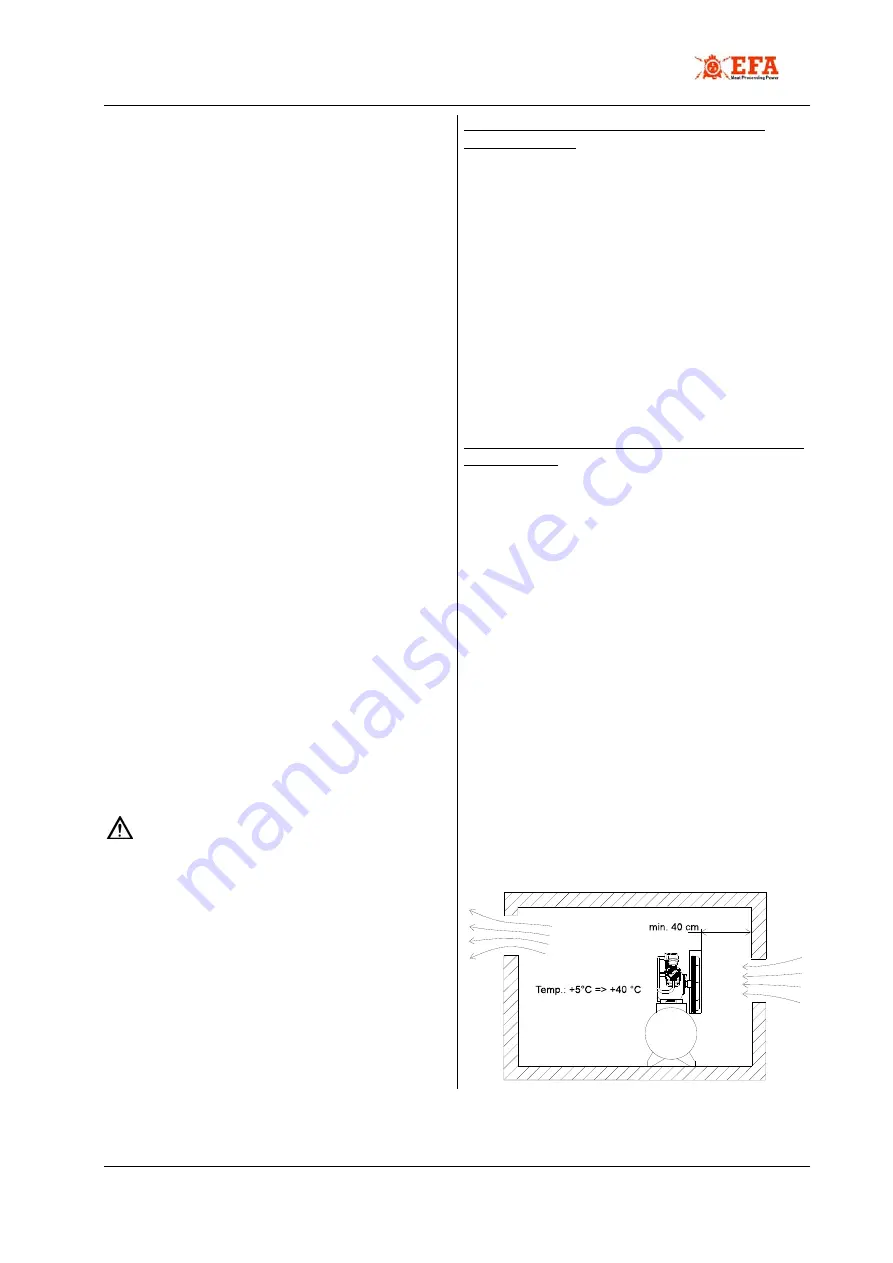
Operating instructions
6
•
Work on electrical machinery or drives must not
be carried out except by a qualified electrician,
or persons with the necessary training under the
supervision of a qualified electrician, and in
compliance with the regulations applicable to
electrical equipment.
•
Please note that for units with combustion
engine special safety preventions have to be
observed.
•
Always switch the machine off when it is not in
use.
•
If you are working at any height above your
normal working height, use suitable ladders and
platforms that meet the relevant safety
instructions. Do not use any part of the machine
as support for climbing.
•
Operating and maintenance personnel must
wear suitable working clothes. Rings and other
jewellery must be removed before work starts
on the machine. Long hair must be tied up
under a hair-net or similar.
•
Goggles or similar eye protection must be worn
for work with compressed air, as loose parts and
particles of dirt can be blown into the face.
•
When operating the machine, wear personal ear
protection of the right kind for the noise level
involved.
•
Never aim compressed air at any person - you
could cause injury!
•
Compressed air from a compressor must never
be used for inhalation without first being
properly treated. The laws and industrial
standards in force in your location apply.
•
Keep children and animals well away from this
machine.
TRANSPORTATION
Warning
!
- keep away from suspended
loads
A suspended load could crash to the ground, and
could cause very serious injury. It is strictly
forbidden to move or stand in the danger area
underneath a suspended load.
CAUTION! Improper lifting
Lifting the compressor in the wrong way can
damage it, so only ever lift this compressor at the
points provided. Never lift it by its cladding or by the
compressor block.
WHEN LIFTING AND TRANSPORTING THE
COMPRESSOR:
•
Let the air off from the machine
•
Undo the connections
•
Secure loose or moving parts
•
Adhere to local safety regulations
•
Only ever use suitable lifting gear with sufficient
lifting capacity.
SETTING UP AND CONNECTING
SETTING UP
Set the compressor up in a cool, dry place.
To dampen noise and vibration, we recommend the
use of damping rubber elements or oscillating metal
parts.
PLEASE PAY PARTICULAR ATTENTION TO THE
FOLLOWING:
•
The air receiver should be easily accessible
from all sides.
•
The distance between the ventilation wheel on
the machine and the nearest wall must never be
less than 400 mm.
•
The surface on which the compressor stands
must be level and capable of bearing the weight.
•
The ambient temperature must lie between
+5°C and +40°C.
•
The room in which the compressor stands must
be adequately ventilated.
•
The suction air must be clean. Caustic,
combustible or poisonous gases must not be
suctioned.
•
The filter insert of the air suction filter has a
separation degree of 10
μ
m. All particles of
more than 10
μ
m are filtered out of the suction
air. Smaller particles can pass through the filter.
If the compressor is operated in a place where
fine dusts exisit (cement plant ,gravel plant or
building sites etc.) an optional filter insert with a
separation degree of 3
μ
m must be used.
Summary of Contents for 001 606 885
Page 1: ...Betriebsanleitung 2 Operation manual VB 125 235 Type VB 125 to 235 PISTON COMPRESSORS...
Page 3: ...Betriebsanleitung 4 EFA 6 EFA...
Page 4: ...Betriebsanleitung 5...
Page 5: ...Betriebsanleitung 6 40 5 C 40 C 10 10 3...
Page 6: ...Betriebsanleitung 7 0 0 1...
Page 7: ...Betriebsanleitung 8 0 15 20...
Page 9: ...Betriebsanleitung 10 500 100 M 8 25 M 10 50 M 12 85...
Page 23: ...Schmid Wezel D 75433 Maulbronn Page 13 15 Version 09 2008 A 4...
Page 24: ...Schmid Wezel D 75433 Maulbronn Page 14 15 Version 09 2008 A 5 Installation plan 200 2000...