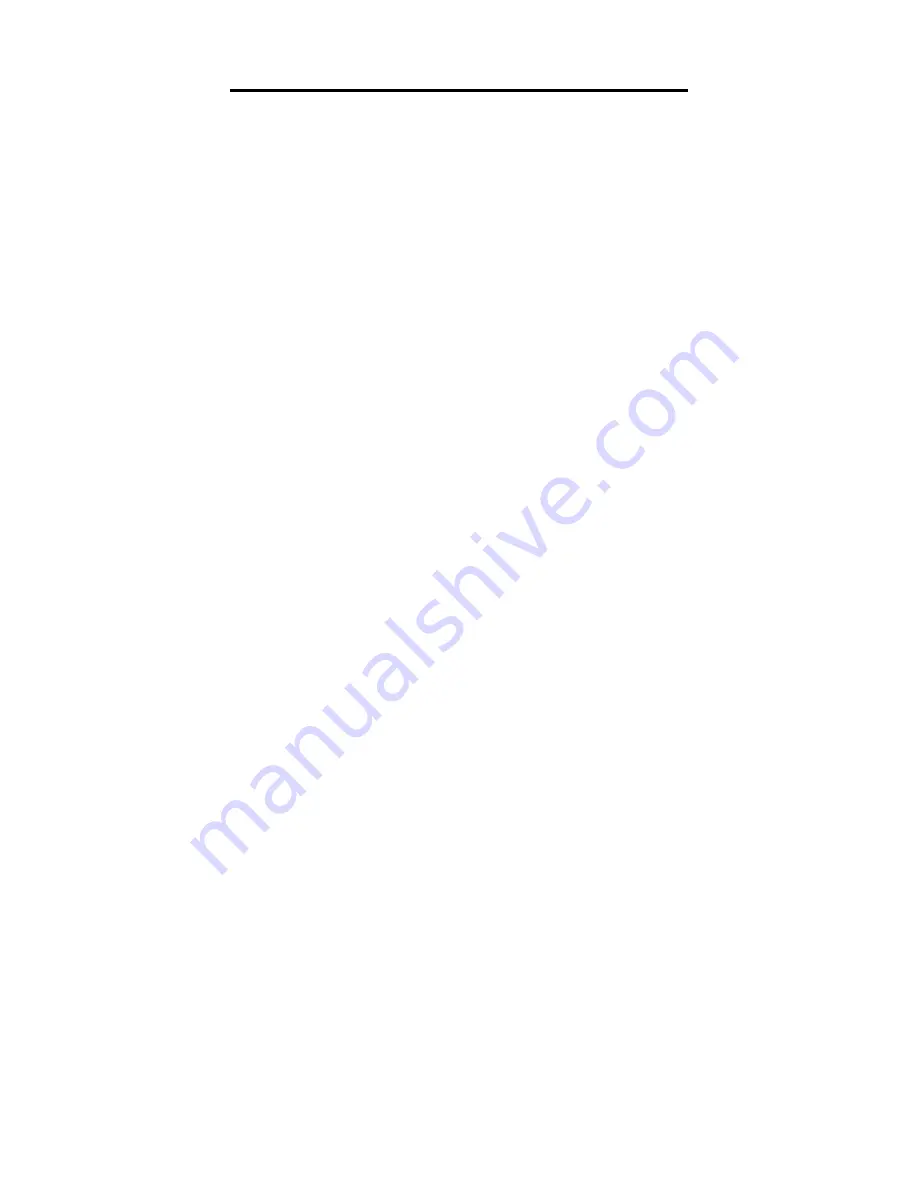
01/10/2008 6
HI321
WF-LGR4 & WF II WIRING & SETUP
WF-LGR4
Application
– Standard heat pump room thermostat, heat pump, WF II Electro-Mate, gas/oil furnace. HP
manufacturer’s fossil fuel kit is
not
required.
Reference Drawing HH340
1.
The provided 10-wire cable includes all connections and functions between WF-LGR4 and the WF II
main board within the Electro-Mate unit.
a.
The 10-pin connector on the main WarmFlo II board originated manufacturing date 08-
04-04 (ARL 3074). On the 10-pin connector may be a dummy cap plug, remove and
expose all 10 pins.
b.
If with this installation you do not have WarmFlo II main board with the 10-pin header,
you can either update the WarmFlo board or call factory for special instructions for
cutting up the cable and terminating with female ¼” tabs.
c.
If this installation is with the new upgraded WarmFlo and the new WF+ control board,
there is no thermostat, heat pump, furnace, load control wiring or field hookup on the
WF+ board. All thermostat, load control, etc. connections are on this separate enclosure
board. Even though the WF+ board is larger, when plugging in the 10-wire cable the
WF+ board functions identical to the normal WarmFlo II main board.
2.
All field connections and wiring from thermostat/heat pump/furnace are now are directly at this
controller, there are no bypass wires.
3.
Room Thermostat Connections
– upper left terminal block, 5 or 6-wire cable.
a.
Terminology is universal, should match most any heat pump room thermostat.
b.
The W at the roomstat is
not used
.
c.
Since this controller is single speed only, there should only be a Y1.
d.
Do not use
“dual fuel” or complex/sophisticated room thermostat.
e.
If you desire to use the roomstat emergency lever or function, you have a choice to
connect the “E” screw to either WF or GAS tab. Electro recommends WF (full plenum
heater output) and use the override switch in the front of this controller as your gas
switchover.
4.
Heat pump outdoor unit
– upper right terminal block, 4 or 5-wire cable. Terminology should be
universal, but some units provide colored wires only. Installer will need to match the wire color to
these lettered functions.
R – 24-volt power
C – 24-volt common
Y – compressor contactor coil
RV (O) – reversing valve, typically orange
a.
As an option (if the installer is absolutely confident of this function), the defrost output
wire can be connected to DF (W1) tab to increase the plenum heater kW output (all
stages on immediate) when the outdoor unit initiates defrost.
b.
Since this controller can only be used for single speed equipment, there should only be a
single Y function.
c.
These are the only connections or wires needed from the outdoor unit.
5.
Furnace terminal block
– bottom center terminal block, 4 or 5-wire cable. Terminology should be
universal.
a.
The Y is only needed for variable speed, ECM motor, type blowers.
b.
The power for this controller and the Electro-Mate/WarmFlo comes from the furnace
transformer and is R and C at this bottom terminal block.
6.
Utility Load Control
– if utility load control applies, remove the blue jumper from the bottom left
terminal block and connect the utility NC contact receiver or device.
a.
If opposite control logic is required, contact factory for other wiring instructions.
Summary of Contents for WARMFLO II
Page 28: ......