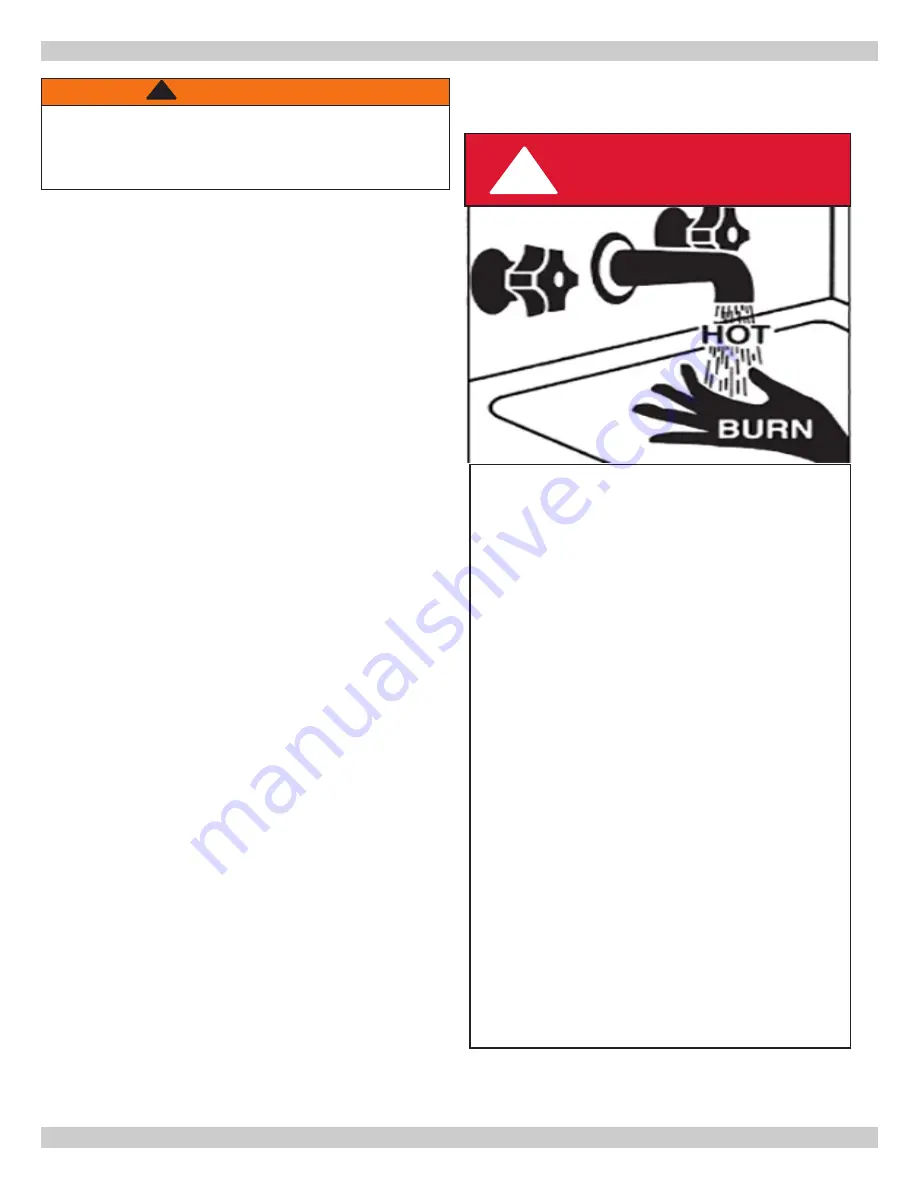
6
PN 240012875 REV. D [03/15/2022]
GENERAL INFORMATION - HYDRONIC PIPING
WARNING
Burn and scald hazard! Manufacturer requires
installation of field supplied anti-scald valve.
Failure to follow these instructions could result in
death or serious injury.
!
FOR YOUR SAFETY READ BEFORE OPERATING
DANGER
!
Hot Water Can Scald!
Water heated to temperature for clothes
washing, dish washing and other sanitizing needs
can scald and cause permanent injury.
Children, elderly, and infirmed or physically
handicapped persons are more likely to be
permanently injured by hot water. Never leave
them unattended in bathtub or shower. Never
allow small children to use a hot water tap or
draw their own bath.
If anyone using hot water in the building fits the
above description, or if state laws or local codes
require certain water temperatures at hot water
taps, you must take special precautions:
• Use lowest possible temperature setting.
• Install some type of tempering device, such
as an automatic mixing valve, at hot water
tap or water heater. Automatic mixing valve
must be selected and installed according
to manufacturer's recommendations and
instructions.
• Water passing out of drain valves may be
extremely hot. To avoid injury:
◊
Make sure all connections are tight.
◊
Direct water flow away from any person.
General Information:
Piping installation, materials, and joining methods shall
conform to requirements of authority having jurisdiction or
in absence of such requirements:
• USA
- National Fuel Gas Code, ANSI Z223.1/NFPA 54
• Canada
- Natural Gas and Propane Installation Code,
CAN/CSA B149.1
Manufacturer Requirements/Recommendations:
• Manufacturer requires all domestic hot water
(DHW) installations use an anti-scald valve
.
Local codes may require additional equipment
(expansion tank, relief valves, etc.) Select and
size equipment to suit installation and meet code
requirements.
• Use a water filter on potable incoming water supply
line.
• Manufacturer recommends use of a magnetic dirt
separator in the hydronic system where there are
cast iron or steel components, or where the previous
boiler was a cast iron heat exchanger. The abrasive,
extremely fine sediment is difficult to remove and can
deposit onto heat exchanger surfaces and accumulate
in pump cavities causing reduced efficiency and
premature wear.
• If the piping manifold is not used the ASME
temperature and pressure relief valve and
temperature and pressure gauge shall be installed
to conform to requirements of the authority having
jurisdiction. Refer to appropriate manufacturer
instructions for installation requirements.
• If the piping manifold is not used, a primary /
secondary piping arrangement is manufacturer
required, unless using Buffer Tank. A maximum of
12 in of separation between the supply and return
pipe (closely spaced tees) of the boiler shall be
maintained. Limit combined supply and return pipe
lengths to maximum linear lengths of 20 ft (6.1
m) between boiler and closely spaced tees, when
minimum ¾ in NPT pipe size is used. Linear length
may be increased if supply and return pipe size is
increased to limit pressure drop.
• Manufacturer recommends installing a shutoff
and purge valve to use during commissioning to
ensure the boiler does not shut down due to over
temperature. Do not install shutoff between boiler
and LWCO or pressure relief valve.
Summary of Contents for 100F
Page 33: ...33 PN 240012875 REV D 03 15 2022 MODEL 75 100 HEAT ONLY 75 100 HEAT ONLY WIRING DIAGRAM ...
Page 34: ...34 PN 240012875 REV D 03 15 2022 MODEL 125 HEAT ONLY 125 HEAT ONLY WIRING DIAGRAM ...
Page 35: ...35 PN 240012875 REV D 03 15 2022 MODEL 165 HEAT ONLY 165 HEAT ONLY WIRING DIAGRAM ...
Page 36: ...36 PN 240012875 REV D 03 15 2022 115 COMBI WIRING DIAGRAM MODEL 115 COMBI ...
Page 37: ...37 PN 240012875 REV D 03 15 2022 MODEL 150 COMBI 150 COMBI WIRING DIAGRAM ...
Page 38: ...38 PN 240012875 REV D 03 15 2022 MODEL 205 COMBI 205 COMBI WIRING DIAGRAM ...
Page 44: ...44 PN 240012875 REV D 03 15 2022 LOW WATER CUTOFF LOW WATER CUTOFF DETAIL NO NO YES ...
Page 49: ...49 PN 240012875 REV D 03 15 2022 3 FAULT SOLUTION SECTIONS ...