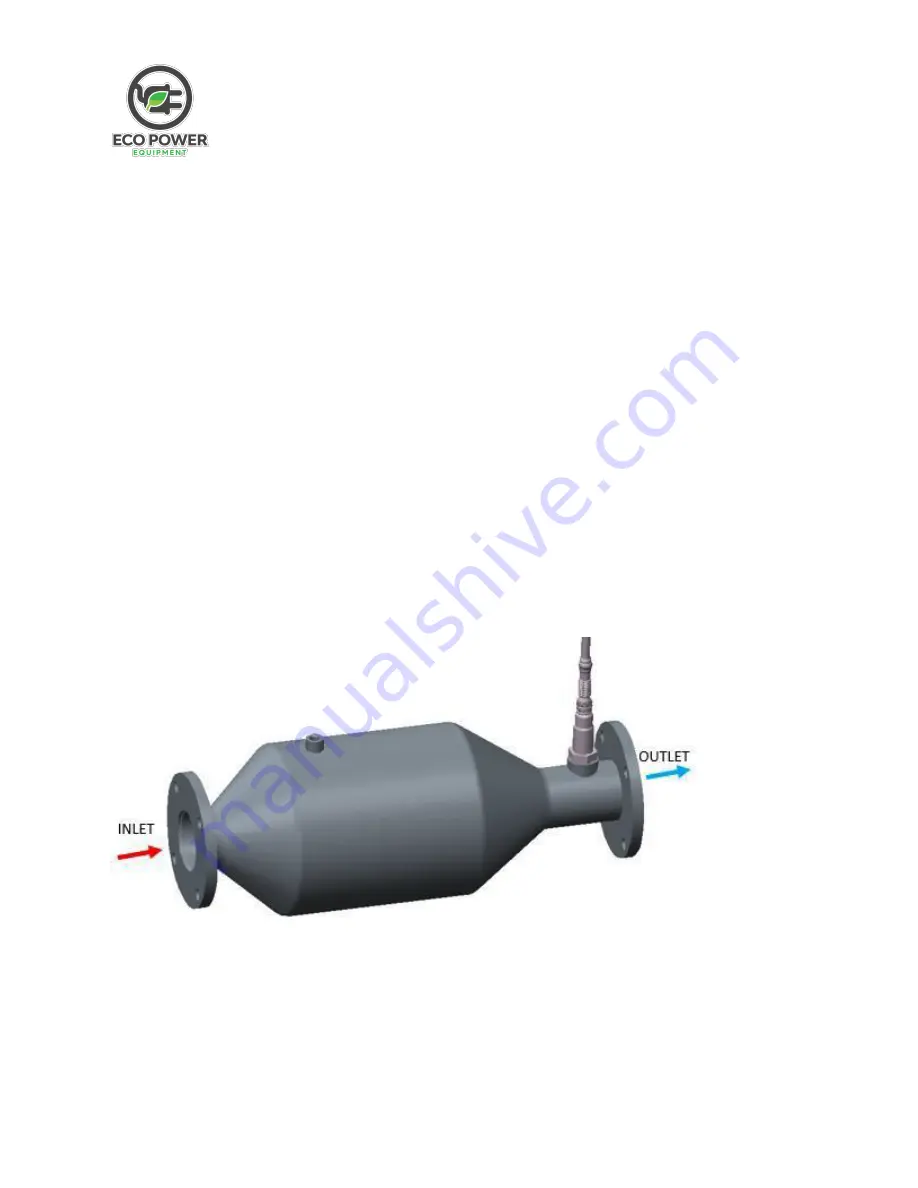
System measures:
Never switch on sensor heating before engine starting
Delayed switch-on or power control of the sensor heater (e.g. as a function of engine and ambient
temperature), so that the max. allowed ceramic temperature is not exceeded when there is
condensation water present
Installation angle should be inclined at least 10° towards horizontal (electrical connection upwards), thus
preventing the collection of liquids between sensor housing and sensor element during the cold start
phase. Other installation angles must be inspected and tested individually.
Avoid inadmissible heating up of the sensor cable grommet, particularly when the engine has been
switched off after running under max. Load conditions. The use of cleaning/greasing fluids or
evaporating solids at the sensor plug connection is not permitted. Assemble with high temperature
resistant grease on the screw-in thread. Tightening torque: 29.5ft-lb ~44 ft-lb (40 Nm~60 Nm). material
characteristics and strength of the thread must be appropriate. Recommended material for the thread
boss in the exhaust pipe is Temperature resistant stainless ferritic steel, e.g. X 5 CrNi 18 9, DIN 17440
1.4301 or 1.4303 or SAE 30304 or SAE 30305 (US standard)
The sensor’s protection tube must protrude completely into the exhaust-gas flow.
Figure 17 TWC and Post HEGO Sensor Installation
There is to be no possibility of the sensor protection tube contacting the opposite side of the exhaust
pipe. A waterproof electrical connector’s version is required.
The sensor must be covered when underseal (wax, tar, paint etc.) or spray oil is applied to the vehicle.
The influence of contamination which enters the exhaust gas through the intake air or as a result of fuel,
36