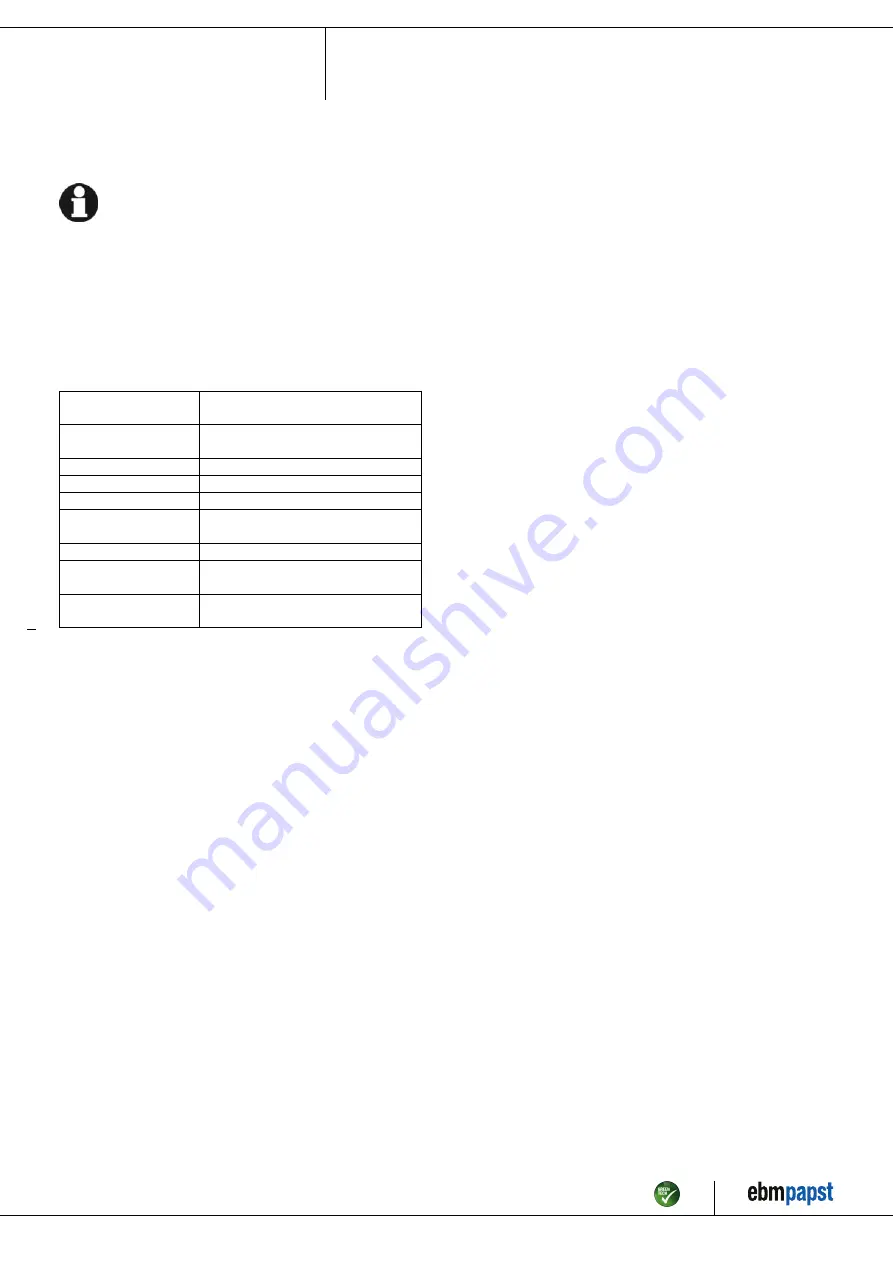
Operating instructions
K3G450-AQ24-01
Translation of the original operating instructions
4.3.3 Cable routing
No water may penetrate along the cable in the direction of the cable gland.
NOTE
Damage caused by moisture penetration.
Moisture can penetrate into the terminal box if water is
constantly present at the cable glands.
→ To prevent the constant accumulation of water at the cable
glands, the cable should be routed in a U-shaped loop
(siphon) wherever possible.
→ If this is not possible, a drip edge can be produced by
fitting a cable tie directly in front of the cable gland for example.
4.4 Factory settings
Factory settings with which the device is pre-set by ebm-papst.
Control mode
parameter set 1
PWM controlling
Control mode
parameter set 2
PWM controlling
Fan / device adress
1
Max. PWM / %
100
Min. PWM / %
5,1
Save set value to
EEPROM
Yes
Set value control
Analogue (linear)
Control function
parameter set 1
Positive (heating)
Control function
parameter set 2
Positive (heating)
Item no. 50638-5-9970 · ENG · Revision 209539 · Release 2021-02-12 · Page 9 / 15
ebm-papst Mulfingen GmbH & Co. KG · Bachmühle 2 · D-74673 Mulfingen · Phone +49 (0) 7938 81-0 · Fax +49 (0) 7938 81-110 · info1@de.ebmpapst.com · www.ebmpapst.com