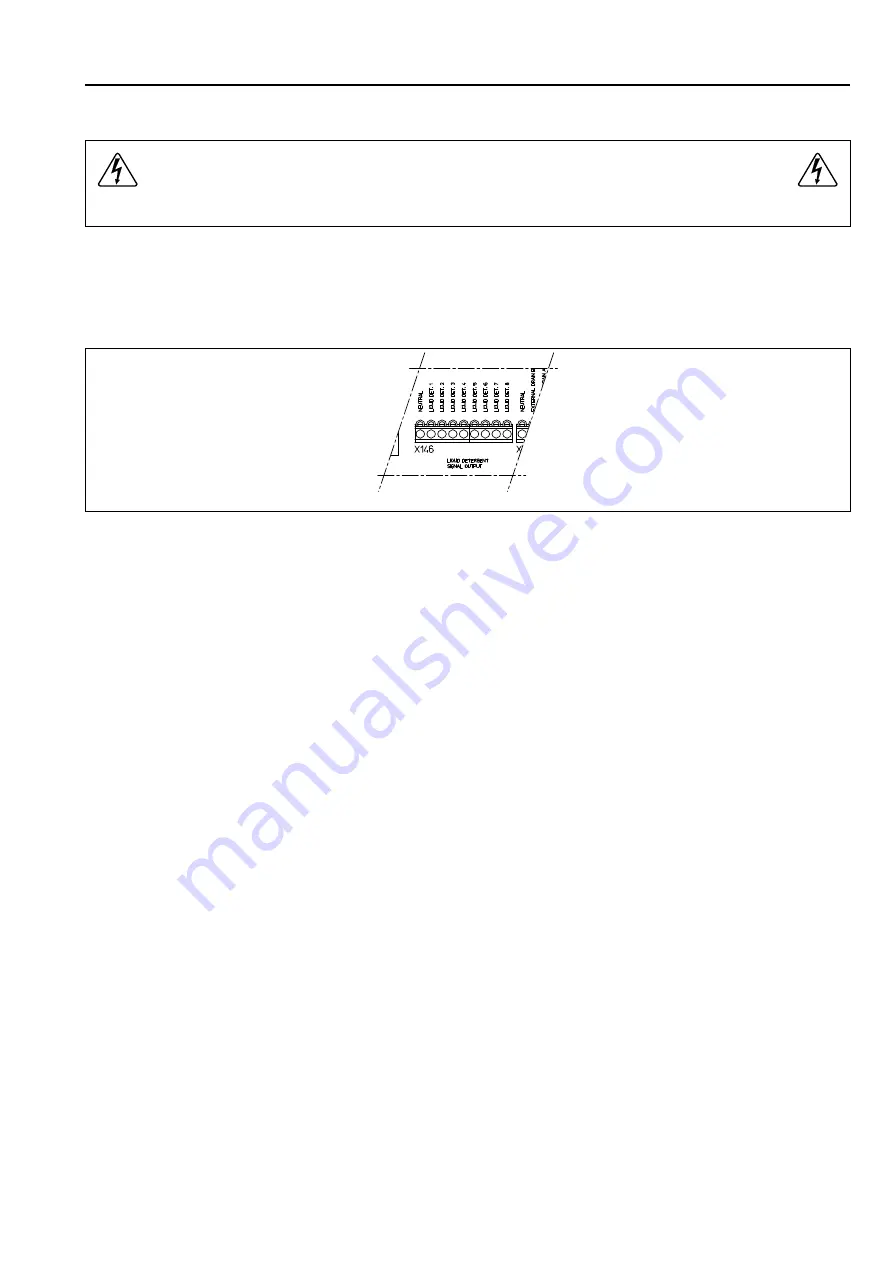
Installation manual
27
11.2 Electrical connection of external dosing system
The electrical installation may only be carried out by qualified personnel.
The external dosage unit connects to the X146 via the upper terminal in the coin operation unit. There are a total of 8
outlets for the dosing of washing detergent. The number on the terminal corresponds to the numbering of the liquid
detergent function when setting the wash program.
A common zero for all the outlets can be found on the X146 terminal ”Neutral”. 230 V max 0.5 A only intended for
control voltage. If the machine is not fitted with a detergent container, then additional signals can be received from
X140.
fig.6527
Summary of Contents for W4 H Series
Page 2: ......
Page 4: ......
Page 39: ......
Page 40: ...Electrolux Professional AB 341 80 Ljungby Sweden www electroluxprofessional com ...