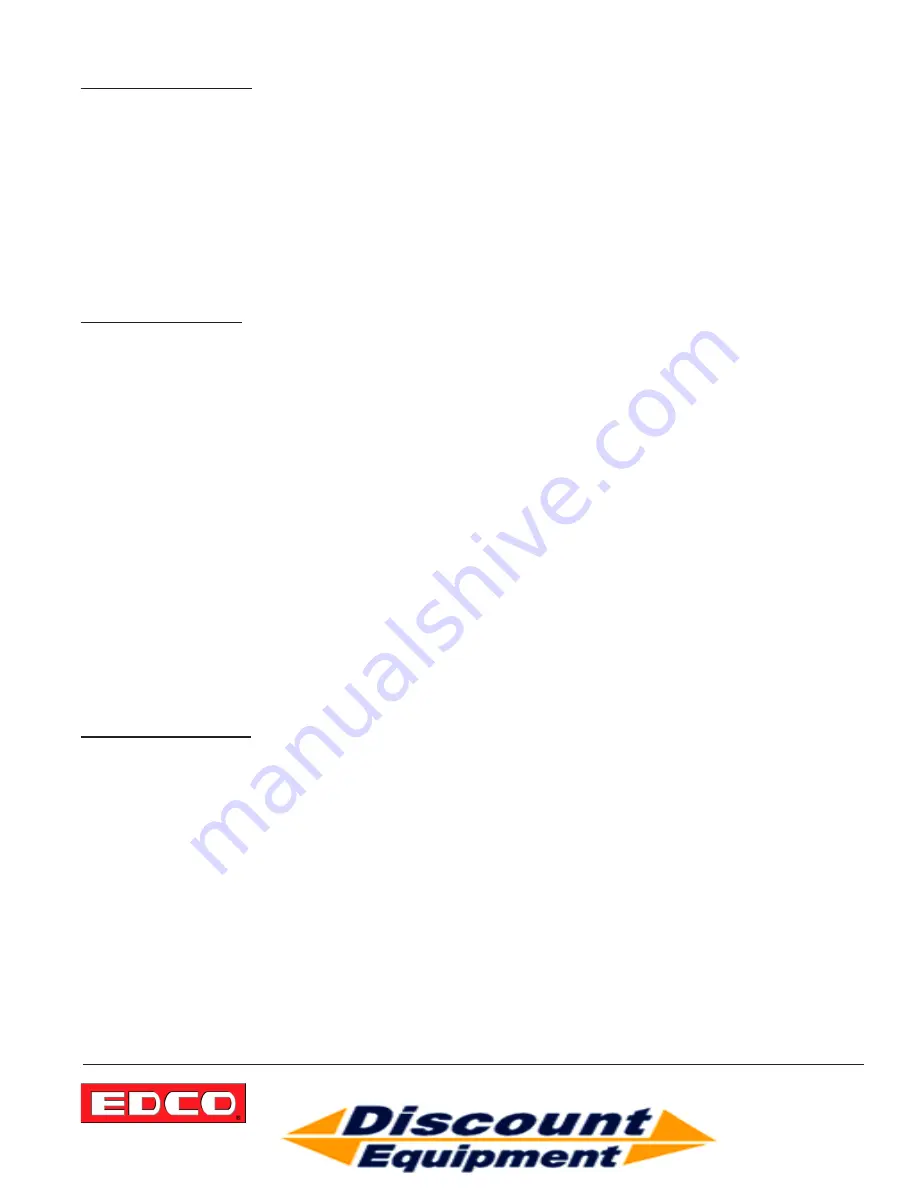
E-VAC290&VAC200-I-1017
Printed in USA
©2017
Page 5
Inspection and Maintenance VAC-200
Standard Filter Inspection
1. Turn the machine off.
2. Knock material off the filter via the hand shaker, motorized shaker or reverse pulse.
3. Pull up on the foot lever to release the dustpan then remove and empty if necessary.
4. Lock the rear casters then carefully tip the machine back onto the push handle.
5. Remove any material between the pleats, by hand only.
CAUTION: Clogged material should only be removed by hand. Using an object to dislodge material may tear the filter.
Consult your EDCO representative if material blockage is excessive.
6. Inspect the pleats of the filter for tears and material blockage.
7. Carefully tip the machine back onto the casters and replace the dustpan.
Standard Filter Removal
1. First follow the preceding filter inspection procedure to determine if removal is necessary.
2. Turn the machine on then block the inlet with a flat and rigid material to place the machine under vacuum pressure.
3. Remove all of the housing-component socket truss screws with a 5/32 hex-wrench.
4. Turn the machine off and disconnect the power source.
5. Separate the motor deck from the housing then disconnect the motor deck ground wire from the push-on terminal.
6. Disconnect the three power cord wires from the terminal block on the underside of the motor deck.
7. Remove the motor deck.
8. Disconnect the clear differential pressure gage tubes from their respective barbed fittings if so equipped.
9. Remove the HEPA filter housing spacer and HEPA adapter assembly if so equipped; make sure to disconnect the
HEPA adapter assembly ground wire via push-on terminal before removing.
10. Remove the reverse pulse/motorized shaker assembly and housing spacer if so equipped; make sure to
disconnect the component ground wire via push-on terminal before removing.
11. Inspect the top of the filter for material.
NOTE: The presence of material in this area or in the exhaust is often the result of a misaligned seal or damaged
filter. Consult your EDCO representative if either is the case.
12. Remove the filter housing spacer assembly; make sure to disconnect the filter housing spacer assembly ground
wire from the base via push on terminal.
13. Turn the filter housing spacer assembly over on a table then work the filter off the filter shaker insert.
Motor Brushes Inspection
1. Turn the machine off then disconnect the power source.
2. Disconnect both motor terminals.
3. Loosen the motor retaining knobs enough to remove both motors.
4. Remove the 12 screws from the bottoms of the motor assemblies.
5. Remove the plastic motor covers to access the tops of the motors.
6. Remove the 2 metal motor-cap-retaining clips per motor.
7. Carefully dislodge the plastic motor cap via the built in hooks on both sides of each motor brush.
(TIP: Dislodge one side of a cap first, then the other.)
8. Remove the motor brush retainers via the 2 phillips screws per brush.
9. Remove each of the brushes and inspect for excessive or uneven wear.
NOTE: A brush should be replaced if its length is less than 0.25 inches.
10. Reverse the procedure to install the brushes.
11. Reassemble and secure both motor assemblies with the 12 motor cover screws. Do not over tighten the screws,
as the cover will crack.
12. Position both motors in the deck and secure with the motor retaining knobs.
13. Connect both motor terminals.
www.discount-equipment.com
Discount-Equipment.com