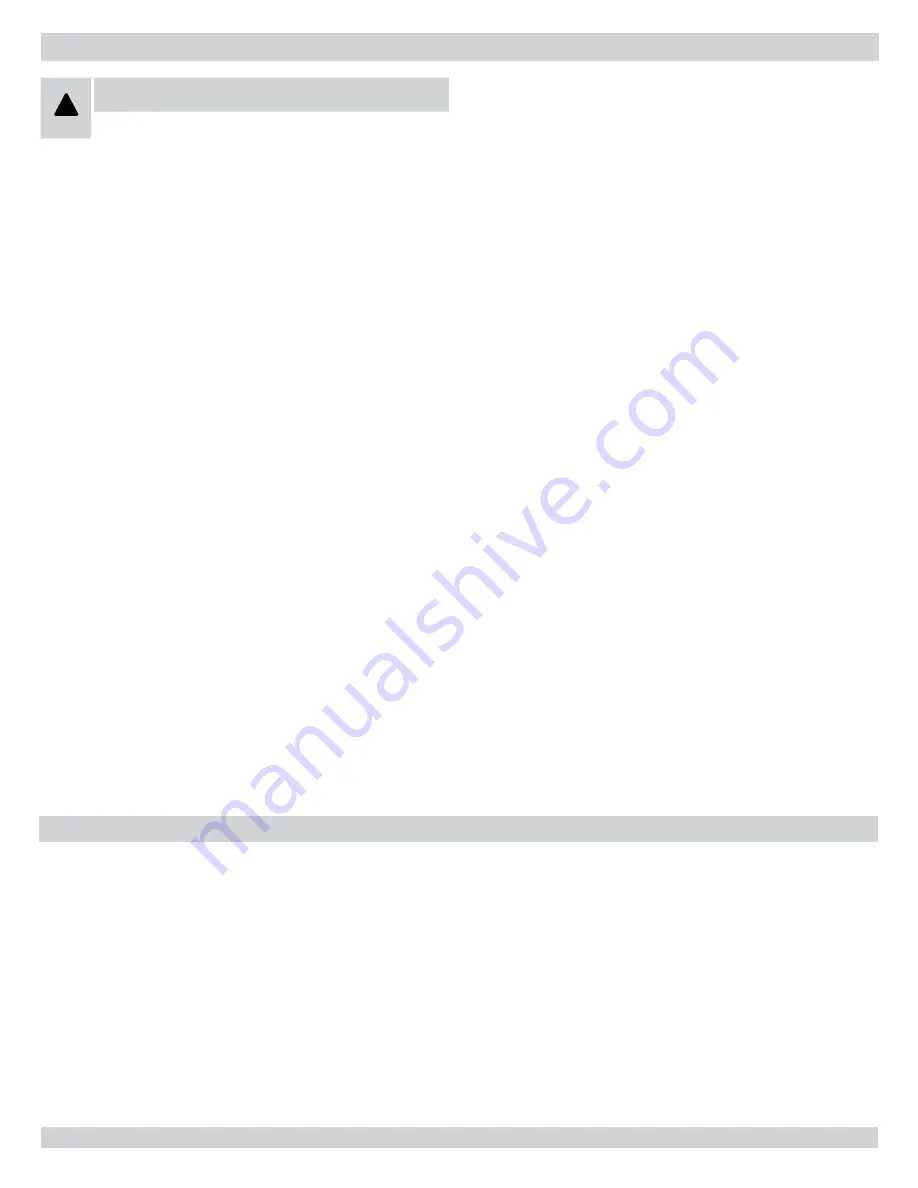
air proving blocked vent safety assembly
The air proving blocked vent safety assembly incorporates two
pressure switches that are designed to discontinue operation of the
appliance if there is a problem with the blower or venting system.
The normally open switch closes upon the initiation of the blower
and functions as an air proving switch. The normally closed switch
opens if there is a blockage in the combustion air intake or exhaust
vent pipes.
drain valve
The manual drain valve provides a means of draining the water in
the heating system, including the boiler and hot water supply and
return piping systems installed above the drain valve. This drain
valve is installed in the return piping at the bottom front of the boiler
section. Any piping installed below the elevation of this drain valve
will require additional drain valves to be installed at low points in
the piping systems in order to drain the entire system.
Xi - controls and accessories
!
WARNING
Never run cold water into a hot, empty boiler.
circulator pump
Every forced hot water system requires at least one circulating pump.
The circulating pump imparts the necessary energy to move water
through the closed loop supply and return piping systems, terminal
heating equipment (finned tube radiators, etc.) and back through the
boiler for reheating. To provide the required hot water flow rates, the
circulator pump must be properly sized to overcome frictional losses
(usually measured in feet of water, also referred to as “pump head
loss”) of the supply and return piping systems and boiler. The cir-
culator pump is furnished in a carton within the boiler cabinet. The
circulator(s) should always be located on the downstream (“pumping
away”) side of the expansion tank.
asme rated pressure relief valve
Each boiler must have a properly sized and installed American
Society of Mechanical Engineers (ASME) rated pressure relief valve.
Water expands as it is heated by the burner/boiler sections. If there
is no place for the water to expand its volume, (i.e., a properly sized
and properly functioning expansion tank) pressure on the inside
of the boiler and heating system will increase. The furnished relief
valve will automatically open at 30 psig pressure to relieve the strain
on the boiler and heating system from the increasing pressure. The
pressure relief valve discharge must be piped with the same size pipe
as the valve discharge opening to an open drain, tub or sink, or other
suitable drainage point not subject to freezing, in accordance with
ASME specifications. Failure to provide the pressure relief valve with
piping as herein described may cause water damage and/or serious
bodily injury. The boiler manufacturer is not responsible for any
water damage or personal injury. Check local codes for maximum
discharge height from floor.
external condensate pump (optional)
For installations where there is no floor drain or other appropriate
drainage receptacle available to receive condensate from the boiler,
an external float activated condensate pump with integral sump
is required. The condensate pump can be piped to a remote tie in
point to a sanitary sewer system. For this application, the boiler must
be installed so that proper pitch of piping to the external condensate
reservoir (sump) can be accomplished. Use wood frame or concrete
blocks to raise boiler as required for proper installation.
concentric vent/air intake termination (optional)
The optional concentric vent/air intake termination utilizes a single
opening per each appliance through the wall or roof of a structure.
Xii - water treatment & freeze protection
When filling the boiler water is the preferred heating solution. Most
potable water supplies may be used to charge and re-fill provided the
chlorine and chloride ions levels are less than 100 ppm.
Antifreeze may be used in most applications provided all of the fol-
lowing conditions are met:
Unless a strict schedule of sampling, analysis and maintenance
1.
of the antifreeze solution is followed, the boiler must be piped
as a primary loop connected to secondary loop as shown in the
Piping & Wiring Diagram Appendix. Failure to perform regular
maintenance to the antifreeze manufacturer’s instructions will
result in damage to the heat exchanger and the voiding of boiler
warranty.
Only the antifreeze manufacturers listed below are selected.
2.
At installation of a new or replacement boiler and at least on
3.
an annual basis the system antifreeze must be analyzed by the
antifreeze supplier or their recommended laboratory.
Adjustments to the system antifreeze must be made according
4.
to the antifreeze manufacturers recommendations using only
their recommended products.
All existing systems MUST be flushed of ALL old system fluid.
5.
Failure to do so may void the boiler warranty if evidence of
improper flushing is revealed.
Consult with your heating professional for recommendations.
piping recommendations
System leaks may not always be visible. An unseen system
•
19
Summary of Contents for UTICA BOILERS UB95M-200
Page 26: ...26 ...
Page 45: ...45 ...
Page 46: ...46 ...
Page 47: ...NOTES ...
Page 48: ...Date Service Performed Company Name Tech Initials Company Address Phone ...