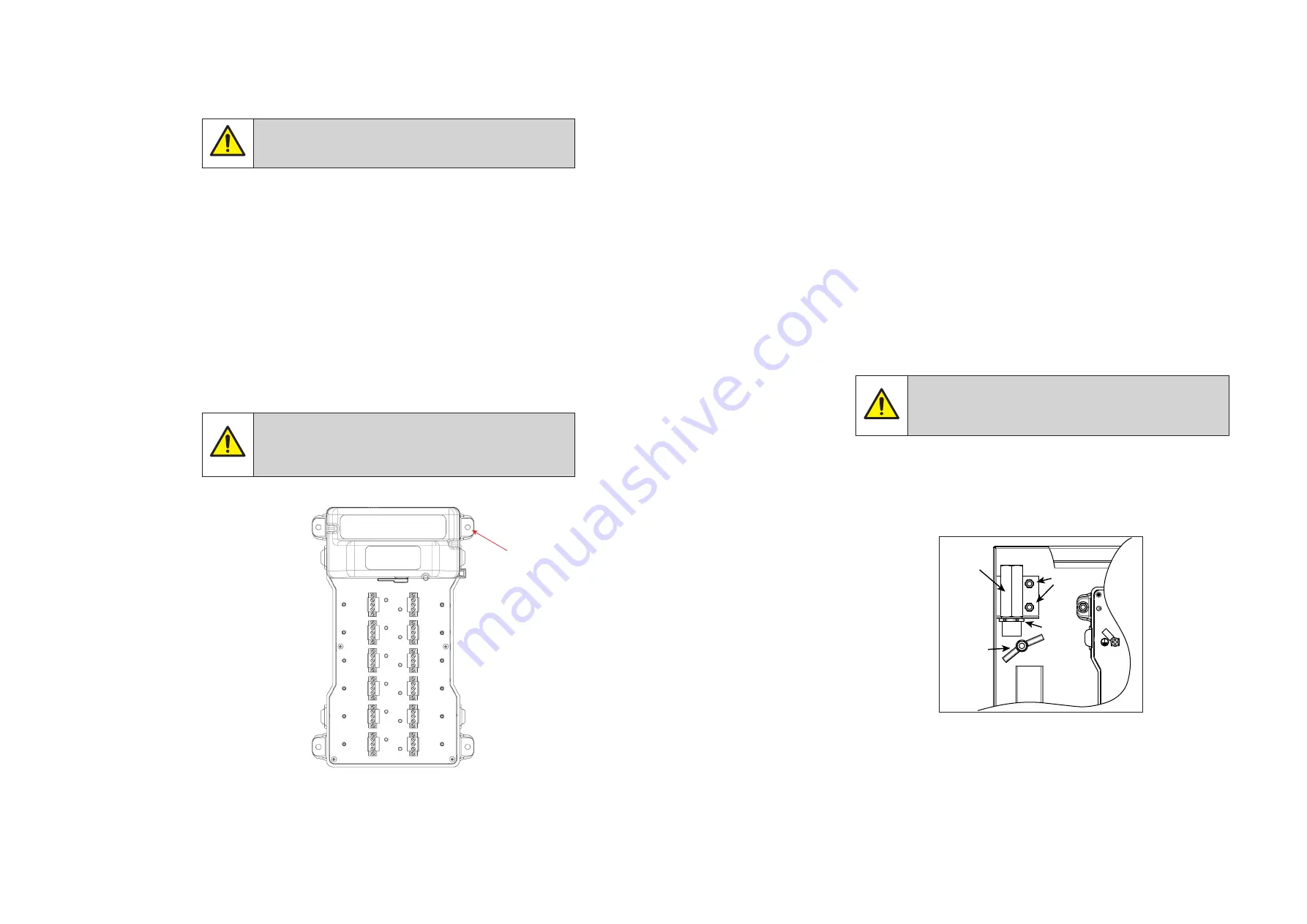
20
21
INM MTL9373-FB3 Rev 1
INM MTL9373-FB3 Rev 1
6.3 Trunk connections
Note the warning given on the covers protecting all of the trunk wiring areas.
WARNING!
Do not remove or replace while circuit is live if a flammable or
combustible atmosphere is present
Work on the trunk wiring, protected by additional covers, requires the trunk power to
the enclosure to be isolated, or a gas clearance certificate obtained.
Once the conditions are known to be safe, the necessary plastic cover(s) over the
Trunk wiring may be removed. Refer to Sections 5.4 or 5.5 for additional information
about the relevant trunk wiring connections.
When any changes or checks have been carried out, ensure there are no loose
implements left before replacing protective cover for the trunk wiring. Replace the
transparent protective cover over the trunk wiring and ensure that there is positive
engagement of the retaining clip.
6.4 Removal and replacement of a module
If it is found necessary to swap-out a complete barrier module in the enclosure,
proceed as below.
WARNING!
The following procedure requires the power to the barrier/enclosure to
be isolated. No work is permitted unless the power has been isolated
or the environment is known to be non-hazardous.
Figure 6.1
– Removing a barrier module
Use the following procedure and reference to Section 5.3.1 may help.
a) Unclip and remove the Trunk Terminal cover
b) Loosen the two screws securing the pluggable, TRUNK-IN wiring connector
and unplug it. Do the same for a TRUNK-OUT connector if there is a cable
connected. Arrange these safely to the side of the barrier.
c) In turn, loosen the two screws securing each pluggable, spur-wiring connector
and unplug the connectors. Arrange the connector wiring so that you have
access to the barrier fixings.
d) The barrier is secured to the backplane of the enclosure by four M5 flange
nuts. (See Figure 6.1 for their locations.) Loosen these in turn and remove
them to free the barrier and remove it from the enclosure.
e) Replacement is the reverse of the removal process – tightening barrier fixing
nuts to a recommended torque of 2.5 Nm and connector screws to
0.5 - 0.6 Nm.
Follow site practice on the reuse of any locking washers; replacement may
be advisable.
6.5 Replacement of a TP-32 Surge Suppressor
WARNING!
The following procedure requires the power to the barrier/enclosure to be
isolated. No work is permitted unless the power has been isolated or the
environment is known to be non-hazardous.
Replacement of this item will depend upon the enclosure type for wiring details.
Refer to sections 5.4 or 5.5 for information on the wiring of the enclosure type.
The TP-32 has a threaded section on its body with a retaining nut to enable it
to be fitted to a mounting bracket on the inside of the enclosure. Removal and
replacement will be simplified by removing the item complete with its mounting
bracket.
Figure 6.2
– TP-32 mounting details
Barrier
mounting
locations
x 4
TP-32
M6 (x2)
Grounding
stud
Retaining
nut