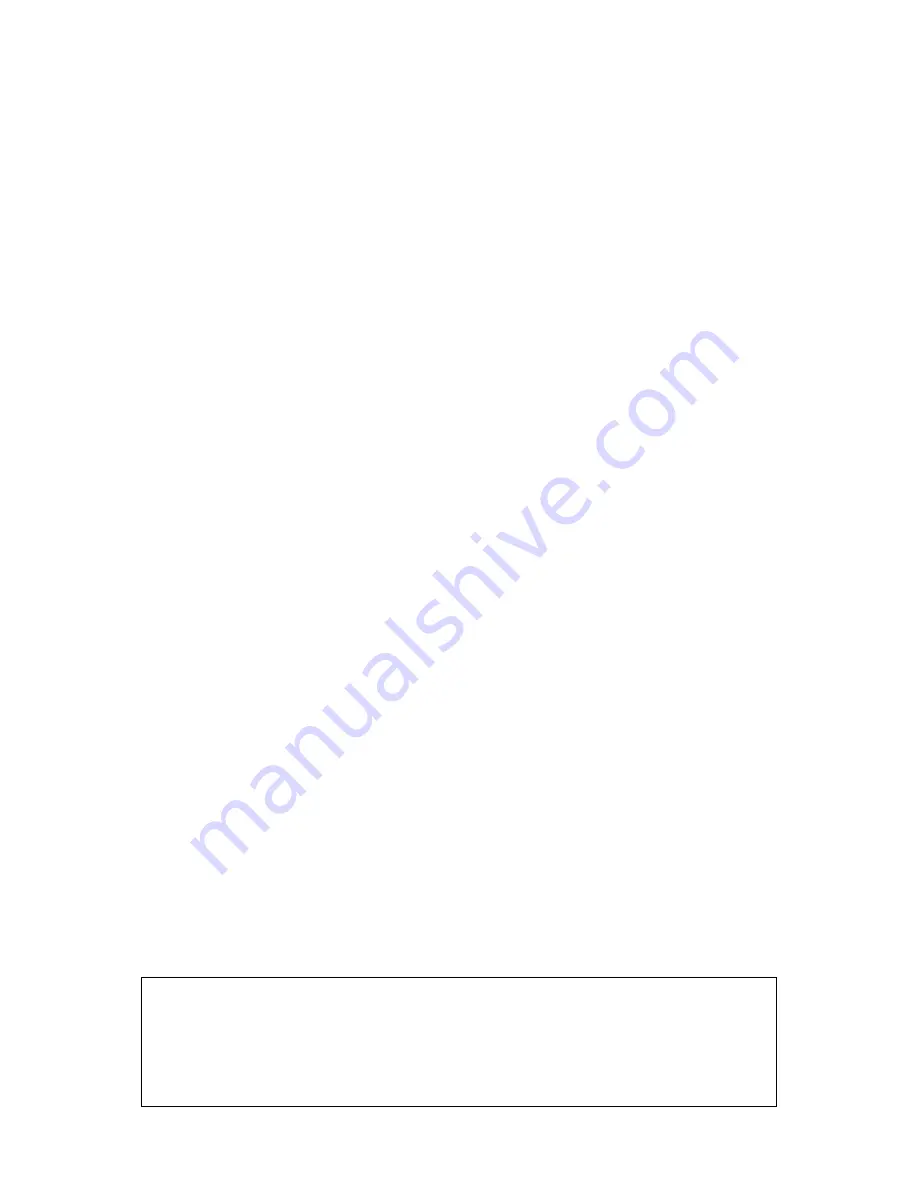
E D R O
D
y n a
W
a s h
®
T
h r e e
P
o c k e T
W
a s h e r
- e
x T r a c T o r s
63
S
ection
7
TROUBLESHOOTING GUIDE
INTRODUCTION
This chapter provides troubleshooting procedures, information and instructions to identify and
correct equipment malfunctions. Troubleshooting is the systematic analysis of a malfunction to
identify the cause of the malfunction. It requires a thorough understanding of the equipment
operation and an ability to recognize the symptoms of a faulty operation. Troubleshooting proce-
dures are divided into three phases: identification of the symptom or malfunction, identification
of the probable cause and performance of the corrective action. This chapter describes opera-
tional characteristics and general troubleshooting procedures. A troubleshooting table to assist
in systematically identifying and correcting operational problems and equipment malfunctions is
provided at the end of this chapter.
DYNATROL
The technology inherent in the modern electronic logic controller eliminates the requirement for
electro-mechanical devices such as control relays and timers and allows for exact operation of
the pre-programmed formulas through integrated electronic circuits, timers and counters. The
programming logic of the HMi DynaTrol control is a sequence design method for applications,
where outputs (motor starters, solenoid valves, LED’s, etc.) are activated according to the status
of specific achieved events or inputs (switches, push buttons, operator controls, etc.), consistent
with rules stored in the control’s ladder logic program. The ladder logic and its internal rules and
instructions, thus combine to form an all-electronic control able to monitor, and more importantly,
manage every operating aspect of the machine.
PRELIMINARY TROUBLESHOOTING
The HMi DynaTrol is fitted with a multitude of warning and alarm screens for notification of most
machine symptoms and malfunctions. Warnings are resettable conditions such as failure to
reach water level in a predetermined configured time. Once reset, warning screens return to
operation screens and continue machine operation. Alarms are fatal errors which halt machine
operation such as activation of the emergency stop button. Once reset, alarm screens go to
alarm log screens. Navigation through these screens show current alarms, history of last 100
alarms, and total count of alarm frequency. See lists of warning and alarm screens.
When troubleshooting alarm conditions, most symptoms/malfunctions may be detected by sight,
sound, smell and touch. First, check components indicating failure. When a variation from the
normal operating condition is noted, the symptoms and causes must be determined. Attempts
should be made to reduce the most likely causes of a malfunction. Unusual sounds or overheat-
ing may point directly to certain components or parts. Also, components that have been recent-
ly installed or serviced are possibly the source of failure.
NOTE
In many troubleshooting cases the apparent malfunction may in fact be a result of a
specific program feature or interlock. If the program does not appear to be advancing
properly and the cause of the malfunction is not obvious refer to the symptoms in .