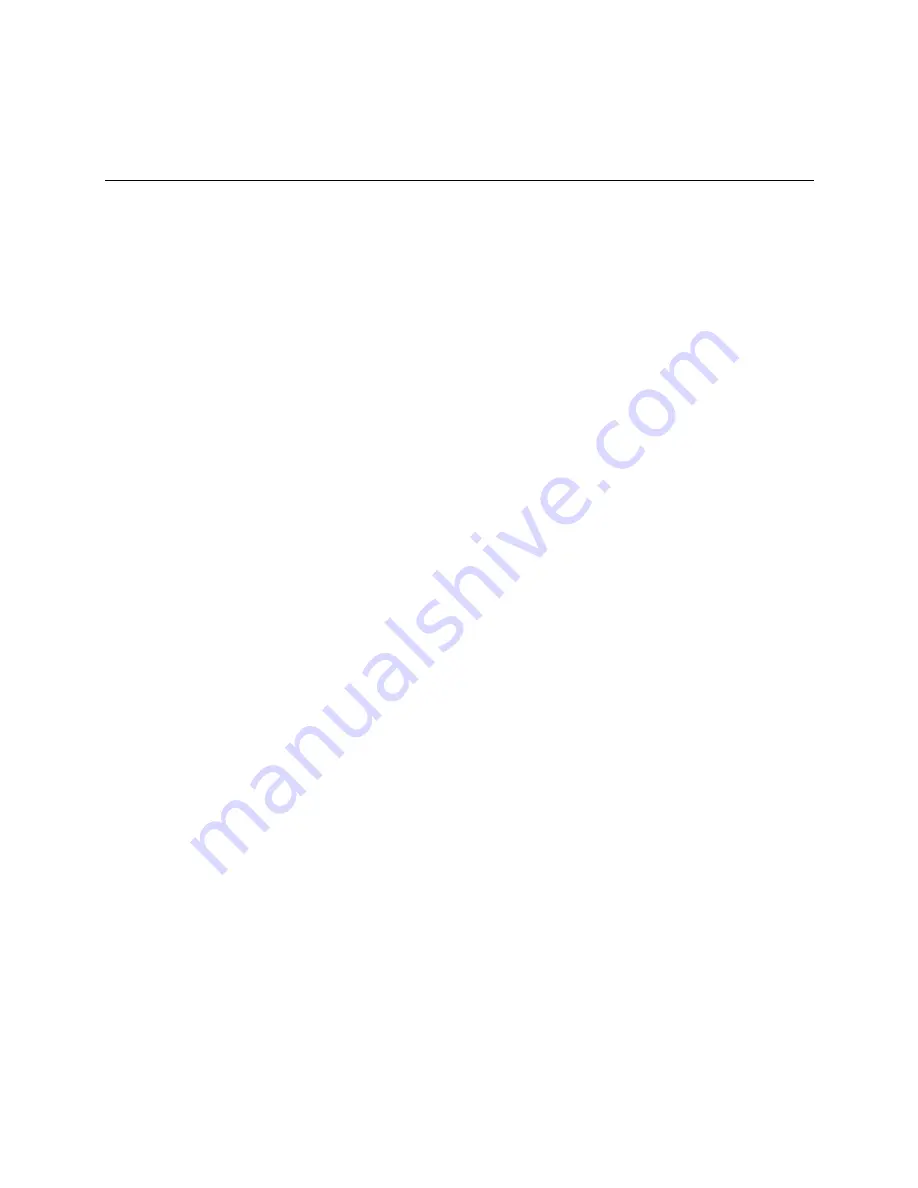
14
Installation
Gas connection
Gas connection
The gas lines and valves and instru-
ments group should be installed and
taken into operation in accordance with
the applicable engineering standards
and regulations.
The connection between the gas distri-
bution network and the gas ramp must
be done by authorised persons.
The section of the pipings must be cal-
culated so that the loss of load doesn’t
exceed 5% of the distribution pressure.
A quarter turn manual valve (not sup-
plied) must be provided for upstream of
the gas ramp and the filter.
The filter must be installed on a hori-
zontal nozzle with the cover in the verti-
cal position to enable cleaning.
The threaded unions used must be in
conformity with present standards
(tapered male thread, straight female
thread with sealing provided in the
thread).
Gas properties
Prior to any installation work make sure
to obtain the following data from the gas
supply company:
1.
type of gas
2.
calorific value Hu
n
=kW/m³ (kJ/m³)
3.
maximum CO
2
content of exhaust
gas
4.
gas connection pressure and rest
pressure
Type of gas test
Prior to mounting the burner to the gas
feed line check the available type of gas
and burner type against the data given
on the burner nameplate (attached to
burner). Be sure the description of the
burner and the type of gas are the
same as indicated on the nameplate.
Gas connection pressure
A minimum connection pressure must
be available upstream of the burner gas
valve to ensure the proper functioning
of the burner.
For the installation of the valves and
instruments group take care to observe
the mounting instructions supplied by
their manufacturers (these are packed
with the equipment).
The gas line installed to the burner
must be dimensioned in accordance
with the throughput rate and the availa-
ble pressure.
For selecting the nominal bore „DN“ of
the gas valves and instruments group
care should be taken to observe the
flue resistance of the boiler and the
gas pressure loss of the burner and
valves and instruments group.
Caution!
The absence of impurities and foreign
bodies must be checked before installa-
tion and commissioning of the gas
ramp, the lever valves and unions.
Gas valves and instruments
group
The gas valves and instruments group
can be connected directly to the gas
feed line.
Take care to observe the
correct order of installation and
direction of flow (arrow on housing).
Check the valves and instruments and
connection pieces for absence of dirt
particles and foreign matter before
installation and initial operation.
To pro-
vide effective conditions for start-up
make sure the distance between the
burner and the gas stop valve is as
short as possible.
Leak test
The gas line upstream of the burner gas
valves and instruments group must be
installed in accordance with the applica-
ble regulations, checked for absence of
leaks, vented and certified accordingly
by the gas installation company. The
screwed unions and flanged joints must
be checked for proper tightness (by
making a pressure test). The leak test
must be made under pressure using
approved foaming agents which do not
cause corrosion. For steam boiler fur-
naces the result of the leak test must be
duly certified.
Venting
Caution!
Prior to taking the burner into
operation or after any repair work make
sure to vent the complete gas feed line
and the gas valves and instruments
group into the open atmosphere (e.g.
by means of a hose) taking care to
avoid any hazards.
In no case should the gas line be
vented into the heating or furnace
chambers.
Make use of a test burner to check the
gas-carrying spaces are free from an
inflammable gas mixture.
Support
The valves and instruments group must
be supported with at least one telesco-
pic jacking member or similar during
and after installation (e.g. on filter and
valve).
Joint
It is recommended to provide an easy-
to-disconnect joint (with planar sealing
faces) to facilitate repair work on the
boiler (furnace) and allow the boiler
door to be swivelled out if required.
12/2011 14 072 205
Summary of Contents for Low-NOx N10.12000.30 G-EU2
Page 33: ...34 Manufacturer s declaration...