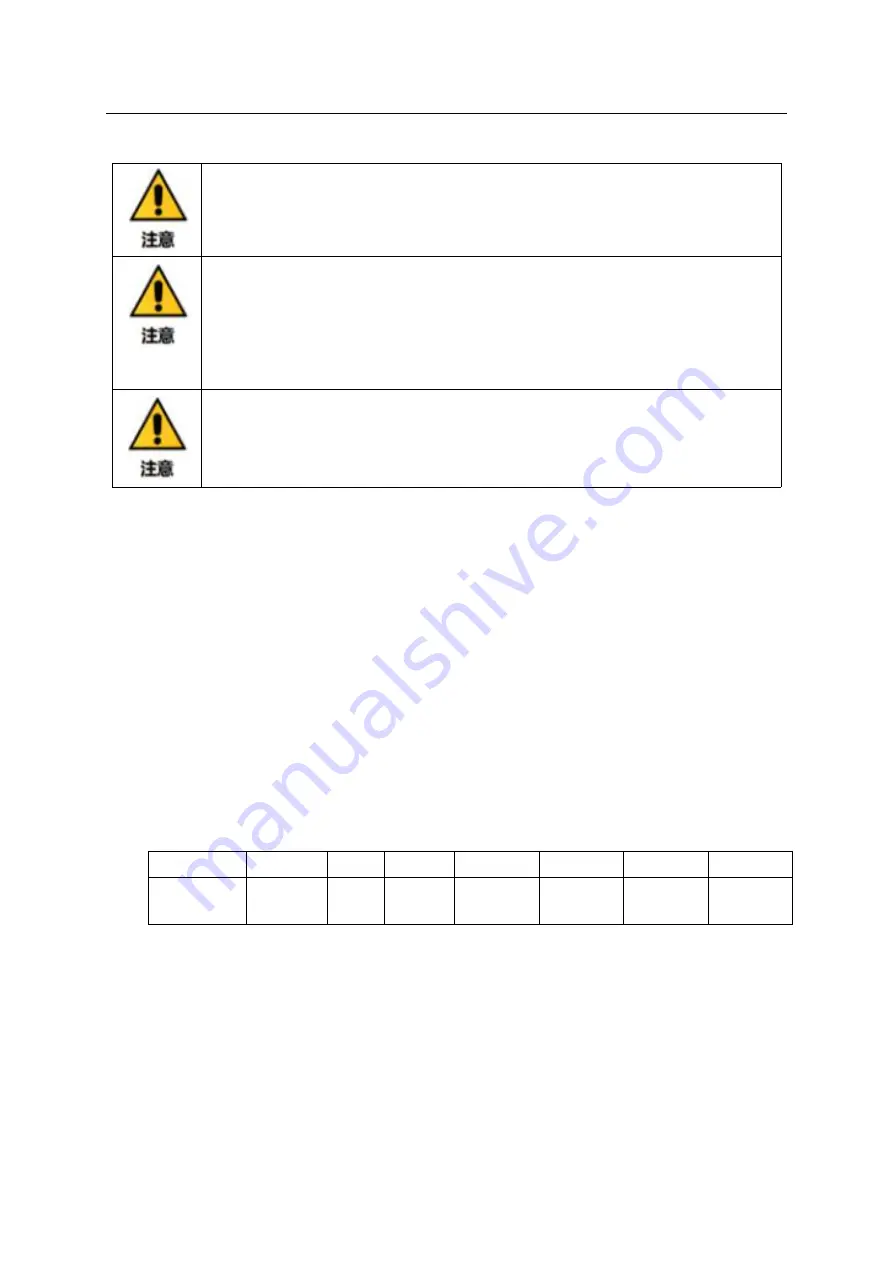
ER6-1400V1.01
Industrial Robot Quick Operation Manual
13
following contents before safe operation:
T
he handling of robots and control devices must be carried out by qualified personnel for
hook, lifting operation, forklift, etc. If the operators do not master the correct skills to
carry out the operation, it may lead to overturning, falling and other accidents.
When handling the robot and control device, please confirm the weight and steps
according to the method recorded in the manual. If the operation cannot be carried out
according to the specified method, the robot and control device may overturn or fall
during the handling process, resulting in accidents.
When handling and installing, pay attention to avoid damaging the wiring. In addition,
after the assembly of the device, protective measures such as covering with protective
cover should be taken to avoid damage to wiring by operators and forklifts.
2.3.2 Robot body handling
1) Handling method 1
When hanlinging the robot, first set the robot according to the posture shown in Fig. 2-3 and 2-4, then
install 4 M10 lifting ring screws on the main frame and lift it with four steel cables. It is suggested that the
length of the steel cable should not be less than 3m, and rubber hose should be put on the contact part
between the steel cable and the main body of the robot for protection.
Note: in Fig. 2-3 and Fig. 2-4, there are no other devices installed on the end effector and manipulator,
so please pay more attention once other devices are installed.
2
)
Handling method 2
Set the robot to the posture shown in the table below and use the forklift to carry.
The angle of each axis of the handling attitude and posture is set as follows:
Table 2-8 angle setting values of each axis of handling attitude
Model
Position
1 axis
2 axis
3 axis
4 axis
5 axis
6 axis
ER6-1400V
1.01
Joint
angle/°
0
+74.5
-74.5
﹢
90
﹢
90
0