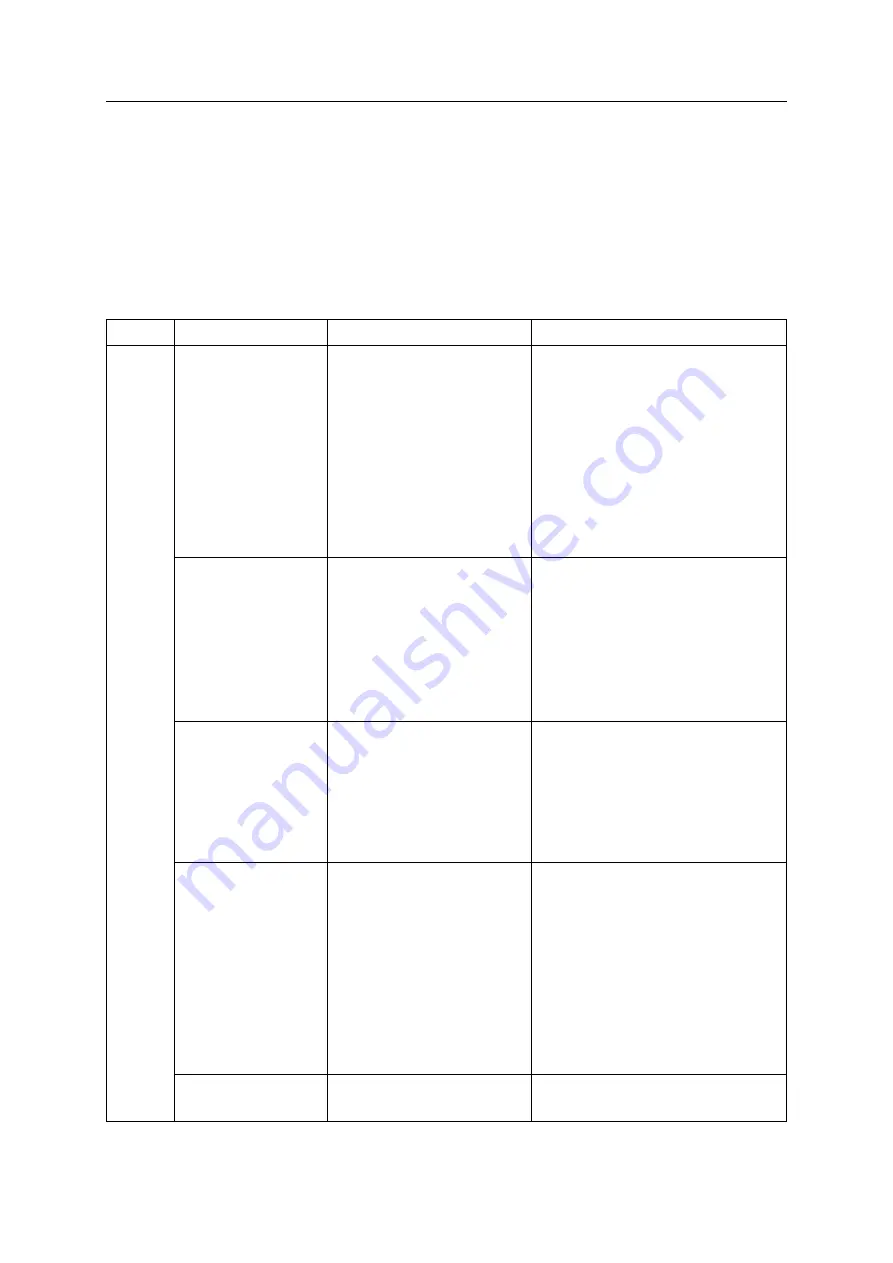
Mechanical Operation and Maintenance Manual for ER20-1100 Industrial Robot
40
Chapter 5 Common Faults and Troubleshooting
When robot body malfunctions, read this chapter to diagnose initial faults. The table
below covers common faults that may happen to robot body, possible reason analysis, and
corresponding troubleshooting techniques, which can help users to troubleshoot them. If faults
remain, please contact our service department.
Fault
Type
Possible reasons
Troubleshooting
Vibration
and
abnormal
noise
The robot base and the
mounting foundation are
not firmly fixed together.
(1) The robot base and the
mounting foundation are not flat
enough or objects are clamped in,
so they cannot fit firmly;
(2) Screws are not tightened in
connecting the robot base and the
mounting foundation, or the
screws are loosened after
long-term operation.
(1) Check and trim the flatness of the robot
base and the mounting foundation, so the
tolerance meets the installation
requirements;
(2) If objects appear between the robot base
and the mounting foundation, clear them
before reinstallation;
(3) Use a torque wrench to tighten the
screws with required torque.
The mounting
foundation and the
ground are not firmly
fixed together.
(1) The rigidity of ground is
insufficient, so the installing
conditions do not meet the
requirements;
(2) The specifications and strength
of chemical bolts do not meet the
requirements.
Refer to 3.2.3 Ground installation in this
manual, let the concrete foundation and
chemical bolt set meet installation
requirements.
The robot vibrates
obviously when a certain
gesture or state.
(1) load exceeding the limit leads
to insufficient stiffness in certain
gestures, so the vibration is arise;
(2) Improper programming and
parameter setting cause vibration.
(1) Decrease load and ensure it is within the
allowable range;
(2) Edit the program and adjust parameters.
Test from low-speed to high-speed mode
until the robot returns to normal operation
state.
The robot vibrates and
makes abnormal noise in
the following three
situations:
(1) after a collision;
(2) long-term overload
operation;
(3) long-term operation
without maintenance.
These situations can all cause the
damage of internal components
(gears, bearings, reducers, etc.),
leading to vibration and abnormal
noise.
(1) Check the robot axes by single-axis
motion and confirm the damaged joints, and
then consult after-sales service department
for replacement;
(2) Try to avoid collision and long-term
overload operation. Replace lubricant
according the maintenance requirements in
this manual.
The robot vibrates
because of the influence
(1) Resonance occurs when robot
and the peripheral devices
(1) Adjust the distance between the robot
and peripheral devices;