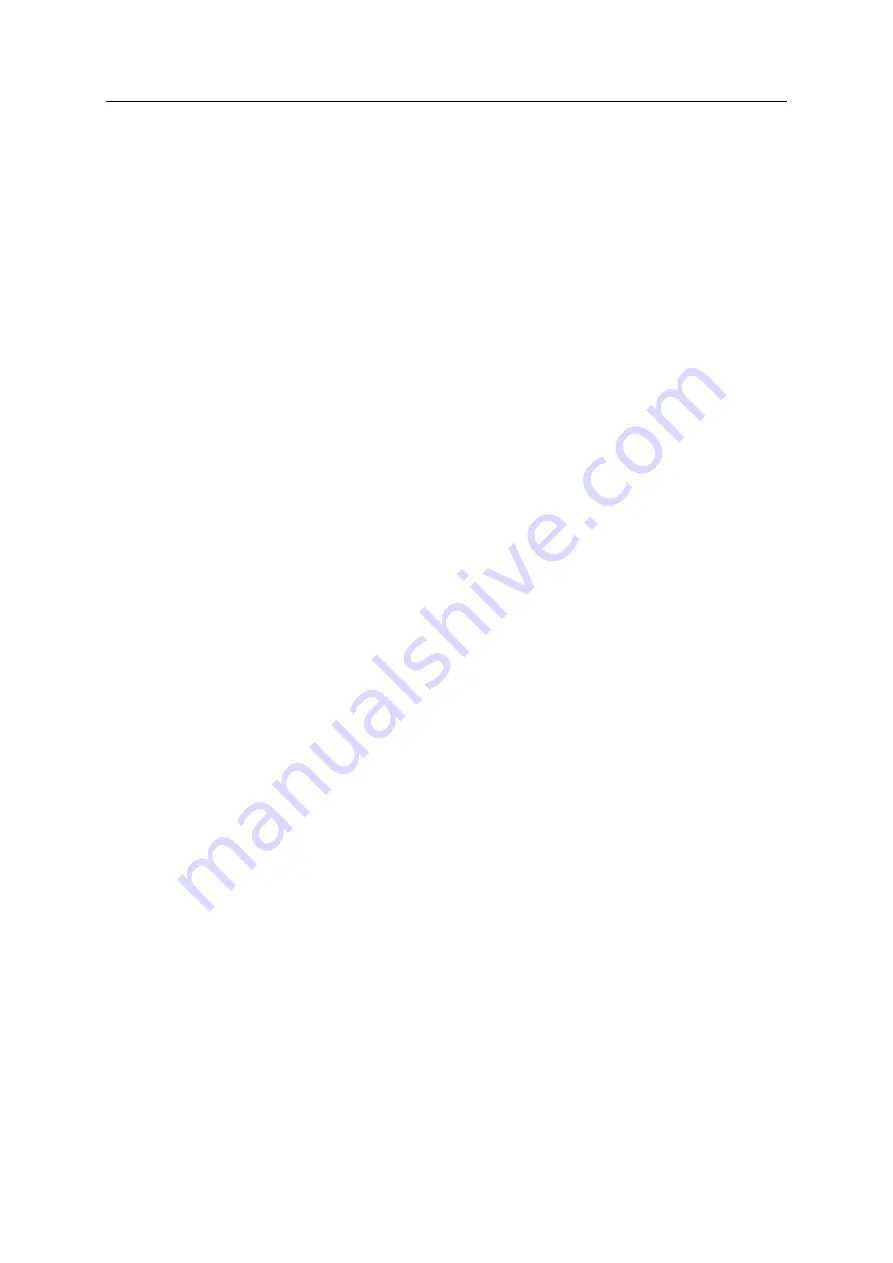
Mechanical Operation and Maintenance Manual for ER20-1100 Industrial Robot
III
4.5.2 Qualification requirements for maintenance personnel and precautions........... 36
.................................................................................37
4.6.1 Calibrating method of home position.................................................................37
4.6.2 Mechanical calibration of axis home position................................................... 38
...............................................................................................39
CHAPTER 5 COMMON FAULTS AND TROUBLESHOOTING....................................40
APPENDICES......................................................................................................................... 44
ORQUE TABLE OF TIGHTENING SCREW
.......................................................................... 44