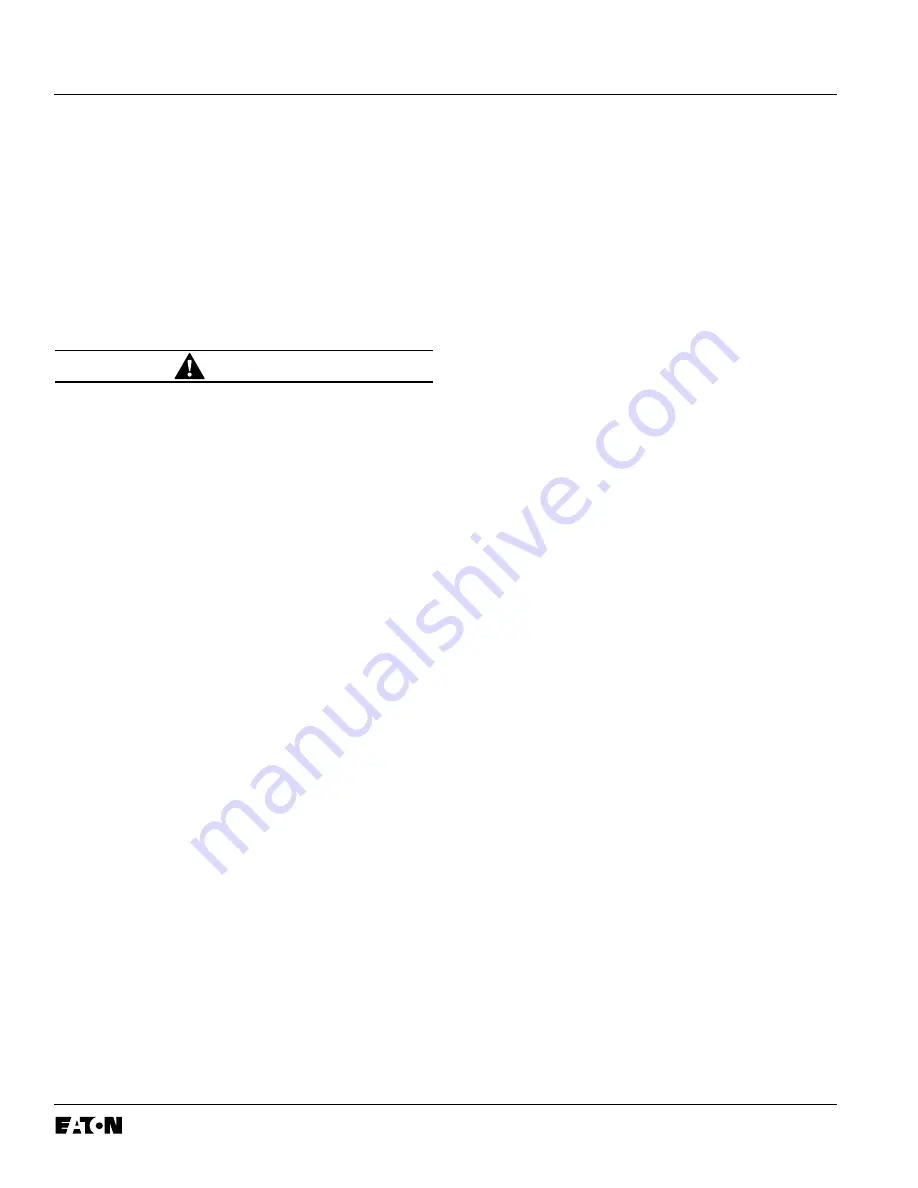
Effective 10/00
IL 33-K2C-3
Page 6
STEP 1:
GENERAL BREAKER PREPARATION
Before attempting to remove the Breaker from the
Cell or perform any Retrofit operation, be sure to
read and understand the Safety Precautions
section of this manual. In addition, be sure to read
and understand the
Instructions for the Application
of Digitrip RMS Retrofit Kits on Power Circuit
Breakers
(Retrofit Application Data – Publication
AD-33-855-2), supplied with the Digitrip Retrofit
Kit.
WARNING
DO NOT ATTEMPT TO INSTALL OR PERFORM
MAINTENANCE ON EQUIPMENT WHILE IT IS
ENERGIZED. SEVERE PERSONAL INJURY OR
DEATH CAN RESULT FROM CONTACT WITH
ENERGIZED EQUIPMENT. VERIFY THAT NO
VOLTAGE IS PRESENT BEFORE PROCEEDING.
A. Trip the Breaker and remove it from the Cell.
Move the Breaker to a clean, well-lit work
bench.
NOTE:
It is the responsibility of the Retrofitter to
insure that the Breaker and all original
components are in good condition. Visu-
ally inspect all Breaker components for
signs of damage or wear. If any signs of
damage or wear are detected for compo-
nents not included in the Retrofit Kit,
secure the necessary replacement parts
before beginning the Retrofit Process.
The force necessary to trip the Breaker
should not exceed three (3) lbs.
NOTE:
It is the responsibility of the Retrofitter to
insure that the proper, manufacturer’s
recommended crimping tools and termi-
nals are used for each type of connector.
It is also the responsibility of the
Retrofitter to insure that all wire
preparations, connections, strippings,
terminations, and wiring techniques are
performed according to the latest IEEE,
NEC, and / or NEMA industry standards,
specifications, codes, and guidelines.
To begin the Retrofit Process, refer to the compo-
nents list at the end of this manual. Lay out the
components and hardware according to the steps
outlined. The parts bags are labeled with the
corresponding step number. The components and
hardware will be used to complete each step in the
Retrofit Process.
www
. ElectricalPartManuals
. com