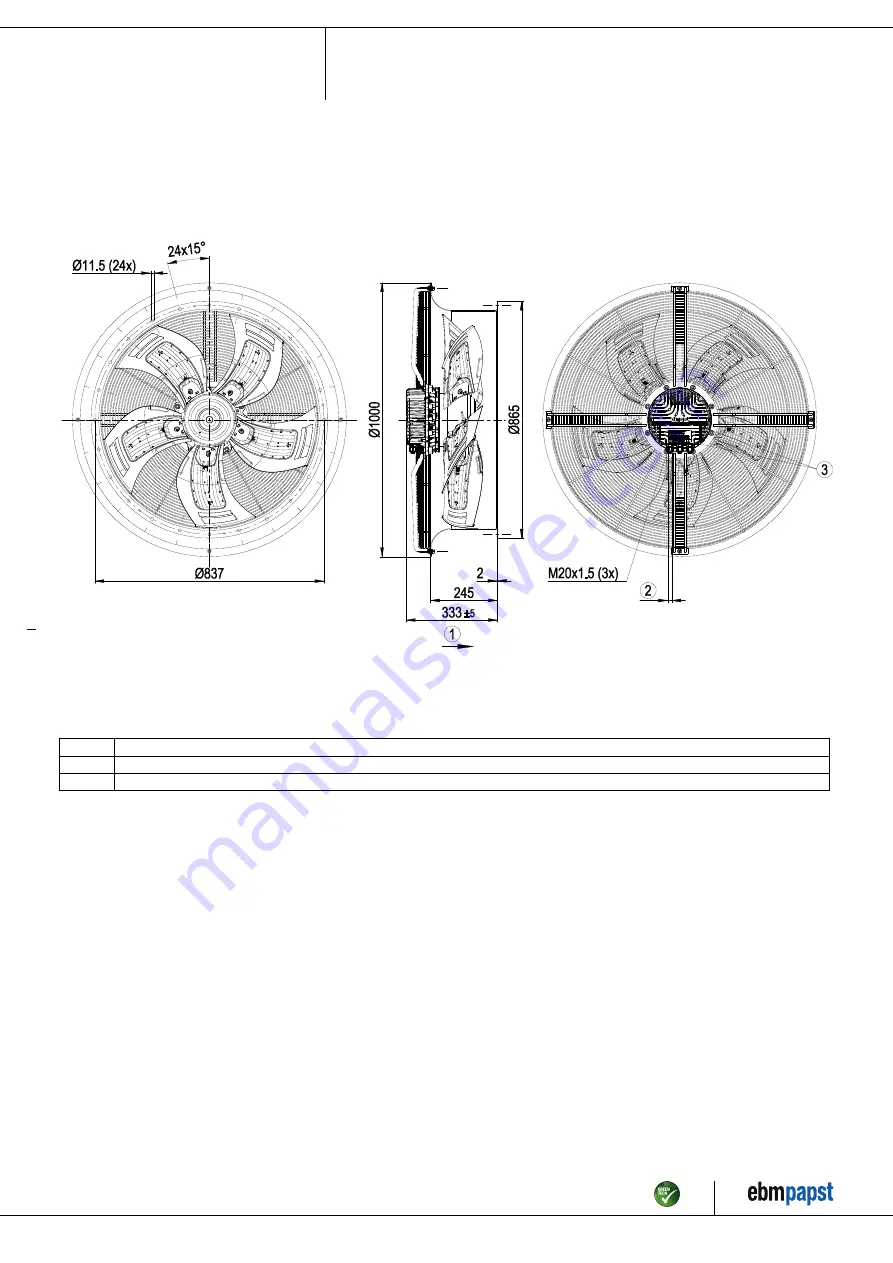
Operating instructions
W3G800-CU25-80
Translation of the original operating instructions
3. TECHNICAL DATA
3.1 Product drawing
All dimensions in mm.
1
Direction of air flow "A"
2
Cable diameter min. 5 mm, max. 13 mm, tightening torque 4 ± 0.6 Nm
3
Tightening torque 3.5 ± 0.5 Nm
Item no. 55047-5-9970 · ENU · Change 212910 · Approved 2020-11-18 · Page 4 / 14
ebm-papst Mulfingen GmbH & Co. KG · Bachmühle 2 · D-74673 Mulfingen · Phone +49 (0) 7938 81-0 · Fax +49 (0) 7938 81-110 · info1@de.ebmpapst.com · www.ebmpapst.com