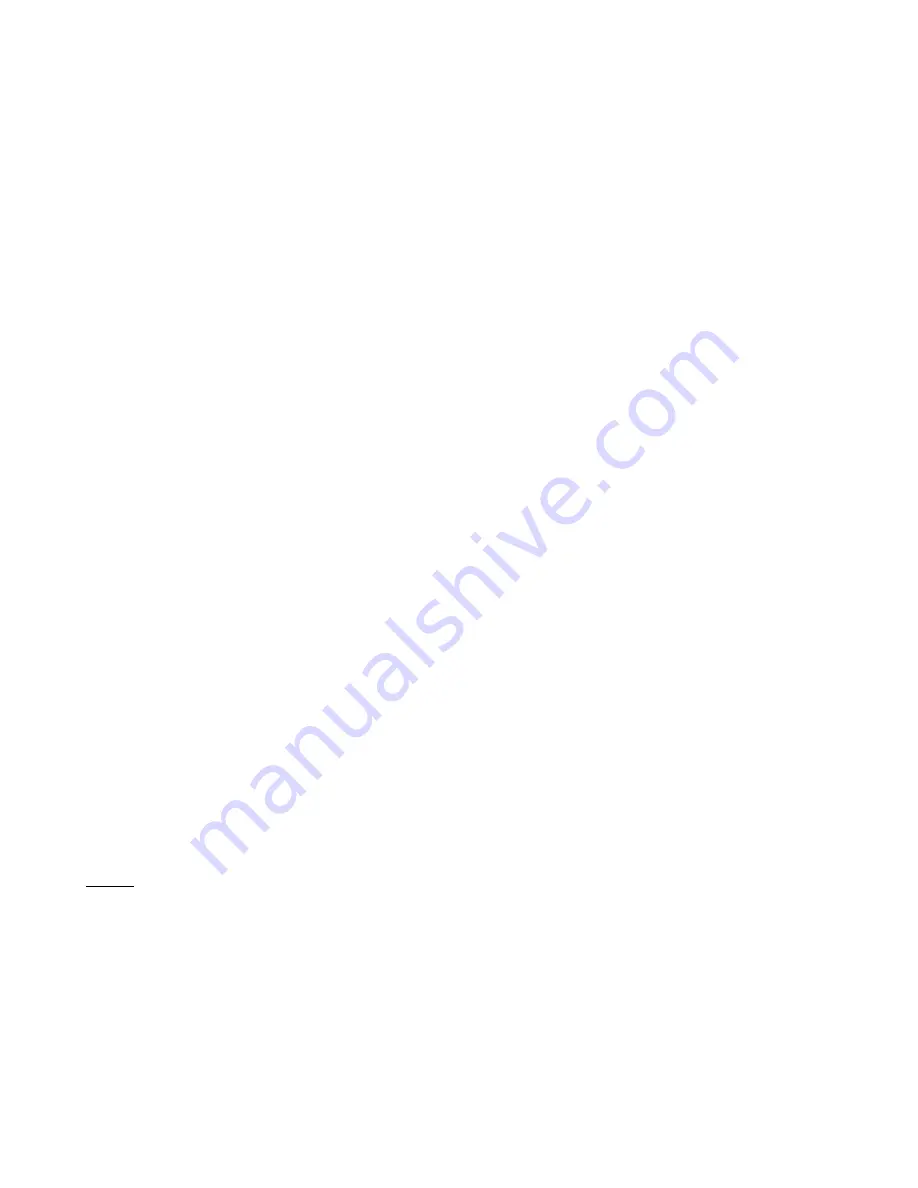
09/17/2014
6
BI308
Power robbing thermostats
– power robbing thermostats cannot be used with the EMB-H Mini-
Boiler.
6.
Load Management Interrupt Control
– this Mini-Boiler product has been pre-wired and designed for
a power company load management receiver connection. This should not be altered in any manner!
A.
Remove blue pigtail wires, wire-nut.
B.
Extend the blue and blue/white wires to the power company load control device.
As shipped, this unit is only equipped for off-peak = N.C. logic. If reversed logic is required,
contact the factory for modification.
Optional
– if load management is not used, simply leave the blues wire-nutted as shipped from
manufacturer. Also for Electro-Stat the load control connection is at the Electro-Stat “R” terminal.
Optional
– if the power company disconnects 240V for load control, please reference BH029 for
special wiring requirements.
7.
Zone Valve
– the installer may elect to totally wire in the zone valves where paralleling the end
switches activate the control board R and W. However, if using EB-5415 or other Electro Industries’
zone controller, wiring is substantially easier and the W OUT goes directly to W input (verify there is a
common on all secondary or auxiliary units). The EMB-H Series has a 40VA, 24-volt transformer
which is capable of driving 1 or 2 external zone valves. Again, generally zone controllers have their
own 24-volt transformer making this easier. Suggest adding zone interlock control, EB-5415A.
8.
Inspection/final check
– Verify all electrical connections are tight (including factory connections),
verify there is proper spacing between all power and electrical wire/terminals, and verify top high limit
manual reset is “in”. During shipping freight vibration there are times when the boiler vessel top
manual reset high limit is “popped out”.
WATER ADDITIVES
1.
Unless the source water is unusually poor and/or rust elements, additives are not required. It is
recommended the water source as shown on drawing BX305 comes through the household water softener.
2.
Impurities within a closed loop hydronics boiler are considerably less damaging than the typical domestic
water heater. In a closed loop electric boiler, the water impurities “boil out” and the system essentially
reverts to pure water. As a closed system, this “pure water” becomes the operating mode. In the case of
domestic water tank, there is always new water entering with new impurities.
3.
However, if additives are required, use the recommendations and source from your local professional
plumber, specializing in hydronics heating systems.
WATER FILL PROCEDURE
The following procedure only applies to the prepackaged plumbing kit and/or when the system is plumbed
exactly as shown on drawing BX305.
1.
Do not apply 24Ø volt heating power during water fill sequence.
2.
Connect the temporary household water supply source (probably hose connection) to the "supply water
connection" input.
NOTE
: If supply water connection is permanent, some local building codes may require special anti-
siphon check valve, PRZ check valve, or equivalent between the Mini Boiler fill regulator and the
domestic water source or the city water connection.
3.
Connect a drain hose to lower hose bib, "drain valve".
4.
Open
"drain valve" and
close
"inlet gate valve" (between drain valve and boiler bottom inlet).
5.
Verify “top gate valve” is
open
.