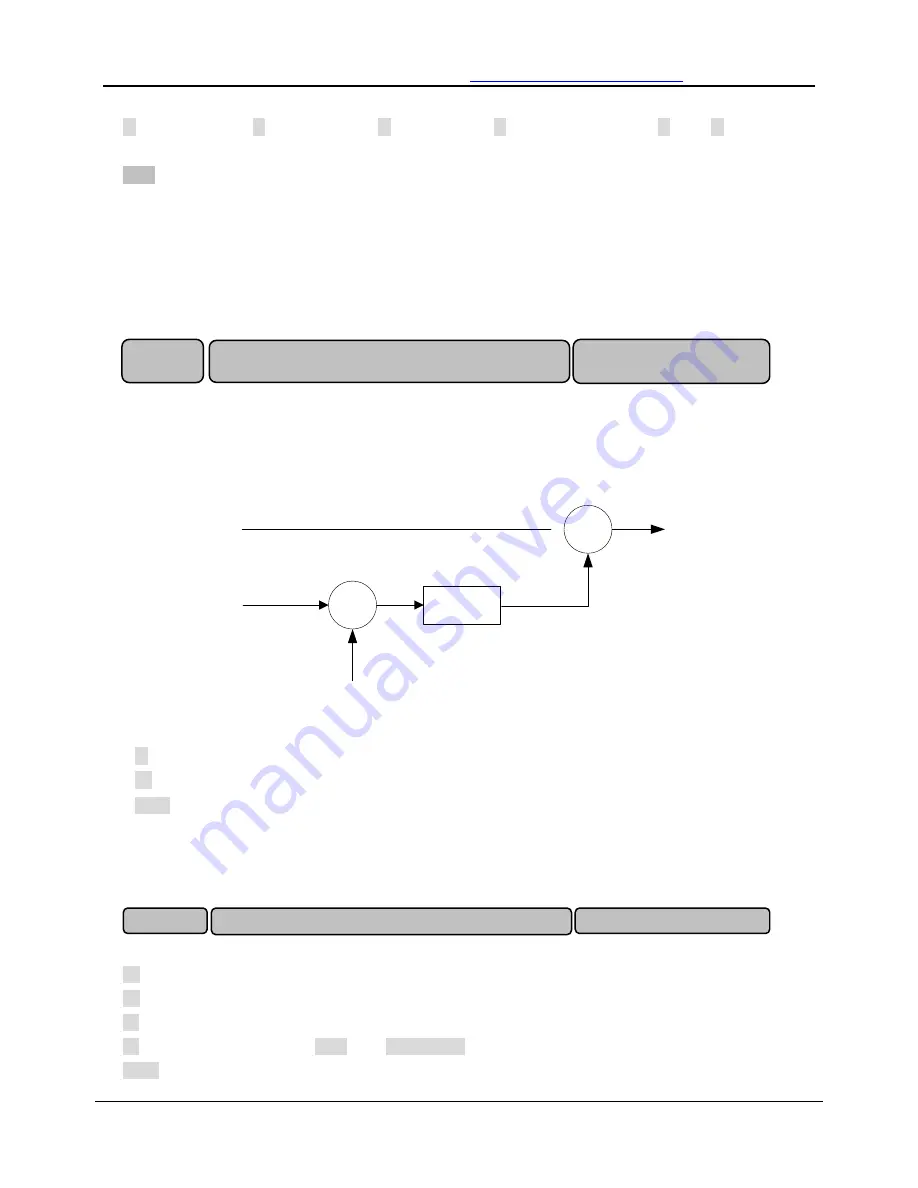
V&T Technologies Co., Ltd.
http://www.ecodrivecn.com
Chapter 6 Parameter Description
71
0: Main + auxiliary; 1: Main - auxiliary; 2: Auxiliary -50%; 3: Main+ auxiliary-50%; 4: Max; 5: Min.
Note:
Under the analog feedback close loop control mode, the analog main reference, analog auxiliary
reference, analog main feedback and analog auxiliary feedback cannot be set at the same
channel.
When the process close loop analog feedback mode is DI, the pulse will be translated into analog
(0~10V) as feedback:
Analog = pulse/maximum pulse input frequency P5.10×10V.
This function definition is similar to that of P1.01. The process open loop composite reference f
com
in this
function definition can be treated as main reference, the frequency output of closed loop PID adjustment f
PID
can be treated as auxiliary reference, and f
FIN
can be treated as composite reference.
f
PID
f
FIN
P1.08
Group
P8
PID
Adjustment
f
com
T
ref
T
act
Fig.6-10 Open loop and closed loop composite operation reference
0: Add the process closed loop adjustment result f
PID
to the process open loop reference f
com
1: Subtract the process closed loop adjustment result f
PID
from the process open loop reference f
com
Note: In the case of analog feedback closed loop, refer to description of P1.02 to P1.04 for the reference
mode T
ref
, refer to the description of P1.05 to P1.07 for the feedback mode T
act.
.
6.3 Key and Display Parameters (Group P2)
It is to realize the locking function of the keys on the operation panel, so as to avoid mis-operation.
0: The keys on the operation panel are not locked, and all the keys are usable.
1: The keys on the operation panel are locked, and all the keys are unusable.
2: All the keys except for the multi-functional key are unusable.
3: All the keys except for the RUN AND STOP/RST keys are unusable.
Note: For the effective methods of key locking, refer to 4.6 description on key locking and unlocking.
P1.08
Process open loop and close loop composite operation
relation calculation
0~1 (0)
P2.00
Key-lock function selection
0~3(0)