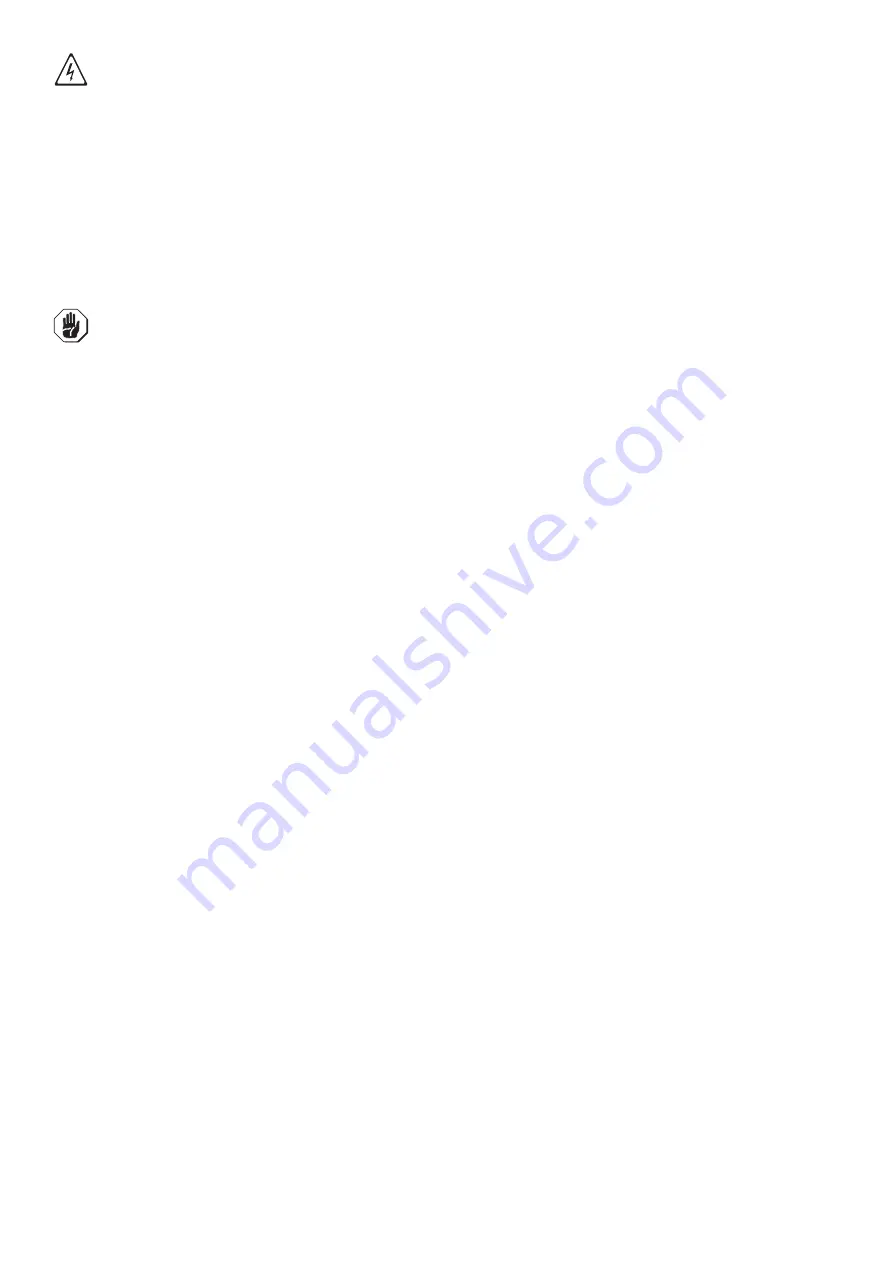
10
ATTENTION!
For protection against indirect contacts (depending on the type of supply foreseen and the con-
nection of the masses to the equipotential protection circuit) refer to par. 6.3.3 of EN 60204-1
(IEC 60204-1) with the use of protection devices that ensure automatic disconnection of the
power supply in the event of an insulation fault in TN or TT systems, or, for IT systems, the use of
isolation controllers or differential current protection devices to start automatic disconnection of
the power supply (except when a safety device is provided to disconnect the power in case of a
first fault to earth, an isolation controller must be provided to indicate the occurrence of a first
fault by a live part to the masses or to earth. This device must activate an audible and/or visual
signal which must continue for the duration of the fault).
For example, in a TT system it is necessary to install a differential circuit breaker upstream of the
supply with intervention current coordinated (e.g. 30 mA) with the earthing system of the building
where the machine is to be installed.
ATTENTION!
The Customer is requested to follow these instructions, otherwise the Manufacturer does not
guarantee the machine for continuous operation and/or against faults.