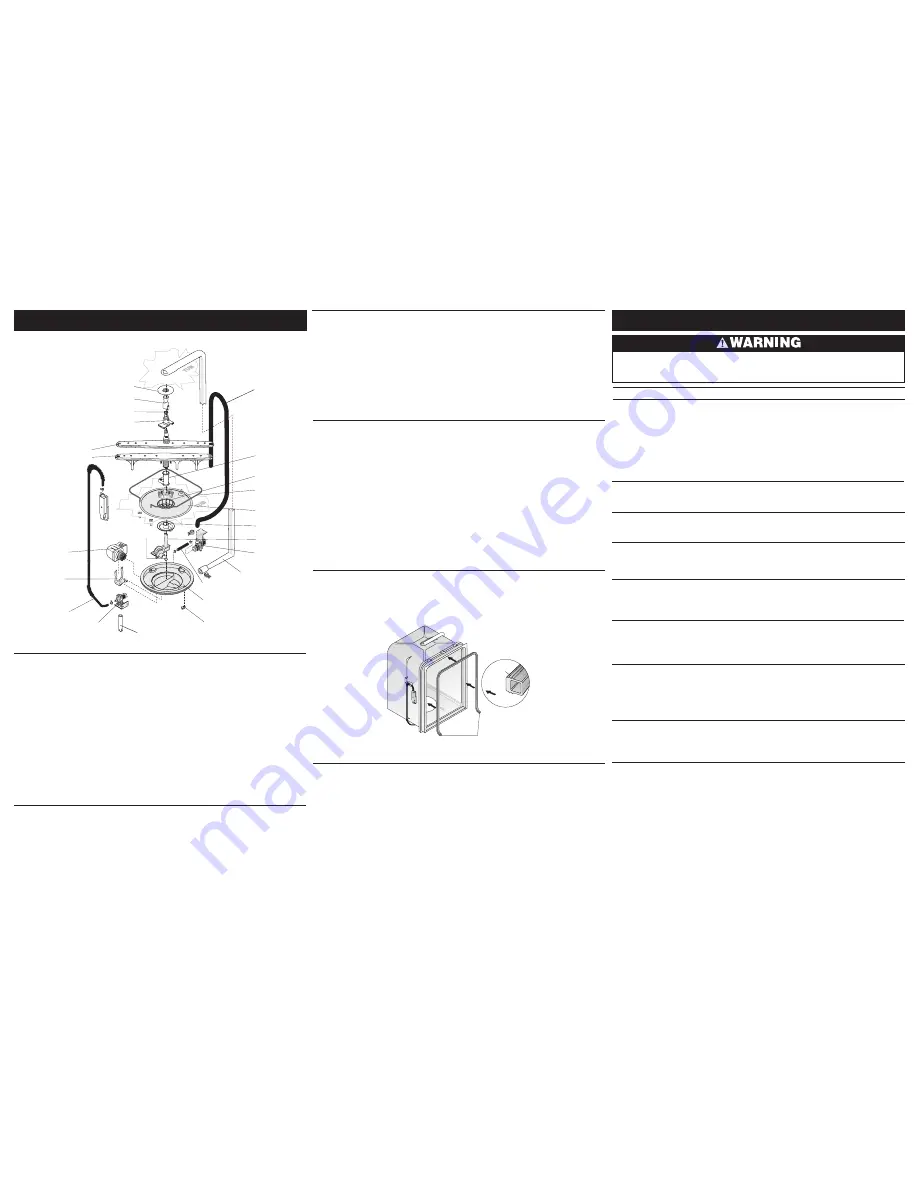
Trouble Shooting Tips
Exploded View of Wash System
Tub and Door Seal
The door seal is pressed into the tub channel for
an interference fit. Center the gasket (marked on
back) at the tub top center and press in place
Product Specifications
Electrical
Rating ................................... 120 Volts, 60Hz
Separate Circuit..15 amp min.- 20 amp max.
Motor (Amps) ........................................... 0.6
Heater Wattage ....................................... 900
Total Amps (load rated) ......................... 10.0
TempAssure .............................. 140°F ±5°F
(60°C±3°C) [with outer door in place]
TempBoost ............. 145°F ±5°F (63°C ±3°C)
Heated Wash/Heated Rinse
Sanitize .................. 155°F ±5°F (66°C ±3°C)
Hi-Limit Thermostat ................ 200°F (93°C)
Water Supply
Suggested minimum incoming water
temperature ............................. 120°F (49°C)
Pressure (PSI) min./max. ................... 20/120
Connection (NPT) .....................................
3
/
8
"
Consumption (Normal Cycle) .......................
............. 4.9 - 9.7 U.S. gal., 18.5 - 36.7 liters
Water valve flow rate (U.S. GPM) ........... .83
Water recirculation rate (U.S. GPM) ..............
.................................................... approx. 12
Water fill time ..................................... 87 sec.
To replace dispenser:
• shut off electricity to dishwasher,
• remove outer door panel assembly,
• disconnect wiring to the actuator,
• remove the six screws,
• remove the dispenser,
• replace and reinstall screws,
• rewire actuator.
Check the Following
1. Fuse (blown or tripped).
2. 120 VAC supply wiring connection
faulty.
3. Electronic control board defective.
4. Motor (inoperative).
5. Door switch (open contacts).
6. Door latch not making contact with
door switch.
7. Touch pad circuit defective.
8. No indicator lamps illuminate when
START or OPTIONS are pressed.
1. Motor (bad bearings).
2. Motor stuck due to prolonged
non-use.
1. Improper voltage.
2. Motor windings shorted.
3. Glass or foreign items in pump.
1. Heater element (open).
2. Electronic control board defective.
3. Wiring or terminal defective.
4. Hi-Limit thermostat defective.
1. Latch mechanism defective.
2. Electronic control board defective.
3. Wiring or terminal defective.
4. Broken spring(s).
5. Defective actuator.
1. Drain restricted.
2. Electronic control board defective.
3. Defective drain pump.
4. Blocked impeller.
5. Open windings.
6. Wiring or terminal defective.
1. Water supply turned off.
2. Defective water inlet fill valve.
3. Check fill valve screen for
obstructions.
4. Defective float switch.
5. Electronic control board defective.
6. Wiring or terminal defective.
7. Float stuck in “UP” position.
1. Drain hose (high) loop too low.
2. Drain line connected to a floor drain
not vented.
1. Detergent allowed to stand too long in
dispenser.
2. Dispenser wet when detergent was
added.
3. Detergent cover held closed or blocked
by large dishes.
4. Improper incoming water
temperature to properly dissolve
detergent.
5. See "Detergent cover will not open."
Always disconnect the dishwasher from the electrical power source before adjusting or
replacing components.
Personal Injury Hazard
900 Watt Heater
Refer to the cycle chart on the reverse side to
determine when the heater is on during the wash
cycle. The heater cycles
ON
and
OFF
for brief
periods during the drying cycle.
Voltage checks of the heater should be made in
the dry portion of the service test mode.
is attached by a worm gear clamp to the discharge
end of the drain pump.
The drain hose must have a loop at a
minimum
height of 32 inches
in order to insure proper
drainage.
The main pump can easily be removed by
disconnecting the upper spray arm supply tube
hose, the drain pump connector hose, the wiring
harness connections made at the circulation
motor, the water heat thermistor located on the
bottom of the pump and rotating the four sump
retainers toward the middle of the sump.
Pump Assembly
The pump assembly is driven by a synchronous
motor. Rotation is in the counterclockwise
direction at 3600 RPM. The motor drives a pump
which supplies 100 percent filtered water at a
rate of approximately 12 GPM to one spray arm
at a time. The spray arm’s operation is alternated
by small “pauses” of the motor during the wash
cycle.
Draining is accomplished by using a small
separate synchronous drain pump mounted to
the side of the sump. The drain pump is
connected to the main pump by a small rubber
hose. The drain check valve is located at the
discharge end of the drain pump. The drain hose
without stretching or bunching. The gasket takes
a short turn at the bottom of the tub channel
before ending at the channel end wall.
Short Turn
Gasket Cross Section
Detergent and Rinse Aid Dispenser
The detergent and rinse aid dispenser is a one
piece component consisting of a molded
detergent cup and a built-in rinse aid dispenser.
The detergent cup has a spring loaded cover
and the rinse aid dispenser has a removable
cover.
Liquid rinse aid is added to the dispenser up to
the fill line indicator. The amount of rinse aid
released can be adjusted by turning the arrow
indicator from one, being the least amount, to
four, being the greatest amount.
Mounting
Rib
Tub
Interior
Remedy
1. Replace fuse or reset breaker.
2. Repair or replace wire fasteners at
dishwasher junction box.
3. Replace control module.
4. Replace motor/impeller assembly.
5. Replace latch assembly.
6. Replace latch assembly.
7. Replace console assembly.
8. Replace console assembly.
1. Replace motor assembly.
2. Rotate motor impeller.
1. Check voltage.
2. Replace motor/impeller assembly.
3. Clean and clear blockage.
1. Replace heater element.
2. Replace control module.
3. Repair or replace.
4. Replace thermostat.
1. Replace dispenser.
2. Replace control module.
3. Repair or replace.
4. Replace dispenser.
5. Replace dispenser.
1. Clear restrictions.
2. Replace control module.
3. Replace pump.
4. Check for blockage, clear.
5. Replace pump assembly.
6. Repair or replace.
1. Turn water supply on.
2. Replace water inlet fill valve.
3. Disassemble and clean screen.
4. Repair or replace.
5. Replace control module.
6. Repair or replace.
7. Clean float.
1. Repair to proper
32-inch minimum
height
.
2. Install air gap at counter top.
1. Instruct customer/user.
2. Instruct customer/user.
3. Instruct customer/user on proper
loading of dishes.
4. Incoming water temperature of
120°F is required to properly
dissolve dishwashing detergents.
Symptom
Dishwasher will not operate when
turned on.
Motor hums but will not start or run.
Motor trips out on internal thermal
overload protector.
Dishwasher runs but will not heat.
Detergent cover will not latch or
open.
Dishwasher will not pump out.
Dishwasher will not fill with water.
Dishwasher water siphons out.
Detergent left in dispenser.
Standard Dry Air Flow
When the control advances to the “dry” portion of
the cycle, a linear actuator retracts a valve, which
opens a vent path through the console into the
kitchen. The heated, moist air leaving the
dishwasher through the console vent causes
drier air to be drawn into the unit by way of intake
020905
Nozzle
Funnel
Nut
Funnel Base
Center Spray Arm
Lower Spray Arm
Delivery Tube
Connector Hose and Clamps
Sump
Water Valve
Water Inlet Tube
Check Ball
Circulation
Motor Assembly
Motor Bracket
Incoming Water Supply
Drain Hose
(32" minimum
height)
Spray Arm
Support
Glass Trap
Heating
Element
Filter
Soil Director
Volute Cover
Drain Motor
Sump Retainers (4)
vents located at the bottom of the door. The water
on the dishes is evaporated into drier air and the
venting process continues. The heating element
is turned
ON
and
OFF
during the entire drying
cycle.
B - 4
Summary of Contents for FDB1050RE 2005
Page 33: ...B 1 ...
Page 35: ...B 3 ...