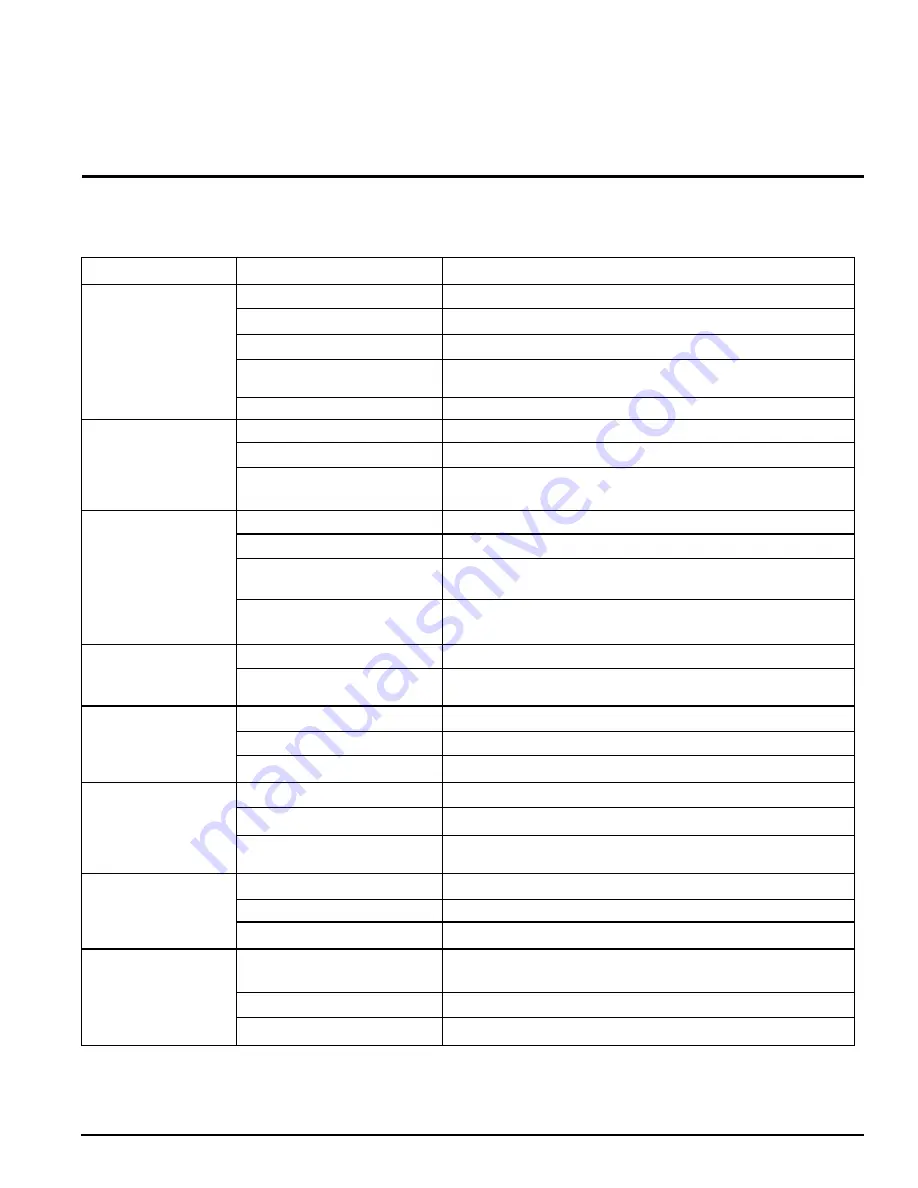
17
3 INCH CHIPPER/SHREDDER
ENGLI
sH
Section
TRoubLEsHooTING
6
pRobLEm
possIbLE causEs
REmEdY
Engine will not start.
Improper control settings.
use proper settings.
lack of fuel.
Fill fuel tank.
Spark plug disconnected.
Connect spark plug.
Dirty, stale or contaminated
gas.
Refill gas tank with fresh, clean unleaded regular gasoline.
Internal engine problems.
See your dealer.
Engine or rotor stalls or
stops.
Obstructed discharge.
use branch or similar object to clear discharge.
Plugged rotor.
Clear rotor. Feed material more evenly.
Feeding material too large into
shredder.
Reduce size of material being fed into shredder.
Chipper does not chip.
Dull chipper blades.
Rotate or sharpen blades.
Drive belts loose or worn.
Inspect drive belts, adjust or replace if needed.
Attempting to feed branches
that are too large.
limit branch size to 3 inches in diameter.
Broken or missing chipper
blades
Replace blade.
Engine overheats.
Cooling system plugged.
Clean cooling fan and fins.
Improper oil level.
Fill engine to correct oil level. Refer to the engine owners manual.
Hard to feed chipper;
requires excessive power
to chip.
Dull chipper blades.
Reverse or sharpen blades.
Obstructed discharge.
use branch or similar object to clear discharge.
Improper blade clearance.
Adjust clearance between chipper anvil and chipper blades.
Shredder requires
excessive power or stalls.
Obstructed discharge.
use branch or similar object to clear discharge.
Plugged rotor.
Clear rotor, feed material into shredder more evenly.
Wet or green material will not
discharge.
Alternately feed dry material or install larger discharge screen.
Engine stalls or belt
squeals when engaging
clutch.
Engaging clutch too fast.
Engage clutch more slowly.
Plugged rotor.
Clear rotor. Feed material more evenly.
Belt tension too loose.
Replace belt or spring.
Material from chipper
wraps around rotor shaft
Stringy, green material
bypasses chipper blades.
Rotate branch or material when feeding to cut completely.
Dull chipper blades.
Sharpen blades.
Improper blade clearance.
Adjust clearance between anvil and chipper blades.
Before performing any of the corrections in this troubleshooting chart, refer to the appropriate information contained in
this manual for the correct safety precautions and operating or maintenance procedures. Contact your dealer or the
factory for service problems with the machine.