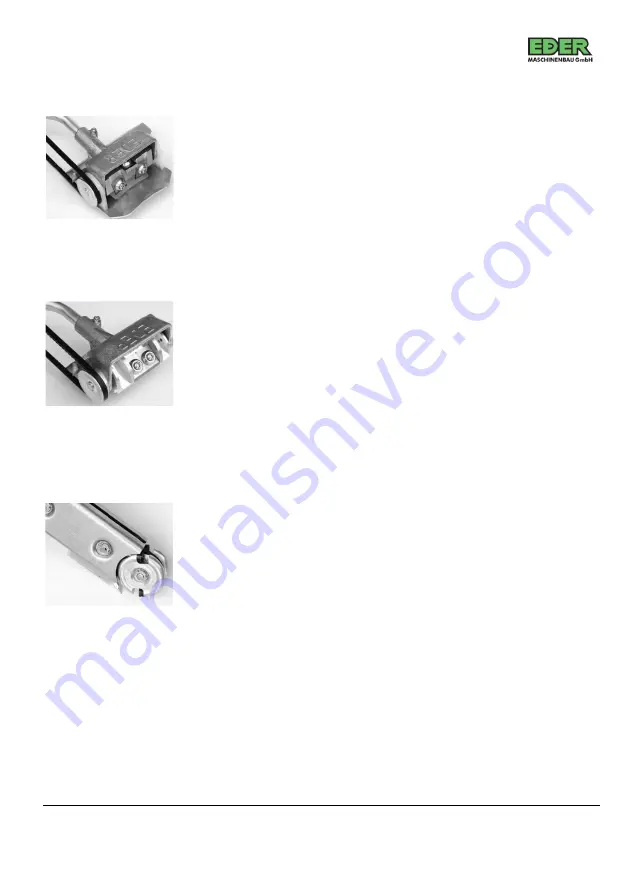
11
Eder Forestrytools
310003_04 | 06.2019
EDER Curved Planer Set ERH-A56
Field of application:
For planing round, flat or curved wood surfaces
up to 30 cm diameter.
The design of the cylinder results in high cutting performance with
minimum effort.
The knives mounted on the rotating cylinder are continuously
adjustable, allowing you to set both the cutting radius and the cutting
depth according to the desired chip thickness.
On the cylinder there are four knives distributed on two levels, which
produce a smooth surface without vibrations.
EDER Contour Planer Set EKH-A56
Field of application:
For planing straight and wavy wooden
surfaces, e.g. when building log houses, children's playgrounds,
bonanza fences and similar projects. Well suited for very hard woods
such as robinia wood.
The design of the cylinder results in high cutting performance with
minimum effort.
The adjustable minimum knife projection setting effectively prevents
the log from splitting. As one rotation of the cylinder means only one
cut at working width, the reaction forces are kept to a minimum.
Knots and thin branches are easily and cleanly planed off.
EDER Trough Cutter Set ETH-A56
Field of application:
For milling recesses in wooden surfaces, for
making troughs and sculptures, for surgical measures on trees and
for removing trunk pieces.
The design of the milling head results in high cutting performance
with minimum effort.
The circular knives are arranged so that the tool can be used for
performing work lengthwise as well as diagonally. Two circular
knives are fitted on the milling head, producing a smooth surface
without any vibrations. The minimum knife projection setting
effectively prevents the log from splitting.