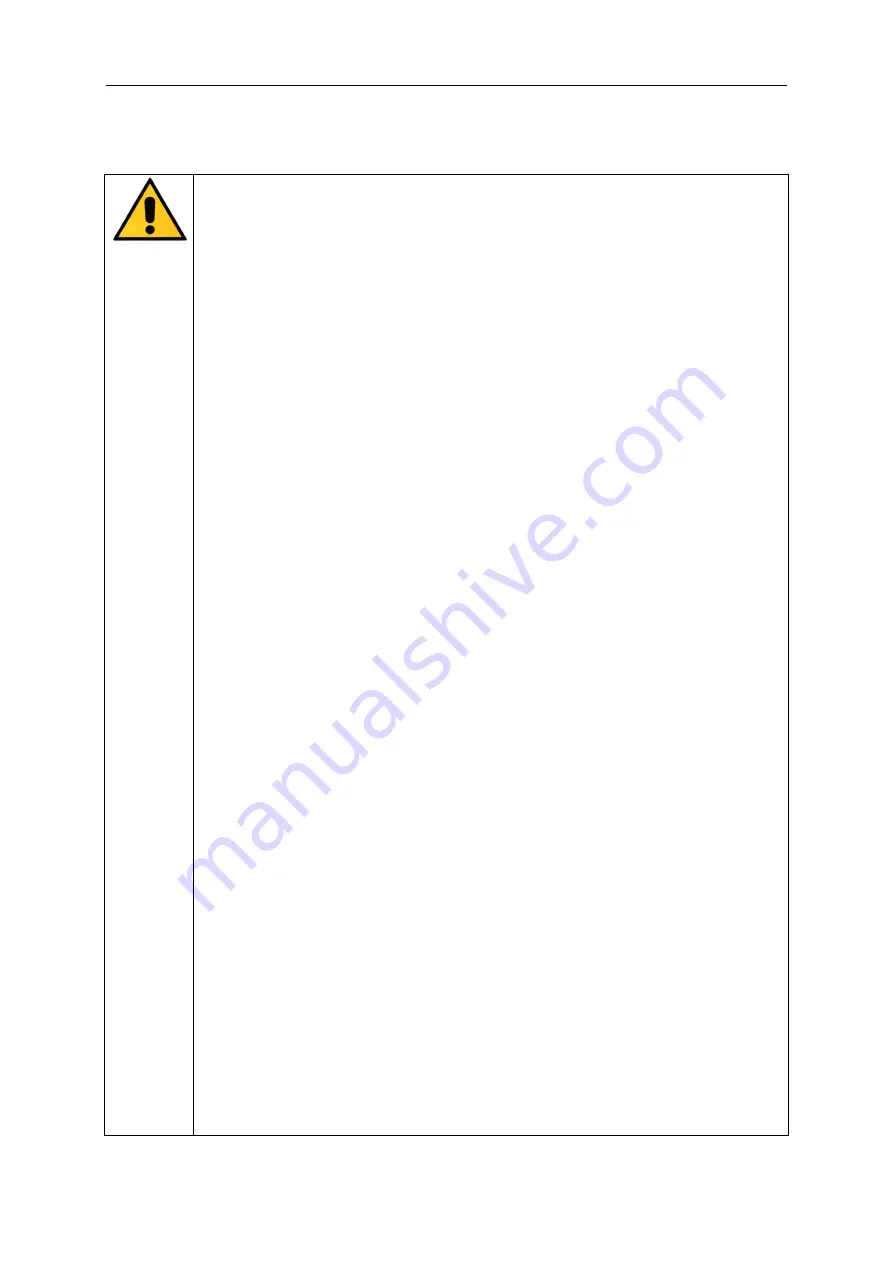
ER15-4-1600 Quick Operation Manual for Industrial Robot
第
6
页
1.3.3 Safety when the robot starts
Danger
To start the robot, first connect the power cord, and then turn the power switch from
OFF to ON. For these operations, please strictly abide by the following items and refer
to relevant domestic/international standards.
The robot complies with the safety requirements for robots used in industrial
environments (GB11291.1-2011/ISO10218-1:2006) for the design of safety functions.
Before starting the robot, make sure that the emergency stop switch is working
properly.
1. Before operation, please read and understand all manuals, specifications and other
related documents provided by EFORT. In addition, a complete understanding of
operations, teaching, maintenance and other processes. At the same time, confirm that
all safety measures are in place and effective.
2. Check the names and functions of all switches, displays and signals necessary for
robot operation.
3. Do not enter the safety fence unless the power supply of the robot is disconnected. At
the same time, confirm that the safety protection devices function normally before
starting the robot.
4. If there are several operators working together in the robot application system,
make sure that all operators and related personnel know that the robot has been
activated before starting the robot.
5. Before turning on the motor power, starting teaching or automatic operation, please
reconfirm that there are no workers or remaining obstacles in the robot safety fence or
around the robot.
6. When starting the robot and resuming operation from a faulty state, please put your
hand on the emergency stop switch after turning on the power of the control cabinet,
so that you can immediately cut off the power of the motor in the event of an abnormal
situation.
7. Before activating the robot, please reconfirm that the following conditions are met.
Confirm that the installation status of the robot is correct and stable.
Confirm that all connections of the robot control cabinet are correct, and the
power supply specifications (power supply voltage, frequency, etc.) meet the
requirements.
Confirm that various application connections (water, compressed air,
shielding gas, etc.) are correct and consistent with specifications and models.
Confirm that the connections with peripheral devices are correct.
Please confirm that in addition to the software motion limit, a mechanical
limit block/or limit switch has been installed to limit the robot's motion
range.
When the robot is stopped by a mechanical limit stop, please make sure to
check the relevant parts or replace the failed mechanical limit stop (if
necessary).