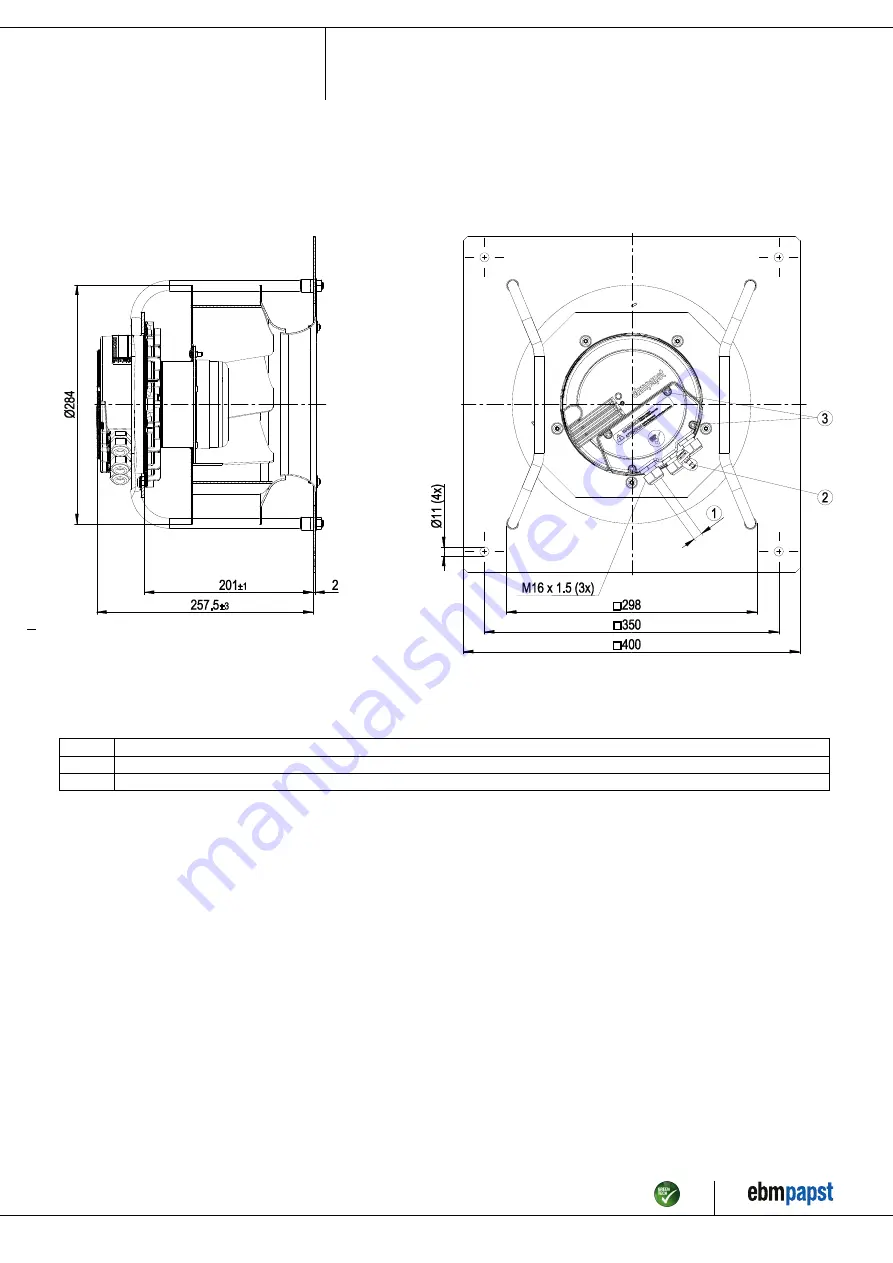
Operating instructions
K3G250-AV29-B2
Translation of the original operating instructions
3. TECHNICAL DATA
3.1 Product drawing
All dimensions in mm.
1
Cable diameter min. 4 mm, max. 10 mm; tightening torque 2.5±0.4 Nm
2
Inlet ring with pressure tap (k-factor: 70)
3
Tightening torque 3.5 ± 0.5 Nm
Item no. 50679-5-9970 · ENU · Change 213957 · Approved 2020-07-14 · Page 4 / 13
ebm-papst Mulfingen GmbH & Co. KG · Bachmühle 2 · D-74673 Mulfingen · Phone +49 (0) 7938 81-0 · Fax +49 (0) 7938 81-110 · info1@de.ebmpapst.com · www.ebmpapst.com