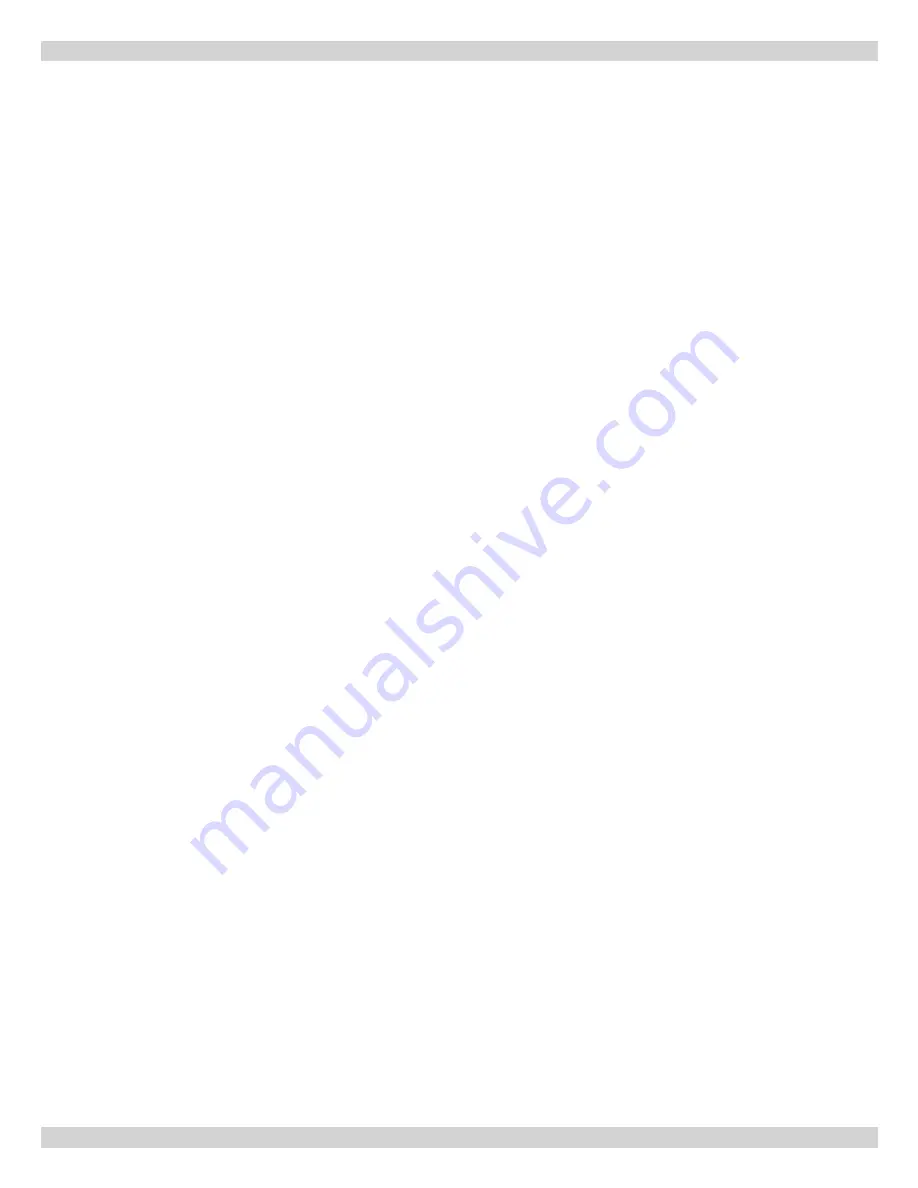
Acidic nature of flue gases condensing on aluminum boiler
sections cause formation of aluminum oxide. This oxide
formation is normal, and represents negligible mass of
aluminum consumed by oxidation during life of boiler.
If left unchecked, this buildup may eventually cause
blockage of flue gas passages in boiler sections, reducing
efficiency, and ultimately shutting boiler down due to lack
of combustion air flow, or drainage of condensate.
Regular service and maintenance by qualified service
agency must be performed at least once every 12
months to assure safe, trouble free operation and
maximum efficiency.
14.1 Beginning of each heating season
1.
Schedule annual service call by qualified service agency
which includes:
• Examine flue passages in heat exchanger, burner,
and condensate lines, and clean (if necessary) follow
instructions in “Annual Examination and Cleaning of
Boiler Components” page 26.
• Inspect venting and air intake system for proper
operation, immediately repair or replace any sign of
deterioration or leakage, and verify proper reassembly
and resealing of system.
• Check for and remove any obstruction to flow of
combustion air or venting of flue gases.
• Follow “Operating Instructions” Section 13. Follow
“Boiler Startup” Section 5 and “Checkout Procedures
And Adjustments”, section 6 of Control Manual and
Troubleshooting Guide.”
• Inspect condensate drain line for proper operation.
Check for deteriorated or plugged condensate drain line.
• Check all gasketed joints for leakage. Tighten bolts or
replace gaskets as needed.
• Remove jacket front and top panels, check for piping
leaks around safety relief valve and other fittings, and
repair if found. Do not use stop leak compounds.
2.
Verify boiler area is free from combustible materials,
gasoline, and other flammable vapors and liquids.
3.
Circulator pump and blower fan motor furnished with
boiler are permanently lubricated from factory and
require no further lubrication. Additional or non-factory
supplied pumps and/or motors should be lubricated
according to pump and/or motor manufacturer’s
instruction.
14.2 Daily During Heating Season
1.
Check for and remove any obstruction to flow of
combustion air or venting of flue gases.
2.
Check boiler area is free from combustible materials,
gasoline, and other flammable vapors and liquids.
14.3 Monthly During Heating Season
1.
Remove jacket front and top panels and check for
piping leaks around safety relief valve and other
fittings. If found, contact qualified service agency. DO
NOT use stop leak compounds.
2.
Test safety relief valve. Refer to valve manufacturers
instructions packaged with safety relief valve.
3.
Visually inspect venting and air intake system for
proper operation. If vent or air intake show any signs
of deterioration or leakage, contact qualified service
agency to repair or replace them immediately and to
insure proper reassembly and resealing of system.
4.
Visually inspect condensate drain pipe for proper
operation. If drain pipe shows any signs of blockage,
leakage, or deterioration contact qualified service
agency to clean, repair, or replace it immediately.
5.
Check air vent(s) for leakage.
6.
Periodic inspection of low water cut off is necessary,
including flushing of float type devices. Refer to low
water cut off manufacturer’s specific instructions.
14 - MAINTENANCE AND CLEANING
25
Summary of Contents for Dunkirk Q95M-200
Page 2: ...1 DIMENSIONS OPENING FOR SAFETY RELIEF VALVE DISCHARGE PIPE 30 785mm 39 1 1m 18 458mm 2 ...
Page 27: ...APPENDIX A BOILER PIPING AND WIRING Electrical Wiring Diagram 27 ...
Page 49: ...49 NOTES ...
Page 50: ...50 NOTES ...
Page 51: ...51 Company Address Phone Company Name Tech Initials Service Performed Date SERVICE RECORD ...