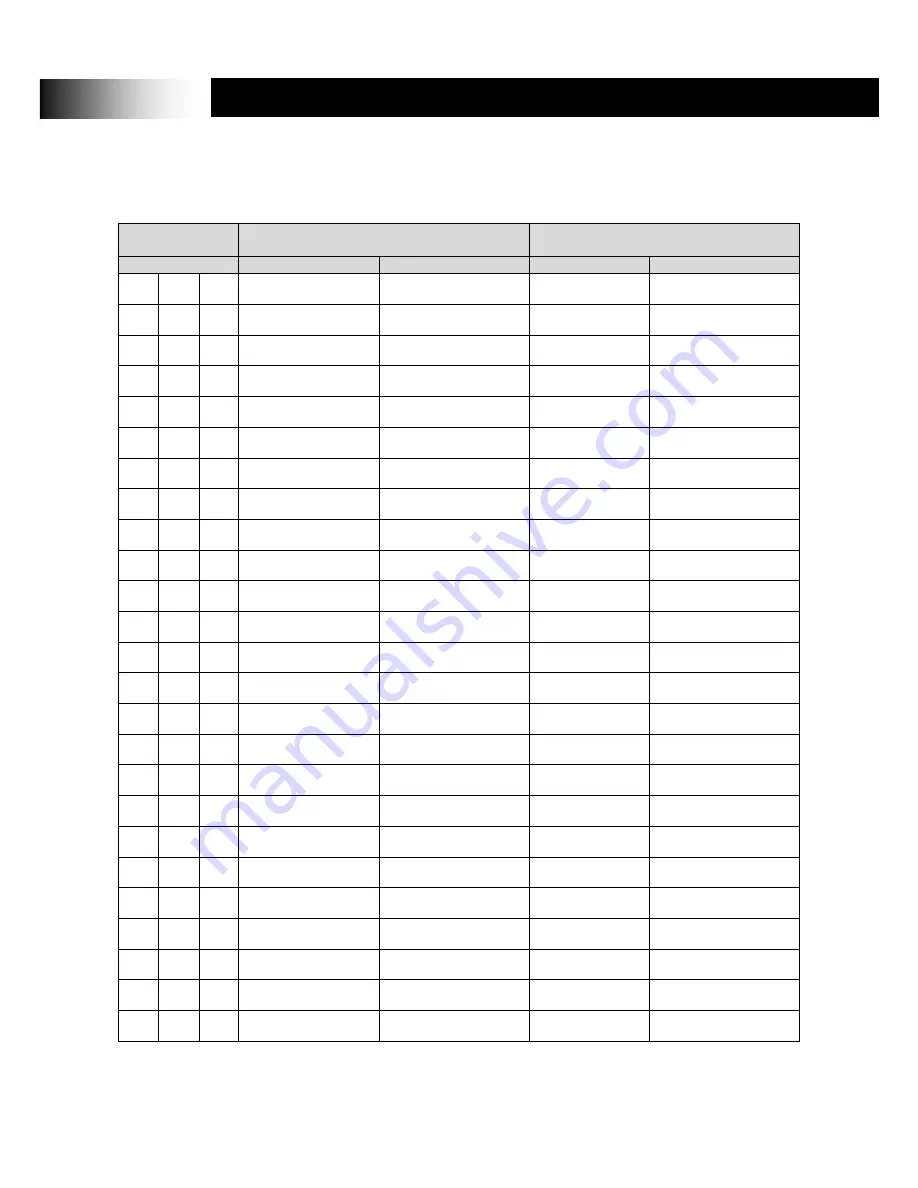
- 40 -
Shown below is a maintenance log format of a kind we recommend you to keep. Each time that you conduct a
maintenance service, such as replacement of a part, tear-down cleaning, post-failure repair, etc., record the
details. In the long run, you will find that such a log is very valuable in keeping your equipment in a
consistently good operating condition.
Equipment
name
Air wrap airless electrostatic spray gun
<ECCO Xtatic LP6000S/W/M>
Date of acquisition: YYYY/MM/DD
Date of service
Portion worked on
Description
Date of service
Portion worked on
In-house / ECCO Finishing AB
In-house / ECCO Finishing AB
In-house / ECCO Finishing AB
In-house / ECCO Finishing AB
In-house / ECCO Finishing AB
In-house / ECCO Finishing AB
In-house / ECCO Finishing AB
In-house / ECCO Finishing AB
In-house / ECCO Finishing AB
In-house / ECCO Finishing AB
In-house / ECCO Finishing AB
In-house / ECCO Finishing AB
In-house / ECCO Finishing AB
In-house / ECCO Finishing AB
In-house / ECCO Finishing AB
In-house / ECCO Finishing AB
In-house / ECCO Finishing AB
In-house / ECCO Finishing AB
In-house / ECCO Finishing AB
In-house / ECCO Finishing AB
In-house / ECCO Finishing AB
In-house / ECCO Finishing AB
In-house / ECCO Finishing AB
In-house / ECCO Finishing AB
In-house / ECCO Finishing AB
NOTE: Due to continuous improvements and modifications, the configurations and specifications of the
equipment specified herein are subject to change without prior notice.
14
Service record