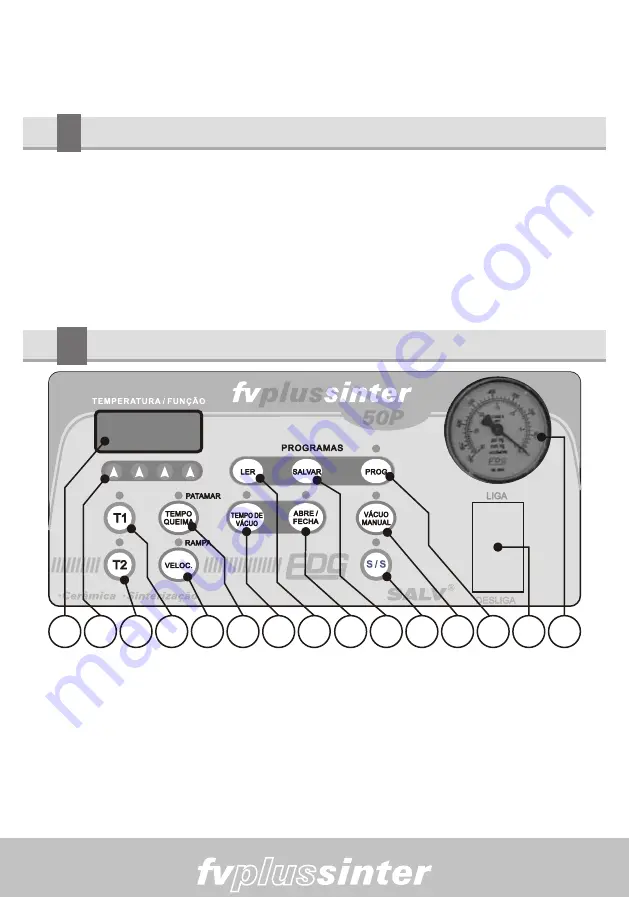
Manual
apropriados para esta aplicação.
4-7)
Connect the vacuum hose to the furnace PIC-1 item (4). Plug the vacuum
pump power cable to the outlet which is at the backside of the furnace PIC-1 Item
(05).
5
Control panel
5-1)
The control panel has a digital display with four red numeral digits which
provides easy identification of the programming functions and record monitoring. It
indicates some messages of the safety process such as system flaw and operation
mistakes.
5-2)
It has a touch sensitive thin layer which makes the activation of its keys and
functions easier.
5.
3
Identifying the keys and its functions
8
9 10 11 12 13 14 15 16 17 18 19 20 21 22
(08)
4 digits display.
(09)
Parameters programming adjustment keys
(10)
Temperature key T2, final burn.
(11)
Temperature key T1, piece entry.
(12)
Heating speed key (veloc.2). A2.
(13)
Burn time key (baseline). Pat-2.
(14)
Vacuum time key Vac-2.
(15)
Database recipes key.
(16)
Muffle opening and closing mode key (0 to 9
min).
(17)
Database recipe saving key.
(18)
Start / stop, key to begin and finish the burn
process.
(19)
Manual vacuum system key.
(20)
Database recipes access key, unlocks the
“save and read” (salvar e ler) functions.
(21)
Equipment main switch.
(22)
Analog vacuum indication.
6
Summary of Contents for Fv Plus Sinter
Page 1: ...Manual CAPA ...