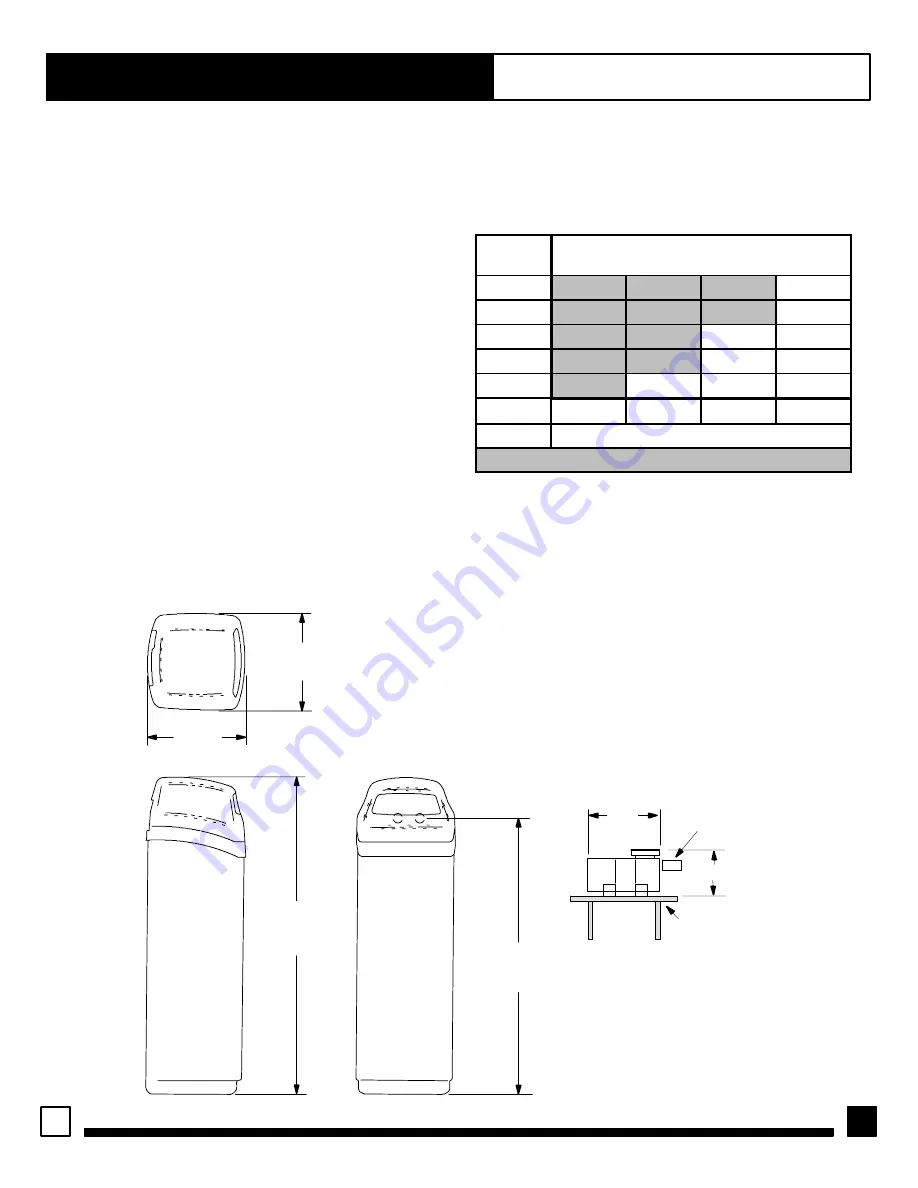
4
Specifications / Dimensions
ECOWATER
S Y S T E
M S
BIRM FILTER WITH AIR INJECTION ASSEMBLY
Filter Type . . . . . . . . . . . . . . . . . . . .
Oxidizing
Type of Mineral . . . . . . . . . . . . . . .
Birm
Amount of Mineral . . . . . . . . . . . . .
1 cu ft
Amount of Gravel . . . . . . . . . . . . .
17 lbs
Recommended Maximum Water
Supply Pressure . . . . . . . . . . . . . .
60 psi
Recommended Type Water
Supply . . . . . . . . . . . . . . . . . . . . . . .
Well System
Maximum Water Temperature . . .
120
_
F
Minimum Water Supply pH . . . . .
7.0
Maximum Service Flow . . . . . . . .
5.0 gpm
Minimum Backwash Flow
. . . .
5.0 gpm
Minimum In--Out Pipe Size . . . . .
3/4 in.
Electrical: Filter Timer . . . . . . . . . .
24V--60Hz
Electrical: Air Pump . . . . . . . . . . .
115V--60Hz
Some feed water with high iron concentrations, or
low pH may require limited service flows or a neutral-
izer filter before the system.
IRON
CONC.
MAXIMUM SERVICE FLOW RATE OF
IRON FILTER
20 PPM
4
4
4
4
15 PPM
4
4
4
5
10 PPM
4
4
4
6
5 PPM
4
4
5
7
2 PPM
4
4
6
8
6.5
7.0
7.5
8.0
pH
Neutralizer needed
Contaminant Removal Limitations:
.
up to 10 ppm iron* and 3ppm hydrogen sulfide at pH of 7.0 and higher
.
up to 20 ppm iron* and 2ppm hydrogen sulfide at pH of 8.0 and higher
.
up to 2 ppm manganese at pH of 8.5 and higher
*
except
, bacterial and organically bound iron
A minimum flow of 5 gpm is required for filter backwash.
7”
4---3/4”
Typical mounting
on shelf
Note: Air filter extends
an additional 4---1/2”.
AIR
PUMP
14”
14”
71 -- 3/8”
64 -- 1/2”