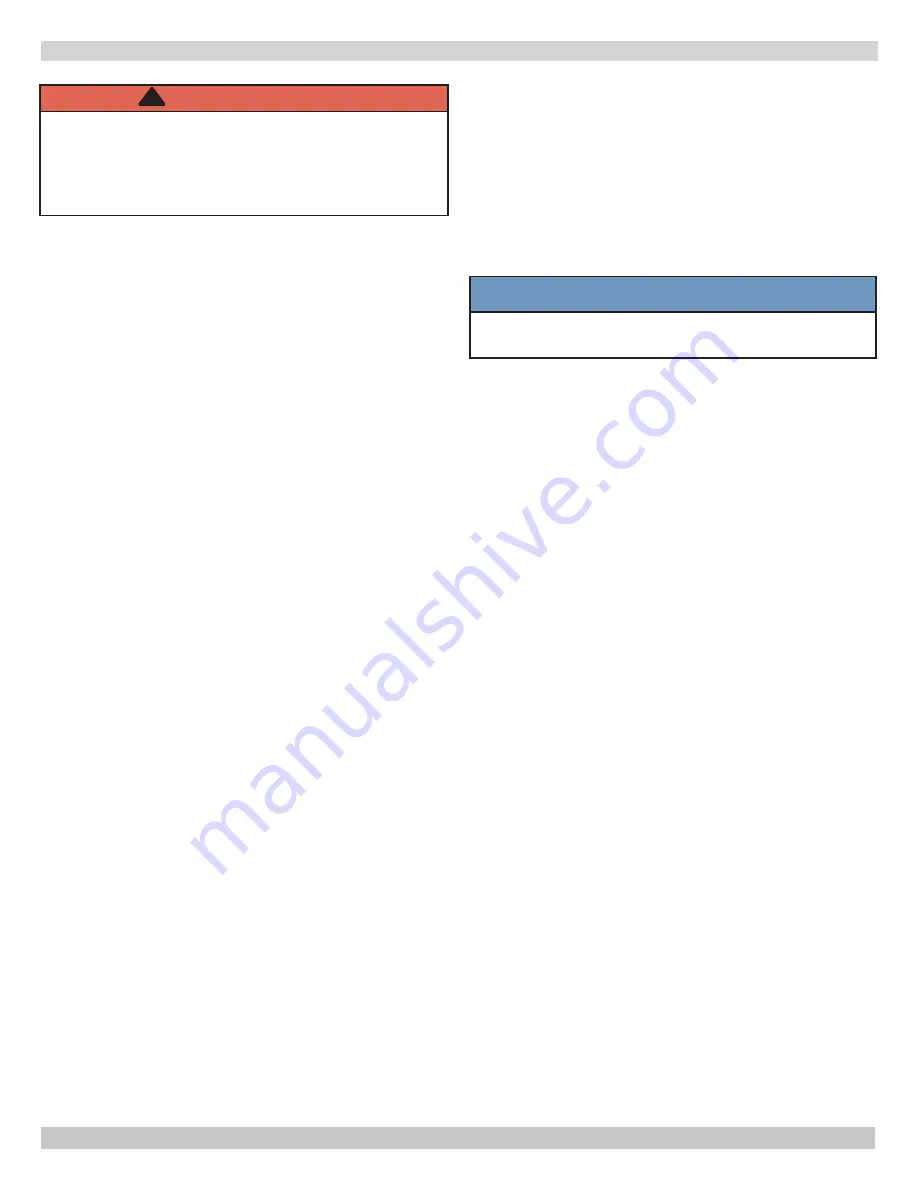
19
Impurities in boiler water
of a steam boiler may cause
foaming and an unsteady water line, or prevent steam
generation. They may result in objectionable odors
escaping from the vents on water boilers. This condition
is caused by oil, grease, and sediment from pipe fittings
collecting within the boiler and can be remedied only by
giving the boiler a thorough cleaning.
BOILERS SHOULD BE CLEANED BY SKIMMING OR
BLOWING DOWN.
NOTICE
Do not leave Boiler unattended during cleaning/
skimming process.
Skimming Off Impurities
Some of the impurities in the boiler water will float on the
water and must be skimmed off.
With the boiler empty and cool, slowly begin to add water.
After water has entered boiler - never before - turn “on”
oil burner and adjust water flow so that the water being
added is kept just below boiling point. Avoid boiling and
turbulence.
Gradually raise hot water level to skimming hole
(
Figure #7
)
installed on the rear section of the boiler being careful not to
raise it above the opening of the hole. Skim until there are no
impurities. Repeat the process if necessary.
Water may be checked to make sure it is free from oil by
drawing off a sample at the skimming hole. If the sample
is reasonably free from oil, it will not froth when boiled on
stove. This test does not indicate the amount of sediment
which may lay in the bottom of the boiler. It is therefore
necessary that the boiler be further cleaned by “blowing
down.”
Blowing Down The Boiler
Before blowing down the boiler, fill it to the water line.
Turn on burner and allow five pounds of steam pressure to
build up. Run a temporary connection from one of the drain
valves to a nearby sewer. Connect to a drain valve on the
opposite end of the boiler from feed water inlet, if possible.
Shut off the oil burner, open drain valve and blow down the
entire contents of boiler.
Allow boiler to thoroughly cool and slowly refill to water
line. Repeat as many times as required until blow off water
is clear. Owner should blow down boiler at least once each
month of the heating season.
Before seasonal start up it is advisable to have a qualified
service agency check boiler for soot and scale in flues,
change oil filter and nozzle, clean burner and re-adjust
burner input rate to maintain proper operation and high
operating efficiency.
On steam boilers verify boiler is filled to water line as
indicated in
Figure #14
. Gauge valves should be normally
open. To remove dirt from gauge glass petcock may be
opened to flush out the glass.
Radiator valves on one-pipe steam system must be either
wide open or tightly shut. Do not attempt to regulate room
temperature by partially closing the radiator valve.
Air vents on steam radiators and the supply main release
air from the system. If radiators do not heat satisfactorily,
make sure the air vents are clean and operational.
The lever of the pressure relief valve on the boiler
(
Figure
#14
)
should be operated periodically to make sure that it
is functioning properly.
Safety valve should open before the steam pressure
exceeds the 15 psi. reading on the gauge.
(
Figure #14
)
If this pressure is exceeded and the safety valve does not
open, it must be replaced. If the safety valve leaks steam
when the boiler is operating at normal pressures, it should
be immediately replaced. Corrosion can build up rapidly
at the valve seat and prevent its functioning as a safety
device.
If the water in a steam boiler appears to be dirty or oily, or
the water level in the gauge glass fluctuates considerably,
the boiler should be cleaned. A competent service person
will use approved cleaning compounds and properly clean
and flush out the boiler. He/she should also clean or replace
air vents and traps, clean flue passages and check for
proper operation of all controls and safety devices.
The venting system should be inspected at the start of each
heating season. Check the vent pipe from the boiler to the
chimney for signs of deterioration by rust or sagging joints.
Repair if necessary.
MAINTENANCE PROCEDURES
WARNING
Burn and scald hazard. Verify Boiler is off and
cooled before performing maintenance. Have a
qualified service agent perform maintenance. Failure
to follow these instructions could result in death or
serious injury.
!