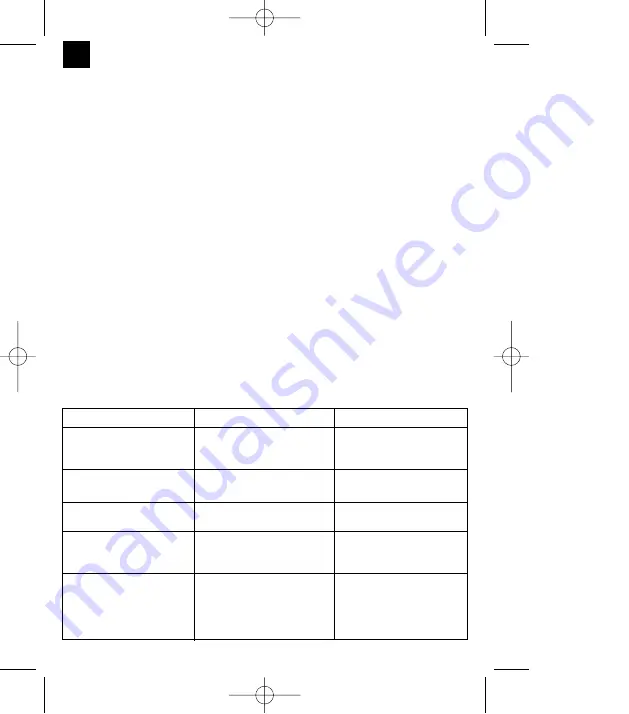
6
Important! Note!
●
Remove the mains plug before all
maintenance work.
●
In the event that the pump is
often transported in the course of
operation, it should be
cleaned out with clear water after
every use.
●
In case of stationary installation,
the function of the loating switch
should be checked every 3
months.
●
All fibrous particles which may
have built-up inside the pump
housing should be removed with
a water jet.
●
Every 3 months the shaft
ground and as should be
cleaned from mud.
●
Remove deposits on the floater
with clear water.
Cleaning the impeller
If excessive deposits collect in the
pump case you must dismantle
the bottom part of the pump as
follows:
1.
Undo the 4 screws from the
bottom of the intake cage.
2.
Remove the intake cage
from the pump case.
3.
Clean the impeller with clear
water.
Important! Do not put down or
rest the pump onthe impeller!
4.
Assemble in reverse order
Setting the ON/OFF opera-
ting point
The ON and OFF operating point of
the float switch can be set by adju-
sting the float switch in its latching
holder.
Before you put the pump into opera-
tion, please check the following:
●
The float switch must be installed
so that the level of the ON opera-
ting point and the level of the
OFF operating point can be rea-
ched easily and with little force.
To check this, place the pump in
a vessel filled with water, raise
the float switch carefully by hand
and then lower it again. As you
do so, note whether the pump
switches on and off.
●
Make sure that the distance bet-
ween the float switch head and
the latching holder is not too
small. Proper operation is not
guaranteed if the gap is too small.
●
When you set the float switch,
make sure that it does not touch
the base before the pump swit-
ches off. Caution! Risk of dry-run-
ning.
Incidents – Causes – Remedies
Incidents
Pumpe does not start
No flow
Pump does not switch off
Insufficient flow
Pump switches of after short
operating period
Causes
– No mains supply
– Floater does not switch
– Inlet sieve is clogged
– Pressure hose in bent
– Floater cannot sink down
– Inlet sieve is clogged
– Reduced pumping capacity by
dirty and abrasive water
– Thermal cutout stops pumps
due to dirty water
– Water too hot. Thermal-cutout
stops pump
Remedies
– Check mains supply
– Bring floater in a higher
position
– Clean inlet sieve water jet
– Reset hose
– Place pump properly on shaft
ground
– Clean inlet sieve
– Clean pump and replace
worn-out parts
– Remove mains plug. Clean
pump and shaft
– Make sure that a water tem-
perature of max. 35°C is not
exceed
GB
Anleitung ESP 460_1_Niro 30.01.2004 13:22 Uhr Seite 6