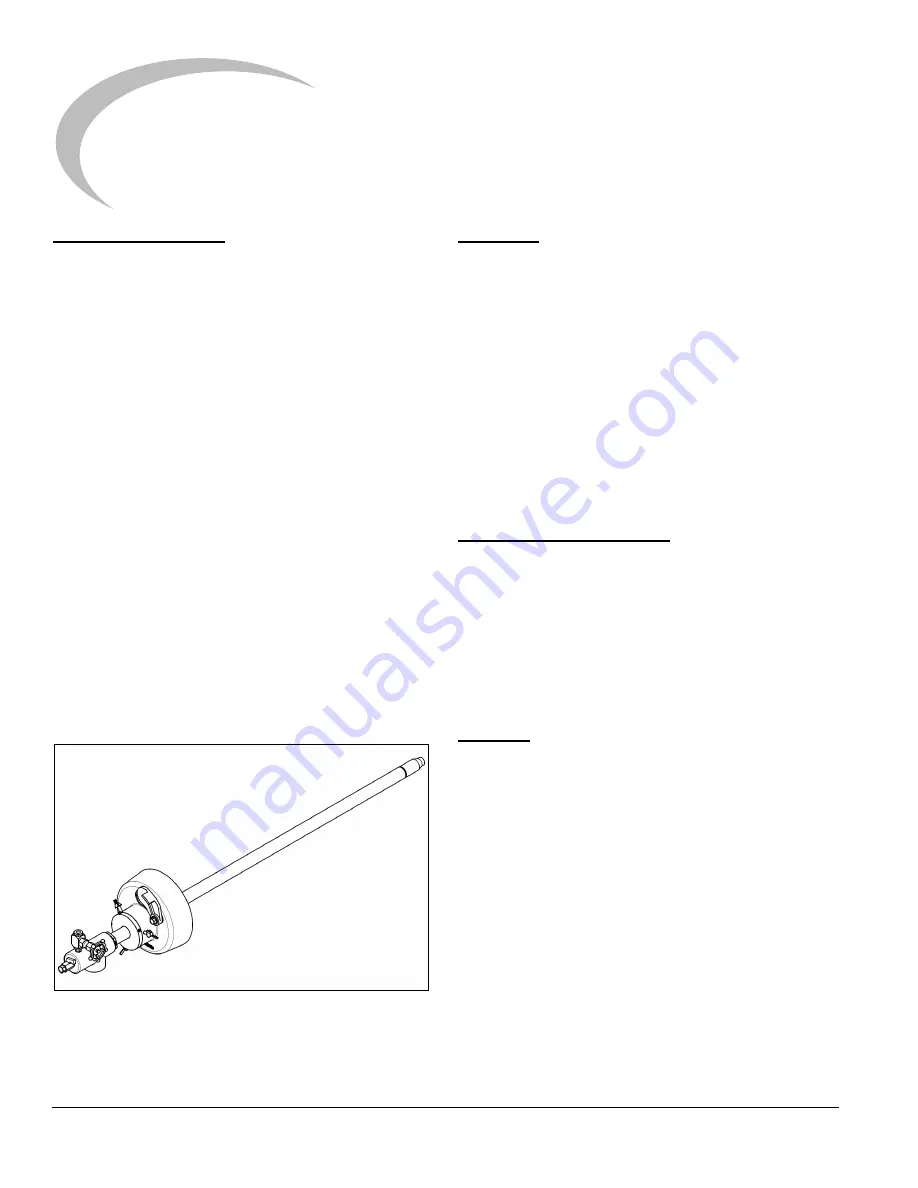
4
Eclipse Vortometric Burner, V3, Design Guide 248, 6/10/2010
Introduction
Product Description
The ExtensoHeat is a nozzle-mixing type burner intended
to operate in high-temperature firing kilns with very thick
walls and roof. It is also suitable for special applications in
which the flame must be developed away from the burner.
The ExtensoHeat is designed to inject the flame through
the thick wall in the combustion chamber, discharging a
strong jet of hot gases inside it.
The high speed of the combustion gases ensures
excellent temperature uniformity and high efficiency of the
system, which improves the product quality. The gas
velocity can reach 328 ft/sec (100 m/s). There are different
nozzle lengths ranging from 31 inches (800mm) to 55
inches (1,400mm).
Burner Specifications:
• Control options include on/off or group modulation
and pulse firing. Constant air flow.
• Self ignition by process temperature.
• Flame detection is not necessary (Temperature
above 1382ºF or 750ºC).
• Operability with other fuels.
• Designed to operate with excess gas in chambers
with an oxidizing atmosphere (O
2
> 12% vol.)
Figure 1.1. ExtensoHeat Burner
Audience
This manual has been written for people who are already
familiar with all aspects of a combustion system and its
add-on components, also referred to as “the burner
system.”
These aspects are:
• Design / Selection
• Installation
• Use
• Maintenance
The audience is expected to have previous experience
with this type of equipment.
ExtensoHeat Documents
Design Guide 235
• Used with Datasheet 235 to design the burner
system
Datasheet 235
• Required to complete design and selection
Installation Guide 235
• This document
Purpose
The purpose of this manual is to ensure the installation of
a safe, effective, and trouble-free combustion system.
1