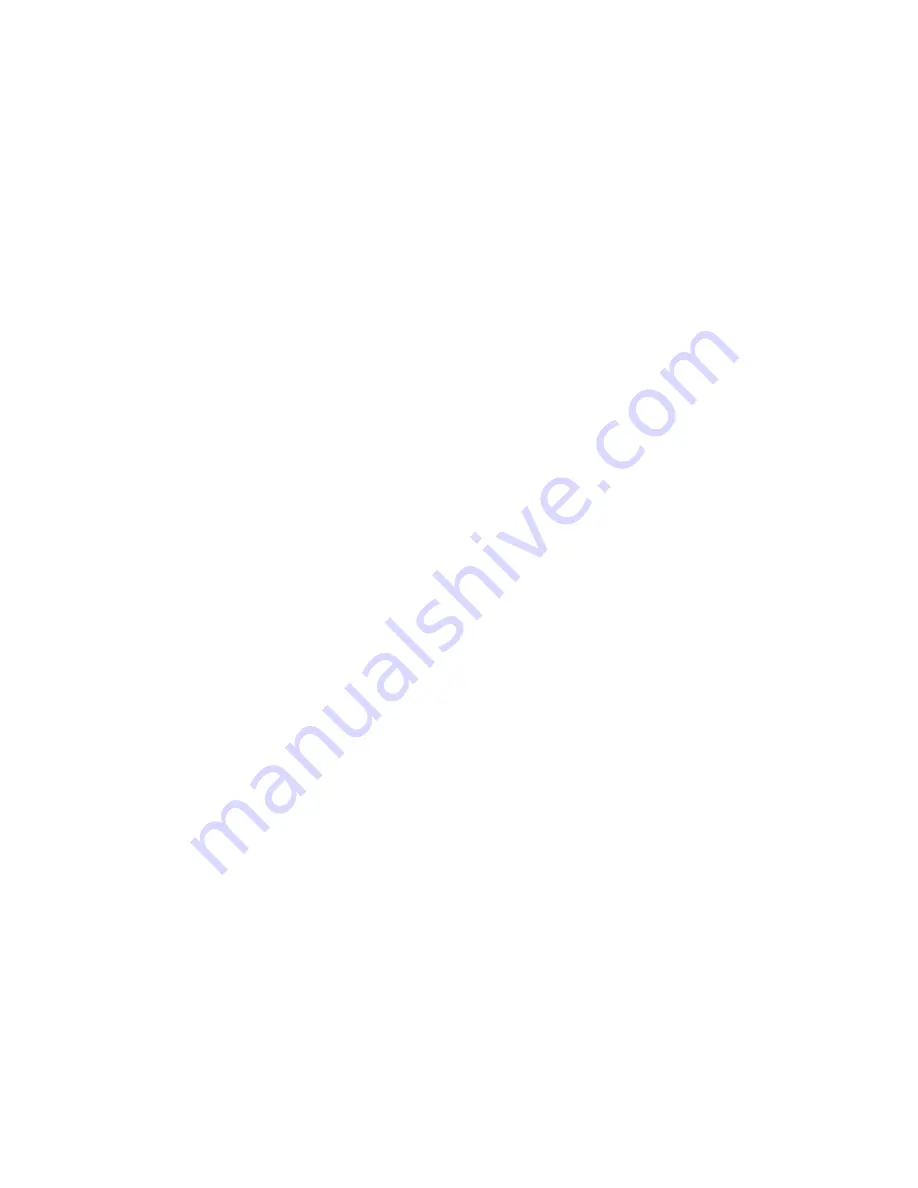
10
The EC Conformity Declaration provided with the
machine also envisages these configurations. The
Manufacturer does not provide for the possibility of
making other constructional modifications to the
machine, but allows the execution of other types of
combinations with systems different from those
described above (in order to create a series of
machines arranged and controlled in an integral way),
as illustrated in this documentation.
In which case it is necessary to comply with provisions
of the applicable European Directives or current regu-
lations in the country of use, and obtain the required
certifications. The Manufacturer declines any liability
for damage caused by arbitrary modifications and con-
versions carried out by the user or third parties. For
requests or for further information, contact Electrolux
Professional S.p.A. - Via Treviso, 15 - 33170 Porde-
none - Italy.
A11
Users of the manual
This manual is intended for:
•
the carrier and handling personnel;
•
installation and start-up personnel;
•
the employer of machine users and the workplace
manager;
•
operators in charge of normal machine use;
•
specialized technicians - technical assistance (see
wiring diagram and service manual).