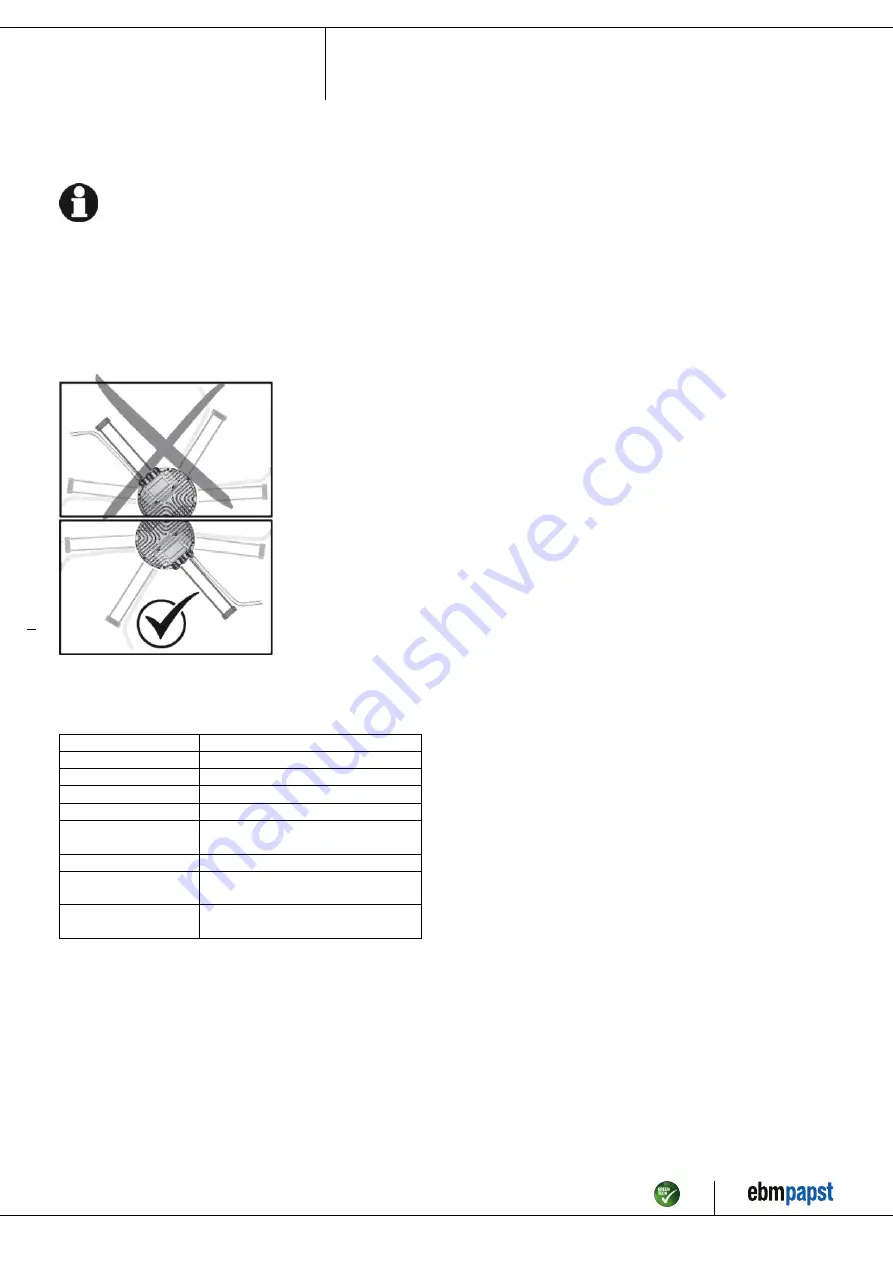
Operating instructions
K3G450-AZ30-35
Translation of the original operating instructions
4.3.3 Cable routing
Water must be prevented from reaching the cable gland along the cable.
NOTE
Damage caused by moisture penetration.
Moisture can penetrate into the terminal box if water is
constantly present at the cable glands.
→ To prevent the constant accumulation of water at the cable
glands, the cable should be routed in a U-shaped loop
wherever possible.
→ If this is not possible, a drip edge can be produced by
fitting a cable tie directly in front of the cable gland for example.
When routing the cable, make sure that the cable glands are located at
the bottom. The cables must always be routed downward.
Fig. 4: Cable routing for fans installed upright.
4.4 Factory settings
Factory settings made for the device by ebm-papst.
Mode parameter set 1
PWM control
Mode parameter set 2
PWM control
Fan/device address
01
Max. PWM / %
100
Min. PWM / %
5
Save set value to
EEPROM
Yes
Set value requirement
Analog (linear)
Direction of action
parameter set 1
Positive (heating)
Direction of action
parameter set 2
Positive (heating)
Item no. 50747-5-9970 · ENU · Change 209539 · Approved 2021-02-12 · Page 9 / 15
ebm-papst Mulfingen GmbH & Co. KG · Bachmühle 2 · D-74673 Mulfingen · Phone +49 (0) 7938 81-0 · Fax +49 (0) 7938 81-110 · info1@de.ebmpapst.com · www.ebmpapst.com