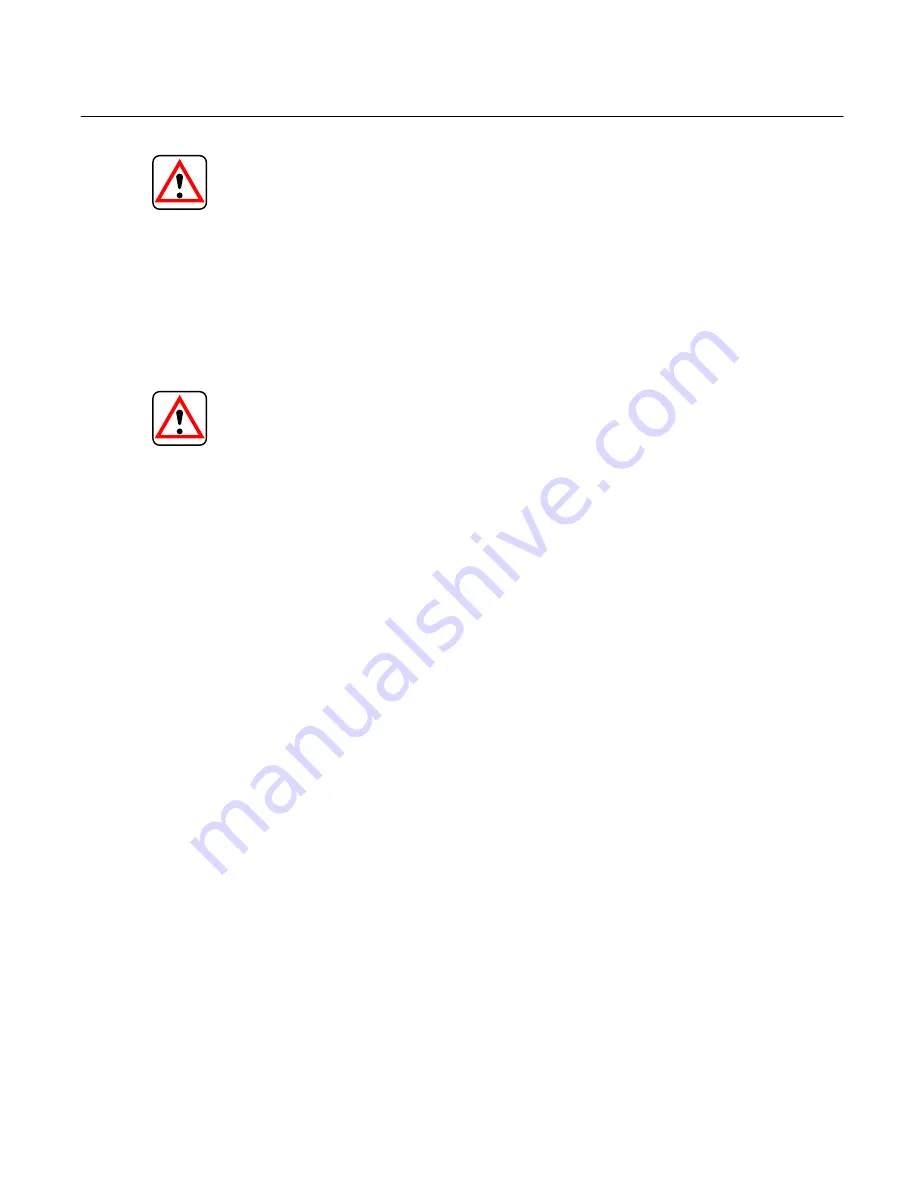
7
Section VI – Overhaul
A. General
CAUTION
Before breaking a circuit connection, make certain
that power is off and system pressure has been
released. Lower all vertical cylinders, discharge
accumulators, and block any load whose movement
could generate pressure.
Drain oil from the hydraulic system. Use new, clean, filtered
oil when restoring the unit to service. Clean the outside of
the unit thoroughly to prevent entry of dirt into the system.
After removing the valve and before disassembly, cap or
plug all ports and disconnected hydraulic lines.
CAUTION
Absolute cleanliness is essential when working on a
hydraulic system. Always work in a clean area. The
presence of dirt and foreign materials in the system
can result in serious damage or inadequate
operation.
B. Special Tools
The following special tools are required:
1. Test stand mounting plate model FGTM – 02 – 10
subplate and one BKFCGT – 02 – 644 bolt kit.
2. Power supply rated at: Input 115 AC 50/60 Hz, Output
0 – 300 DC mA. Vickers EMCS – P – 30 power supply part
number 631995.
3. Millimeter rated at 0 – 500 mA.
4. Test stand capable of providing the required hydraulic
flow. See figure 6 located in Section VII, Test Procedure.
5. Pencil type solder iron and rosin core solder.
6. Volt – Ohm meter (VOM).
7. 5 inch “C” clamp.
C. Improvised Tools
No improvised tools are required for overhaul.
D. Disassembly
Periodic maintenance of the valve will generally not require
disassembly to the extent described here. However, the
sequence can also be used as a guide for partial
disassembly. In general, disassembly is accomplished in the
item number sequence shown in figure 3. Special
procedures are included in the following steps:
NOTE
Discard and replace all “O” rings removed during
disassembly.
1. Prepare a clean lint free surface on which to lay inter-
nal parts of the valve.
2. Remove and discard “O” rings (1) and (2).
3. Remove four screws (3) from the electrical connector
(4) and allow the connector to hang down on its wires.
4. Symbolize each wire with a piece of tape to allow
reassembly to the same pin of the connector. Unsolder the
four wires from connector (4). Remove connector and gasket
(5).
NOTE
Hold the valve over a container during the following
step. The cover is full of system fluid that can leak
out during cover removal.
5. Remove four screws (6) and cover (7). This exposes
torque motor assembly (10). Use a 0.05 inch hex key to
thread metering spool adjustment screw from the torque mo-
tor armature nut.
6. Remove four screws (8) and washers (9) from torque
motor assembly (10) and remove torque motor from valve
body (30). Set the torque motor on the clean prepared sur-
face. Remove metering spool (12) from body (30). Be careful
not to stress or bend the wire. Lift spacer (11) and gasket
(13) from valve. Discard gasket.
NOTE
Parts (14) and (15) are used only on
FCGT-02-A-***-11 models. Do not remove from
body of valve at this time.
7. Apply pressure to center of retainer (17) with a “C” clamp
and remove snap ring (16) with a sharp screwdriver.
8. Remove parts (17) through (20) from valve body (30).
9. Apply pressure to center of retainer (22) and remove
snap ring (21) with a sharp screwdriver.
10. Remove retainer (22) then separate “O” ring (23) from
retainer. Discard “O” ring.
11. Remove parts (24) through (26). DO NOT remove seat
(27) at this time.
E. Inspection, Repair & Replacement
NOTE
All parts must be thoroughly cleaned and kept clean
during inspection and assembly. The close toler-
ance of the parts makes this requirement very
important. Clean all removed parts, using a com-
mercial solvent that is compatible with the system
fluid. Compressed air may be used in cleaning, but
it must be filtered to remove water and contamina-
tion. Clean compressed air is particularly useful in
cleaning the spool and body passages. Replace all
parts that do not meet the following specifications.
1. Inspect all components for excessive wear, erosion
and/or seizure.
2. Inspect torque motor (10) for contaminations (Ferrous
wear particles binding the armature). Inspect torque motor
coils for continuity (use the volt – ohm meter). Replace the
torque motor if contaminated, or coils are open. DO NOT
attempt repair of the torque motor.