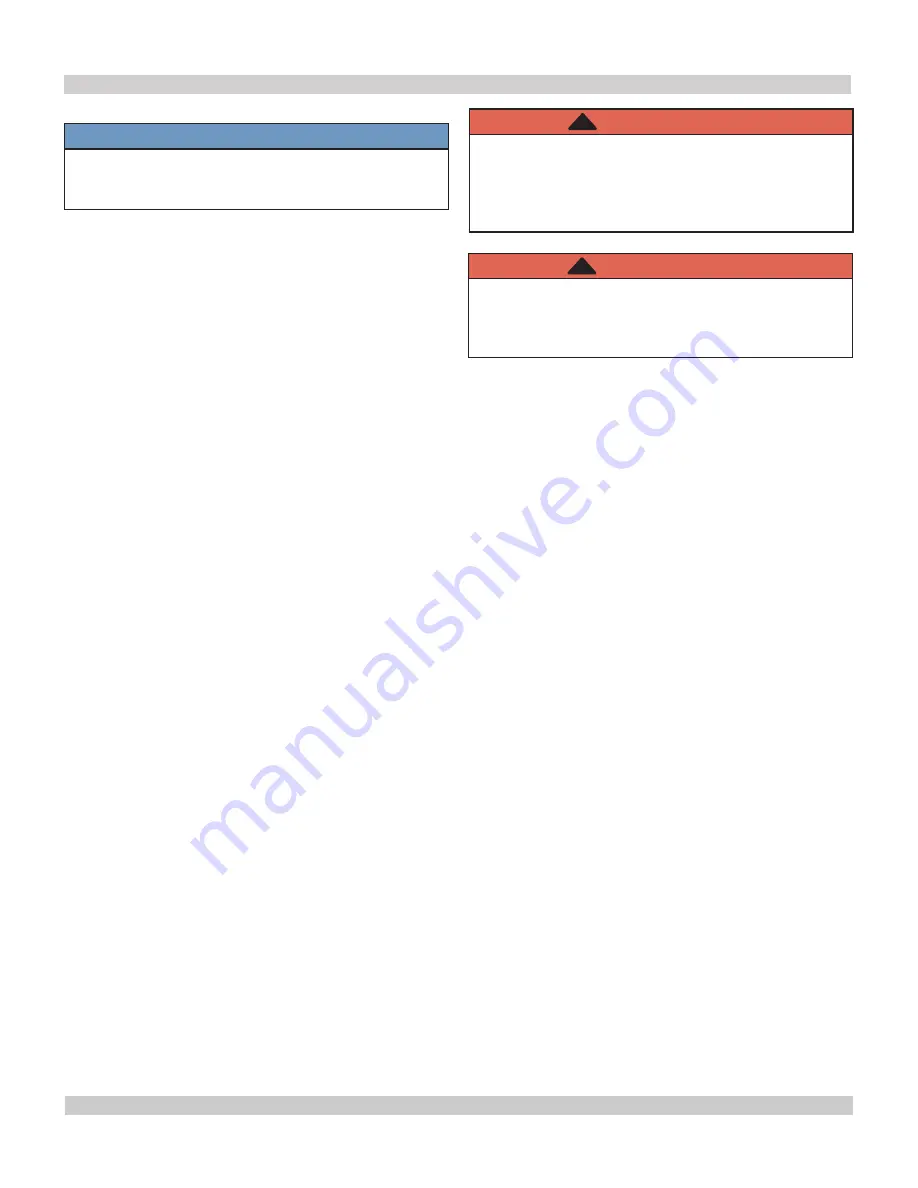
9.2
Boiler Start-up and Operational Test
1.
Verify air is purged from hydronic piping
2.
System test pumps - verify each pump is
operational
3.
Verify gas piping
• Con
fi
rm pressure test. See section 7.3 page 22.
• Visually inspect piping to determine there are no
open
fi
ttings or ends, and all valves at unused
outlets are closed and plugged/capped.
• Purge air from piping
• Check piping and connections for leaks immediately
after gas is turned on. Shut off gas supply and
make necessary repairs if leaks found.
4.
Follow OPERATING INSTRUCTIONS to initiate boiler
operation. See section 10.
5.
Inspect combustion air and vent piping. Verify pipe
is not leaking and terminations are unobstructed and
vent gas discharge is not a nuisance or hazard.
6.
Verify boiler operates.
7.
Check control module operation.
8.
Check
fi
eld sourced limits, low water cutoffs, etc. per
manufacturer's instructions.
WARNING
Asphyxiation hazard. Verify cap is
fi
rmly placed on
combustion analyzer port to prevent CO emission.
Failure to do so could result in death or serious
injury.
!
WARNING
Asphyxiation hazard. Carbon monoxide is odorless,
tasteless, clear colorless gas, which is highly toxic.
Carbon monoxide production shall not exceed
400ppm. Failure to follow these instructions could
result in death or serious injury.
!
24
9 - START UP PROCEDURE
9.1
Fill Boiler With Water And Purge Air
NOTICE
To maintain boiler ef
fi
ciency and prevent boiling
inside the heat exchanger,
fl
ush entire heating
system until clean.
• Flush heating system, including all heating zones.
• Fill boiler with potable water.
• Fill boiler and system piping with water (or
antifreeze-water solution, if used). See antifreeze
information Section 5.3 page 11. Purge air from
boiler using air vent. Purge air from system piping.
• Inspect system piping and boiler connections.
Repair any leaks immediately.
• Activate all heating zones and calls for heat,
including CH calls and DHW calls (if available).
• Do not open gas shutoff valve until all air is purged
from system.
9.3
Burner Pressure Adjustment
Unit has
fl
ame modulation, with two
fi
xed pressure values:
minimum and maximum. See sec. 12, page 33.
Connect pressure gauge to pressure point
“B”
downstream
of the gas valve.
1.
Remove protection cap “D”.
2.
Operate boiler in TEST mode.
3.
Adjust maximum pressure by turning screw “G”
clockwise
↷
to increase pressure and counter clockwise
↶
to decrease.
4.
Disconnect one of two connectors “C” from modulation
regulator “F” on the gas valve.
5.
Adjust minimum pressure by turning screw “E” clockwise
↷
to increase the pressure and counter clockwise
↶
to
decrease it.
6.
Turn burner on and off, verify minimum pressure
remains stable.
7.
Reconnect connector “C” detached from modulation
regulator “F” on the gas valve.
8.
Verify maximum pressure has not changed.
9.
Replace protection cap “D”.
10.
To end TEST mode, repeat activation sequence or wait
15 minutes.
9.4 To Enter Test Mode/Adjust Heating Power
Press CH+/- buttons at the same time for 5 seconds.
• 3 way valve is in CH position and burner is forced at
100%. Boiler automatically exits test mode after 15
minutes or to exit test mode manually press CH +/-
buttons together for 5 seconds.
• With Ch +/- buttons you can adjust Max power from (0
to 100%)
9.5 Ignition Adjustment
To adjust ignition, switch boiler to TEST mode (See Start
up Procedure). Press DHW buttons to increase or decrease
power (min.= 00, max. = 60). Press
RESET
button within
5 seconds and ignition remains set. Exit
TEST
mode.
Summary of Contents for CHB-100
Page 6: ...Figure 2 Component Listing 6 3 GENERAL VIEW AND MAIN COMPONENTS ...
Page 33: ...33 12 RATINGS AND CAPACITIES ...
Page 38: ...KEY Part Number Description Qty A01 FE3980B830 CASING CTR 1 38 REPAIR PARTS LIST CHB 100 ...
Page 40: ...40 REPAIR PARTS LIST CHB 100 ...
Page 42: ...42 REPAIR PARTS LIST CHB 100 ...
Page 44: ...KEY Part Number Description Qty A01 FE3980B830 CASING CTR 1 44 REPAIR PARTS LIST CHB 130 ...
Page 46: ...46 REPAIR PARTS LIST CHB 130 ...
Page 48: ...48 REPAIR PARTS LIST CHB 130 ...
Page 50: ...NOTES 50 ...
Page 51: ...NOTES 51 ...
Page 52: ...ECR International Inc 2201 Dwyer Avenue Utica NY 13501 web site www ecrinternational com ...