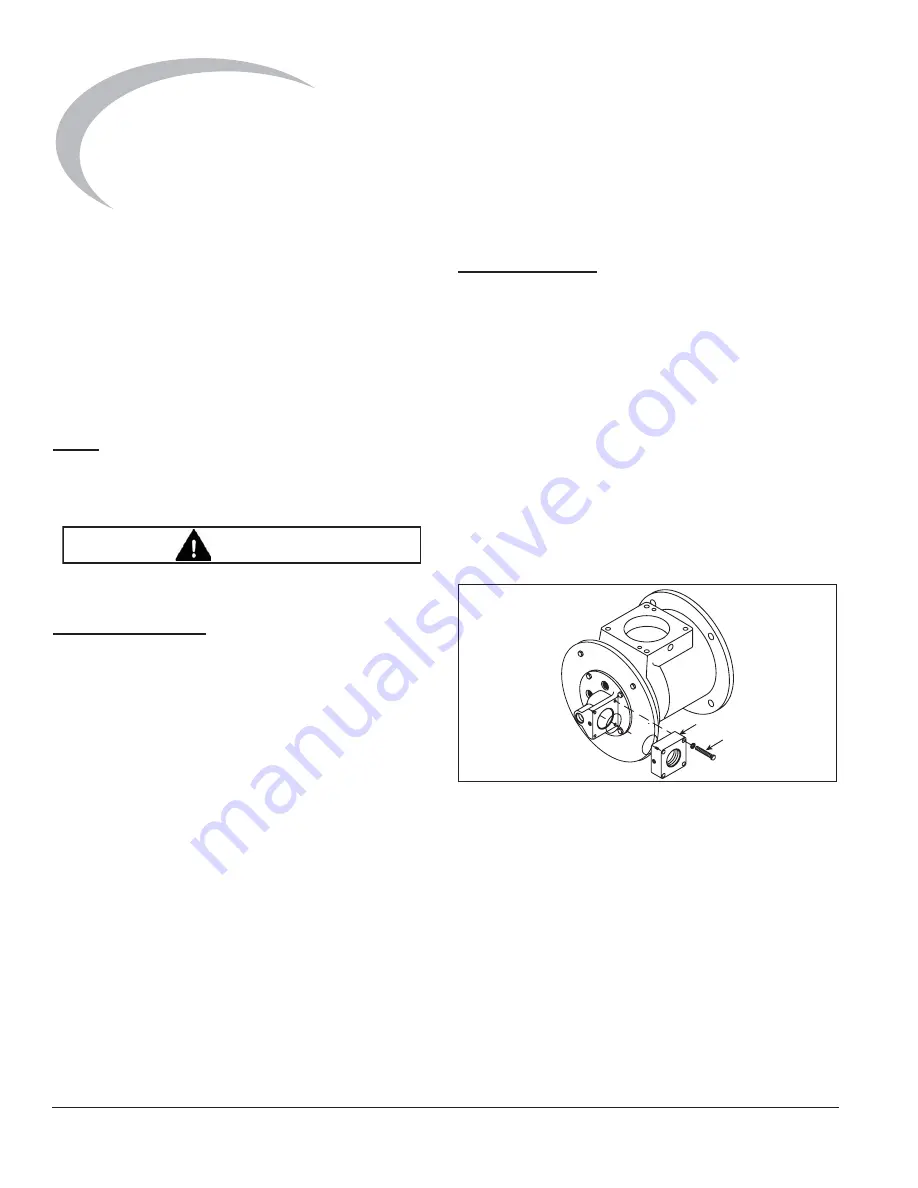
Eclipse Winnox Burner, WX Series, V2, Installation Guide 111, 2/26/2010
16
This section is divided into two parts. The first part
describes the maintenance procedures, and the second
part helps you to identify problems that may occur and
gives recommendations on how to solve these problems.
Preventative maintenance is the key to a reliable, safe
and efficient system. The following are suggested
guidelines for periodic maintenance. Burners in severe
environments or operational conditions should be
checked more frequently.
NOTE:
The monthly and yearly lists are an average
interval. If your environment is dirty, then the intervals may
be shorter. Check with local authorities having jurisdiction
on their recommended maintenance schedules.
Ŷ
Turn off the power to the burner and controls
before proceeding with burner inspection.
Monthly Checklist
1. Inspect flame-sensing devices for good condition and
cleanliness.
2. Check for proper air/gas pressures. Refer to the
Winnox datasheet, series 111.
3. Test all alarms for proper signals.
4. Check and clean igniter electrodes.
5. Check the air control valve for smooth, trouble free
operation and adjustment.
6. Check for the proper operation of ventilating
equipment.
7. Test interlock sequence of all safety equipment and
manually make each interlock fail, noting that related
equipment closes or stops as specified by the
manufacturer. Test flame safeguard by manually
shutting off gas to burner.
8. Test all manual fuel valves for operation.
9. Clean and/or replace the combustion air blower filter.
10.Inspect and clean the combustion air blower rotor.
Yearly Checklist
1. Test (leak test) safety shut-off valves for tightness of
closure.
2. Test pressure switch settings by checking switch
movements against pressure settings and compare
these with the actual impulse pressure.
3. Visually check ignition cable and connectors.
4. Inspect impulse piping for leaks.
5. Be sure the following components are not damaged or
distorted:
• the burner nozzle
• the igniter
• the flame sensors
• the combustion tube or block
Figure 5.1 Component Inspection
The nozzle can be inspected without removing the burner
from the chamber wall or entering the chamber. See
Figure 5.1 and Figure 5.2. Perform the following:
a. Shut the burner off and manually close the main gas
shut off cocks.
b. Allow the chamber temperature to cool down to
250°F (121°C).
c. Disconnect the gas piping at a union or the gas inlet
flange
X
provided on the burner.
d. Remove the four bolts
Y
.
CAUTION
Maintenance &
Troubleshooting
5